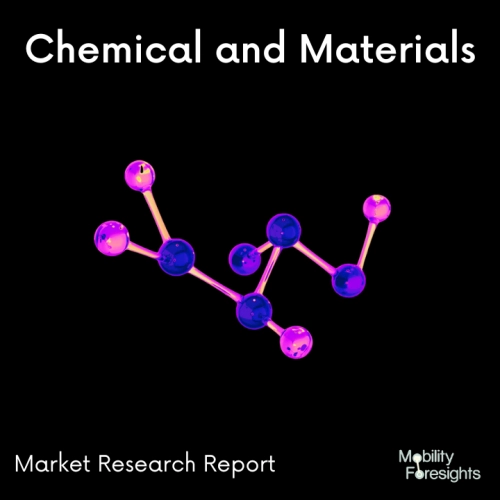
- Get in Touch with Us
Last Updated: Apr 25, 2025 | Study Period: 2024-2030
2 reactive adhesives and structural adhesives are other names for component adhesives. They are distinguished by the fact that they heal not through the evaporation of a substance like water or a solvent, but rather through a chemical reaction.
It is absolutely necessary for the two necessary components to be mixed homogeneously, or evenly, and dosed in the appropriate mixing ratio. It is ideal for 2âcomponent cements to be dissolvable free.
For applications where adhesive joints are expected to have very high strengths, these structural adhesives are the best choice.
These structural adhesives are mostly used to join high-strength materials like bare, coated, painted, or pre-treated metals, composite materials like glass-reinforced plastics (GRP + SMC) or carbon fiber-reinforced plastics (aramid, carbon, and CFC), and solid materials like ceramics or glass.
2 component adhesives necessitate a unique method of operation. Working from double-chamber cartridges, also known as side-by-side cartridges, has proven to be a successful method in addition to manual or mechanical dosing and mixing.
The two components are packaged separately in these cartridges. Depending on the recipe, there are mixing ratios of 1:1, 2:1, or 10:1 parts per volume.
The two parts are pressed in equal amounts through a static mixer (mixing tube) by dispenser guns that are appropriate.
These guns can be manual or pneumatic. After that, the ready-to-work mixture is immediately applied to one of the materials that need to be joined. After that, the second material can be joined together, and the parts only need to be fixed when the adhesive is dry.
The Global Two-Component Conductive Adhesives market accounted for $XX Billion in 2023 and is anticipated to reach $XX Billion by 2030, registering a CAGR of XX% from 2024 to 2030.
The Volex Dynamic Mix Valve was recently introduced by Graco Inc., a manufacturer of fluid handling equipment.
The new mix valve provides uniform and consistent blending for difficult-to-dispense materials for a variety of applications. It was made for dispensing two-component adhesives like foaming urethanes and silicones.
The Volex valve is designed to deal with silicones and foaming urethanes, which are notoriously difficult to work with due to their rapid reactivity and expanding nature.
In situations like these, the dispensing process and equipment are crucial for avoiding poorly mixed materials and potential downtime.
To address these issues, the Volex valve from Graco features innovative error detection technology, disposable mixing elements, a dependable servo-electric motor, and durable seals and check valves.
This valve has already shown that it can be used in new applications, like the battery industry for electric vehicles (EVs).
This valve is a valuable addition to the meter, mix, and dispense equipment lineup. The simple design, combined with Graco's technical excellence and known quality.
The valve is already a crucial component of the dispensing procedure for several battery manufacturers thanks to Graco's well-established relationships with material suppliers and proven complete solution.
This complete dispensing solution meets the requirements of numerous applications in emerging markets thanks to precise control at each corner of the meter, mix, and dispense process.
The Volex Dynamic Mix Valve is a dependable solution that can handle challenging material and application requirements for everything from filter sealing and automotive bonding to appliance gasketing and battery potting.
Sl no | Topic |
1 | Market Segmentation |
2 | Scope of the report |
3 | Abbreviations |
4 | Research Methodology |
5 | Executive Summary |
6 | Introduction |
7 | Insights from Industry stakeholders |
8 | Cost breakdown of Product by sub-components and average profit margin |
9 | Disruptive innovation in the Industry |
10 | Technology trends in the Industry |
11 | Consumer trends in the industry |
12 | Recent Production Milestones |
13 | Component Manufacturing in US, EU and China |
14 | COVID-19 impact on overall market |
15 | COVID-19 impact on Production of components |
16 | COVID-19 impact on Point of sale |
17 | Market Segmentation, Dynamics and Forecast by Geography, 2024-2030 |
18 | Market Segmentation, Dynamics and Forecast by Product Type, 2024-2030 |
19 | Market Segmentation, Dynamics and Forecast by Application, 2024-2030 |
20 | Market Segmentation, Dynamics and Forecast by End use, 2024-2030 |
21 | Product installation rate by OEM, 2023 |
22 | Incline/Decline in Average B-2-B selling price in past 5 years |
23 | Competition from substitute products |
24 | Gross margin and average profitability of suppliers |
25 | New product development in past 12 months |
26 | M&A in past 12 months |
27 | Growth strategy of leading players |
28 | Market share of vendors, 2023 |
29 | Company Profiles |
30 | Unmet needs and opportunity for new suppliers |
31 | Conclusion |
32 | Appendix |