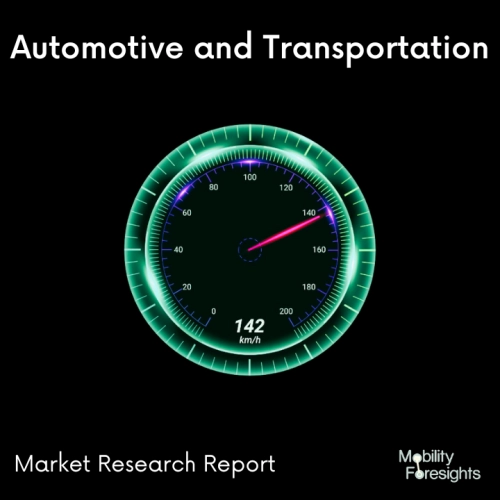
- Get in Touch with Us
Last Updated: Apr 25, 2025 | Study Period: 2023-2030
One form of the turbocharger is a variable geometry turbocharger (VGT), often referred to as a variable-nozzle turbine (VNT), which is typically built to allow the turbocharger's effective aspect ratio to be changed as conditions change.
This is accomplished by using movable vanes that control the flow of gases toward the turbine and are situated inside the turbine housing between the inlet and turbine. The advantage of the VGT is that the ideal aspect ratio at low engine speeds and high engine speeds are quite different.
At low speeds, a turbo that has an aspect ratio that is too large will not provide boost; at high speeds, a turbo that has an aspect ratio that is too small will choke the engine, causing high exhaust manifold pressures, high pumping losses, and eventually poor power output.
The aspect ratio of the turbo can be kept at its ideal level by adjusting the geometry of the turbine housing as the engine speeds up.
As a result, VGTs have a low boost threshold, less lag, and good efficiency at higher engine speeds. The turbine's vanes rotate simultaneously with respect to the hub in light-duty engines (passenger cars, racing cars, and light commercial vehicles) to change the pitch and cross-sectional area.
The vanes do not spin in heavy-duty engines; instead, their effective breadth is altered. This is often accomplished by rotating the turbine on its axis while partially retracting the housing's vanes.
As an alternative, a wall within the home may move back and forth. A variable-aspect-ratio system with fewer moving components results from the variation in the space between the edges of the vanes.
A membrane vacuum actuator, electric servo, 3-phase electric actuation, hydraulic actuator, or pneumatic actuator using air brake pressure are all options for controlling VGTs.
Because they are less susceptible to failure due to lower exhaust temperatures, VGTs are often far more prevalent on diesel engines.
Early gasoline-engine VGTs needed a lot of pre-charge cooling to extend the turbocharger life to acceptable levels, but as technology advanced, they became more resistant to high-temperature gasoline exhaust and started to show up in more and more gasoline-powered cars.
The Global Variable Geometry Turbochargers market accounted for $XX Billion in 2022 and is anticipated to reach $XX Billion by 2030, registering a CAGR of XX% from 2023 to 2030.
To enable engine manufacturers to fulfill upcoming pollution rules and provide best-in-class fuel efficiency, Cummins introduced the 7th generation 400 series Variable Geometry Turbocharger (VGT).
As we develop new technologies while advancing our existing ones, innovation never stops at Cummins. CTT is currently getting ready to release the 8th generation HE400VGT with this idea in mind.
It is designed exclusively for the 10-15L heavy-duty vehicle market and has best-in-class performance, dependability, and longevity.
Sl no | Topic |
1 | Market Segmentation |
2 | Scope of the report |
3 | Abbreviations |
4 | Research Methodology |
5 | Executive Summary |
6 | Introduction |
7 | Insights from Industry stakeholders |
8 | Cost breakdown of Product by sub-components and average profit margin |
9 | Disruptive innovation in the Industry |
10 | Technology trends in the Industry |
11 | Consumer trends in the industry |
12 | Recent Production Milestones |
13 | Component Manufacturing in US, EU and China |
14 | COVID-19 impact on overall market |
15 | COVID-19 impact on Production of components |
16 | COVID-19 impact on Point of sale |
17 | Market Segmentation, Dynamics and Forecast by Geography, 2023-2030 |
18 | Market Segmentation, Dynamics and Forecast by Product Type, 2023-2030 |
19 | Market Segmentation, Dynamics and Forecast by Application, 2023-2030 |
20 | Market Segmentation, Dynamics and Forecast by End use, 2023-2030 |
21 | Product installation rate by OEM, 2023 |
22 | Incline/Decline in Average B-2-B selling price in past 5 years |
23 | Competition from substitute products |
24 | Gross margin and average profitability of suppliers |
25 | New product development in past 12 months |
26 | M&A in past 12 months |
27 | Growth strategy of leading players |
28 | Market share of vendors, 2023 |
29 | Company Profiles |
30 | Unmet needs and opportunity for new suppliers |
31 | Conclusion |
32 | Appendix |