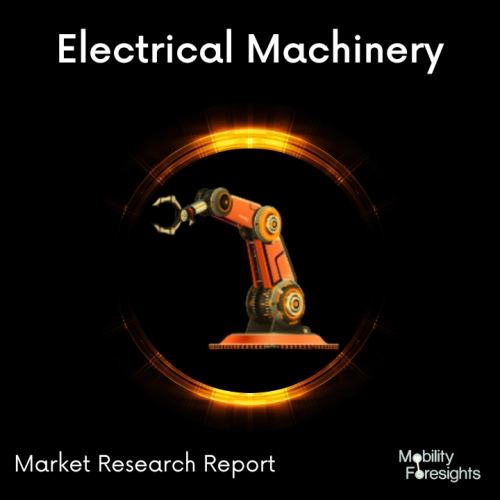
- Get in Touch with Us
Last Updated: Apr 25, 2025 | Study Period: 2024-2030
Generally, according to the machining accuracy, machining can be divided into three stages: general machining, precision machining, and ultra-precision machining. Ultra-precision machining refers to sub-micron and nanoscale precision machining.
The process methods and technical measures taken to realize these processing are called ultra-finishing technology. Coupled with measurement technology, environmental protection and materials and other issues, this technology is generally referred to as ultra-precision engineering.
Ultra-precision machining mainly includes three fields: ultra-precision machining of diamond tools, which can process various mirror surfaces. It has successfully solved the processing of large parabolic mirrors for laser fusion systems and astronomical telescopes; ultra-precision grinding processing such as coating surface processing of high-density hard disks and processing of large-scale integrated circuit substrates; ultra-precision special processing such as large-scale integrated circuit wafers are processed by electron beam and ion beam etching methods, and the line width can reach 0.1µm.
If processed by scanning tunneling electron microscope, the line width can reach 2-5nm. three different types of machining exist: ordinary, precision, and ultra-precision. Sub-micron and nanoscale precision machining is referred to as ultra-precision machining.
The techniques used to carry out these processes are referred to as ultra-finishing technology. This technique is frequently referred to as ultra-precision engineering when it is combined with measurement technology, environmental protection, materials, and other concerns.
The three main areas of ultra-precision machining are as follows: diamond tool ultra-precision machining, which can handle different mirror surfaces. Large parabolic mirror processing for laser fusion systems and astronomical telescopes, ultra-precision grinding processing, such as coating hard disc surfaces and processing large integrated circuit substrates, ultra-precision special processing, such as large integrated circuit wafer processing by electron beam and ion beam etching methods, have all been successfully resolved.
The Global Ultra High Precision Grinding machine market accounted for $XX Billion in 2022 and is anticipated to reach $XX Billion by 2030, registering a CAGR of XX% from 2024 to 2030.
Engis Corp. of Wheeling, has launched the EVG Series of ultra high-precision vertical grinding machines for the creation of ultra-smooth surfaces. The equipment is built to grind complex materials with extreme accuracy in flatness and surface quality, considerably lowering or even doing away with the requirement for subsequent lapping and going straight from grinding to final polish.
Three different variants of the new machines are offered, and each includes a programmable logic controller, a 400-rpm work-table speed, and a 2000-rpm wheel speed. With the EVG-200, sizes range from 800 x 800 x 1900 to 1050 x 1050 x 2020.
Each one has been ergonomically constructed, with simple access to the work surface and a range of chuck alternatives. There are sophisticated machine control options that enable automated workpiece thickness measurement, automatic dressing of the grinding wheel, and automated positioning of the grinding wheel in relation to the workpiece. An update to in-process thickness measuring with real-time feedback to the grinding cycle is also available for optimal control.
Sl no | Topic |
1 | Market Segmentation |
2 | Scope of the report |
3 | Abbreviations |
4 | Research Methodology |
5 | Executive Summary |
6 | Introduction |
7 | Insights from Industry stakeholders |
8 | Cost breakdown of Product by sub-components and average profit margin |
9 | Disruptive innovation in the Industry |
10 | Technology trends in the Industry |
11 | Consumer trends in the industry |
12 | Recent Production Milestones |
13 | Component Manufacturing in US, EU and China |
14 | COVID-19 impact on overall market |
15 | COVID-19 impact on Production of components |
16 | COVID-19 impact on Point of sale |
17 | Market Segmentation, Dynamics and Forecast by Geography, 2024-2030 |
18 | Market Segmentation, Dynamics and Forecast by Product Type, 2024-2030 |
19 | Market Segmentation, Dynamics and Forecast by Application, 2024-2030 |
20 | Market Segmentation, Dynamics and Forecast by End use, 2024-2030 |
21 | Product installation rate by OEM, 2023 |
22 | Incline/Decline in Average B-2-B selling price in past 5 years |
23 | Competition from substitute products |
24 | Gross margin and average profitability of suppliers |
25 | New product development in past 12 months |
26 | M&A in past 12 months |
27 | Growth strategy of leading players |
28 | Market share of vendors, 2023 |
29 | Company Profiles |
30 | Unmet needs and opportunity for new suppliers |
31 | Conclusion |
32 | Appendix |