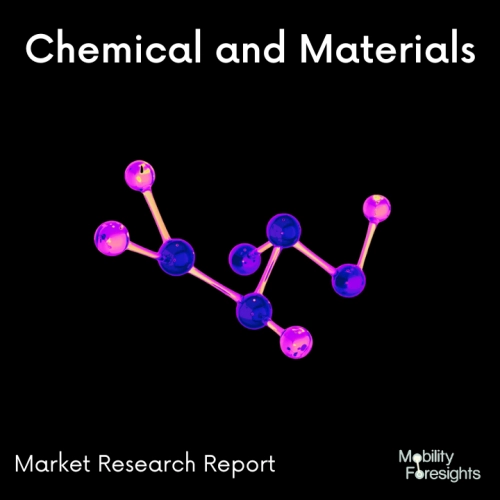
- Get in Touch with Us
Last Updated: Apr 25, 2025 | Study Period: 2024-2030
Vinyl acetate monomer (VAM) is a significant intermediate in the production of a wide variety of resins and polymers for paints and coatings, adhesives, glues and sealants, elastomers, textile finishes, paper coatings, binders, films, and a plethora of other applications in industry and consumer goods.
VAM can be used in a variety of random copolymers and terpolymers, including ethylene-vinyl acetate copolymers, vinyl-acrylic resins, vinyl acetate-acrylic acid copolymers, and vinyl acetate-vinyl chloride copolymers.
It efficiently homo-polymerizes to polyvinyl acetate (PVA), and VAM can be used in PVA homo-polymerization. VAM has made it possible to create products with a wide range of cost and performance profiles thanks to its wide range of polymerization options.
The production of polyvinyl acetate resins as a base for adhesives and coatings and as a feedstock for derivative resins like polyvinyl alcohol (PVOH) is the largest application for VAM. Emulsions and resins made of polyvinyl acetate are inexpensive, simple to use, and suitable for a wide range of applications.
PVA is probably best known for being the base of household white glues that are used to bond paper, fabrics, wood, and plastic.
The Global VAM-Based Emulsion Adhesives market accounted for $XX Billion in 2023 and is anticipated to reach $XX Billion by 2030, registering a CAGR of XX% from 2024 to 2030.
VAM-BASED EMULSION ADHESIVES MARKET DYNAMICS
Asian Paints to set up manufacturing facility for VAE and VAM - The establishment of a manufacturing facility in India for VAE (Vinyl Acetate Ethylene Emulsion) and VAM (Vinyl Acetate Monomer) with an estimated investment of Rs. 2,100 crores over three years.
This is contingent on obtaining the necessary regulatory and other approvals and concluding definitive agreements, such as a technology license agreement for the production of VAE and VAM. The aforementioned manufacturing facility would have an installed capacity of 100,000 tons per year. for 150,000 tons per year and VAM the VAE.
The most important component in the production of environmentally friendly paints is VAE, which is considered to be the future emulsion. VAE can significantly enhance paint performance in customer-facing attributes and provide improved paint properties. The Company's primary raw material is VAE.
For the production of VAE, VAM is a crucial inputâjustification for in-house production of VAM and VAE. Rather than relying on imports, manufacturing VAM and VAE in India would reduce costs significantly over time and be used for the company's internal consumption.
Rather than relying on imports, manufacturing VAM and VAE in India would reduce costs significantly over time and be used for the company's internal consumption. The company's most important backward integration project would be this one.
The licensing of technology with Kellogg Brown & Root LLC (KBR), USA, would serve as the foundation for the establishment of a VAM manufacturing facility. KBR is a US-based company with operations in more than 80 countries.
Asian Paints has a significant competitive advantage in the coatings industry thanks to the environmentally friendly Next Generation Vinyl Acetate Ethylene Emulsion, which is based on a one-of-a-kind Vinyl Acetate Monomer technology.
Asian paints have made a number of investments in China, the most recent of which is the expansion of emulsions. With six production units, including acetic acid and vinyl acetate monomer (VAM), several units from Asian paints's Ticona business, and the existing emulsions plant, Nanjing is currently the largest integrated site in the Asian paints global manufacturing network.
Since their first manufacturing activities in China just over three years ago, Asian Paints Emulsion Polymers has grown into a thriving organization in China and is presently expanding across Asia, into India and surrounding countries, Southeast Asia, and Australia.
Celvolit 149 LV, a low-odour vinyl acetate/ethylene (VAE) emulsion manufactured by Celanese Emulsion Polymers, has been launched to meet China's new national tobacco adhesives standard.
Celvolit 149LV combines Celanese's reputation for high performance in the tobacco industry with the new standard for residual monomer level.The new VAE emulsion has been tested in adhesives designed for high-speed tipping applications and exhibits excellent rheology.
The new emulsion can also be used in the tobacco industry paper packaging adhesives, where VAE emulsions have long been the preferred choice due to their extremely low odour.A low-odour, low-VOC adhesive is the result of the new emulsion's advanced technical control and formulation. In Asia, Celvolit 149LV is available.
North America
The North American market, particularly the USA, will be one of the prime markets for (VAM-Based Emulsion Adhesives) due to the nature of industrial automation in the region, high consumer spending compared to other regions, and the growth of various industries, mainly AI, along with constant technological advancements. The GDP of the USA is one of the largest in the world, and it is home to various industries such as Pharmaceuticals, Aerospace, and Technology. The average consumer spending in the region was $72K in 2023, and this is set to increase over the forecast period. Industries are focused on industrial automation and increasing efficiency in the region. This will be facilitated by the growth in IoT and AI across the board. Due to tensions in geopolitics, much manufacturing is set to shift towards the USA and Mexico, away from China. This shift will include industries such as semiconductors and automotive.
Europe
The European market, particularly Western Europe, is another prime market for (VAM-Based Emulsion Adhesives) due to the strong economic conditions in the region, bolstered by robust systems that support sustained growth. This includes research and development of new technologies, constant innovation, and developments across various industries that promote regional growth. Investments are being made to develop and improve existing infrastructure, enabling various industries to thrive. In Western Europe, the margins for (VAM-Based Emulsion Adhesives) are higher than in other parts of the world due to regional supply and demand dynamics. Average consumer spending in the region was lower than in the USA in 2023, but it is expected to increase over the forecast period.
Eastern Europe is anticipated to experience a higher growth rate compared to Western Europe, as significant shifts in manufacturing and development are taking place in countries like Poland and Hungary. However, the Russia-Ukraine war is currently disrupting growth in this region, with the lack of an immediate resolution negatively impacting growth and creating instability in neighboring areas. Despite these challenges, technological hubs are emerging in Eastern Europe, driven by lower labor costs and a strong supply of technological capabilities compared to Western Europe.
There is a significant boom in manufacturing within Europe, especially in the semiconductor industry, which is expected to influence other industries. Major improvements in the development of sectors such as renewable energy, industrial automation, automotive manufacturing, battery manufacturing and recycling, and AI are poised to promote the growth of (VAM-Based Emulsion Adhesives) in the region.
Asia
Asia will continue to be the global manufacturing hub for (VAM-Based Emulsion Adhesives) over the forecast period with China dominating the manufacturing. However, there will be a shift in manufacturing towards other Asian countries such as India and Vietnam. The technological developments will come from China, Japan, South Korea, and India for the region. There is a trend to improve the efficiency as well as the quality of goods and services to keep up with the standards that are present internationally as well as win the fight in terms of pricing in this region. The demand in this region will also be driven by infrastructural developments that will take place over the forecast period to improve the output for various industries in different countries.
There will be higher growth in the Middle East as investments fall into place to improve their standing in various industries away from petroleum. Plans such as Saudi Arabia Vision 2030, Qatar Vision 2030, and Abu Dhabi 2030 will cause developments across multiple industries in the region. There is a focus on improving the manufacturing sector as well as the knowledge-based services to cater to the needs of the region and the rest of the world. Due to the shifting nature of fossil fuels, the region will be ready with multiple other revenue sources by the time comes, though fossil fuels are not going away any time soon.
Africa
Africa is expected to see the largest growth in (VAM-Based Emulsion Adhesives Market) over the forecast period, as the region prepares to advance across multiple fronts. This growth aligns with the surge of investments targeting key sectors such as agriculture, mining, financial services, manufacturing, logistics, automotive, and healthcare. These investments are poised to stimulate overall regional growth, creating ripple effects across other industries as consumer spending increases, access to products improves, and product offerings expand. This development is supported by both established companies and startups in the region, with assistance from various charitable organizations. Additionally, the presence of a young workforce will address various existing regional challenges. There has been an improvement in political stability, which has attracted and will continue to attract more foreign investments. Initiatives like the African Continental Free Trade Area (AfCFTA) are set to facilitate the easier movement of goods and services within the region, further enhancing the economic landscape.
RoW
Latin America and the Oceania region will showcase growth over the forecast period in (VAM-Based Emulsion Adhesives Market). In Latin America, the focus in the forecast period will be to improve their manufacturing capabilities which is supported by foreign investments in the region. This will be across industries mainly automotive and medical devices. There will also be an increase in mining activities over the forecast period in this region. The area is ripe for industrial automation to enable improvements in manufacturing across different industries and efficiency improvements. This will lead to growth of other industries in the region.
Margin Comparison (Highest to lowest) | Region | Remarks |
1 | Europe | The supply chain demands and the purchasing power in the region enable suppliers to extradite a larger margin from this region than other regions. This is for both locally manufactured as well as imported goods and services in the region. |
2 | North America | Due to the high spending power in this region, the margins are higher compared to the rest of the world, but they are lower than Europe as there is higher competition in this region. All the suppliers of goods and services target USA as a main market thereby decreasing their margins compared to Europe |
3 | Asia | Lower purchasing power, coupled with higher accessibility of services in this regions doesnât enable suppliers to charge a high margin making it lower than Europe and North America. The quality of goods and services are also affected due to this aspect in the region |
4 | Africa and ROW | The margins are the lowest in this region, except for Australia and New Zealand as the countries in this region donât have much spending power and a large portion of the products and services from this area is exported to other parts of the world |
Sl no | Topic |
1 | Market Segmentation |
2 | Scope of the report |
3 | Abbreviations |
4 | Research Methodology |
5 | Executive Summary |
6 | Introduction |
7 | Insights from Industry stakeholders |
8 | Cost breakdown of Product by sub-components and average profit margin |
9 | Disruptive innovation in the Industry |
10 | Technology trends in the Industry |
11 | Consumer trends in the industry |
12 | Recent Production Milestones |
13 | Component Manufacturing in US, EU and China |
14 | COVID-19 impact on overall market |
15 | COVID-19 impact on Production of components |
16 | COVID-19 impact on Point of sale |
17 | Market Segmentation, Dynamics and Forecast by Geography, 2024-2030 |
18 | Market Segmentation, Dynamics and Forecast by Product Type, 2024-2030 |
19 | Market Segmentation, Dynamics and Forecast by Application, 2024-2030 |
20 | Market Segmentation, Dynamics and Forecast by End use, 2024-2030 |
21 | Product installation rate by OEM, 2023 |
22 | Incline/Decline in Average B-2-B selling price in past 5 years |
23 | Competition from substitute products |
24 | Gross margin and average profitability of suppliers |
25 | New product development in past 12 months |
26 | M&A in past 12 months |
27 | Growth strategy of leading players |
28 | Market share of vendors, 2023 |
29 | Company Profiles |
30 | Unmet needs and opportunity for new suppliers |
31 | Conclusion |
32 | Appendix |