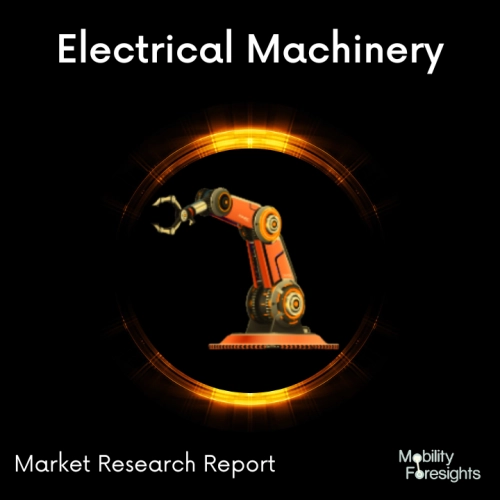
- Get in Touch with Us
Last Updated: Apr 25, 2025 | Study Period: 2024-2030
A polymer diverter valve, a pelletizing unit, a water treatment and drying system, and an electrical control system comprise the underwater pelletizing system.
The polymer diverter valve directs the melt flow downwards when it is activated.Pelletizing is an agglomeration or particle size enlargement procedure that converts material particles into pellets or granules.
Pelletizing is used in a variety of sectors to convert thousands of materials from tough to handle powders and fines to easy to handle pellets.The goal of pelleting is to take a finely split, sometimes dusty, unpleasant, and difficult-to-handle feed material and shape it into larger particles using heat, moisture, and pressure.
The Global Underwater Pelletizing System Market accounted for $XX Billion in 2023 and is anticipated to reach $XX Billion by 2030, registering a CAGR of XX% from 2024 to 2030.
ips increases its underwater pelletizing product line ips Intelligent Pelletizing Solutions GmbH & Co. KG currently offers a newly developed, compact rotary tube for the inline crystallisation of PET pellets as a supplement to its ips-UWG S underwater pelletizing systems and as a "stand-alone" product.
PET is an ideal plastic for the production of packaging films, bottles, fibers, and packaging tapes. However, the substance must be dried and crystallised before it can be treated. The ips-DR / K rotary tube has recently been introduced as a system option for Ips' underwater pelletizing systems, specifically for the inline crystallisation of PET recycled goods.
The ips-DR / K is ideal for continuous production and the efficient crystallisation of amorphous PET granulate and regrind due to its compact, horizontal design and targeted process control.
The constant mobility, which occurs in the absence of external energy, keeps the amorphous PET granulate from clumping and sticking together throughout the crystallisation process.
The ips-DR / K rotary kiln allows for the delicate and energy-efficient crystallisation of PET granulate with crystallisation degrees more than 30%. Because of the simple and durable structure, the conveying parts inside the rotary kiln may be cleaned and maintained quickly and easily.
The amorphous PET pellets enter the rotary kiln immediately from the ips-GT pellet drier, with a pellet temperature above the required crystallisation start temperature. The crystallisation of PET granulates is enabled by the utilisation of their own heat energy. An external energy source, such as infrared heaters, is not required.
Sl no | Topic |
1 | Market Segmentation |
2 | Scope of the report |
3 | Abbreviations |
4 | Research Methodology |
5 | Executive Summary |
6 | Introduction |
7 | Insights from Industry stakeholders |
8 | Cost breakdown of Product by sub-components and average profit margin |
9 | Disruptive innovation in the Industry |
10 | Technology trends in the Industry |
11 | Consumer trends in the industry |
12 | Recent Production Milestones |
13 | Component Manufacturing in US, EU and China |
14 | COVID-19 impact on overall market |
15 | COVID-19 impact on Production of components |
16 | COVID-19 impact on Point of sale |
17 | Market Segmentation, Dynamics and Forecast by Geography, 2024-2030 |
18 | Market Segmentation, Dynamics and Forecast by Product Type, 2024-2030 |
19 | Market Segmentation, Dynamics and Forecast by Application, 2024-2030 |
20 | Market Segmentation, Dynamics and Forecast by End use, 2024-2030 |
21 | Product installation rate by OEM, 2023 |
22 | Incline/Decline in Average B-2-B selling price in past 5 years |
23 | Competition from substitute products |
24 | Gross margin and average profitability of suppliers |
25 | New product development in past 12 months |
26 | M&A in past 12 months |
27 | Growth strategy of leading players |
28 | Market share of vendors, 2023 |
29 | Company Profiles |
30 | Unmet needs and opportunity for new suppliers |
31 | Conclusion |
32 | Appendix |