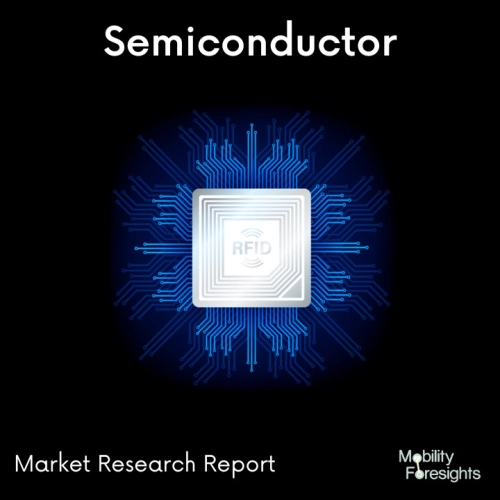
- Get in Touch with Us
Last Updated: Apr 25, 2025 | Study Period: 2024-2030
A vacuum chamber, customised gas delivery system, radio frequency (RF) waveform generator to power the plasma, heated chuck to seat the wafer and exhaust system comprise the dry etching hardware design.
Chemical etching wafers is a technique that removes material from the surface of a wafer in layers during the fabrication of Silicon Wafers (Si), Gallium Arsenide (GaAs), and Gallium Nitride wafers.
Wet chemical etching methods use dissolving processes to remove components from the top layer of an integrated device structure.Dry etching is often an anisotropic method in which the momentum of accelerating ion species combined with a masking process is employed to physically remove and etch the target materials.
S.NO | Overview of Development | Details of Development |
1. | Trymax Launches a Brand-New UV Curing and Charge Erase Product Line | A charge-erasing and ultraviolet (UV) curing product line have been added to Trymax Semiconductor Equipment BV's (Trymax) portfolio. Trymax is a leader in the world of plasma solutions for semiconductor manufacturers. The NEO 2000UV system is a cutting-edge dual chamber solution that can accommodate wafer diameters up to 200mm. |
Applications for UV curing and charge erase equipment include photo-stabilizing the resist prior to implantation or etch, for tiny CDs, and to erase charge accumulated during the manufacture of integrated circuits (ICs). Trymax decided to create this new product in response to market demand.
Finding UV curing/charge erase equipment to increase their manufacturing capacity or even just to maintain their current tooling was proving to be problematic for a number of IC fabs. Customers were forced to rely primarily on infrequently available refurbished components and equipment.
New memory and logic devices are now possible wih the launch of next-generation selective etch tools by a number of etch providers. Next-generation selective etch systems, also known as highly-selective etch systems, were initially shipped by Applied Materials.
In advance of cutting-edge products like 3D DRAM and gate-all-around transistors, companies like Lam Research, TEL, and others are shipping equipment with highly-selective etch capabilities. During the manufacturing of integrated circuits (ICs), a specialized etch tool uses highly-selective etch to remove or etche away materials from small chip architectures.
Additionally, the materials can be removed in any direction (isotropically) with these highly selective etch tools without causing harm to the device's other components. In rare circumstances, materials can be removed in one direction (anistropically) by extremely selective etch instruments.
There are certain existing etch tools that can do selective etches to varying degrees, but their capabilities are constrained here and they cannot build the new device architectures at advanced nodes.
The Global Wafer Dry Etching System Market accounted for $XX Billion in 2023 and is anticipated to reach $XX Billion by 2030, registering a CAGR of XX% from 2024 to 2030.
The NA-1500 dry etching equipment from ULVAC is designed for 600mm advanced packaging substrates. ULVAC debuted the NA-1500 dry etching equipment for 600mm advanced packaging substrates, which allows for consistent Descum and Ti etching procedures.
Higher data transfer rates necessitate high-density packaging, whereas modern mobile and wireless devices necessitate thinner and higher-pin-count IC packages. Fan-Out Wafer Level Packaging (FO-WLP) is common, whereas Panel Level Packaging expands substrate size from 300mm to 600mm.
While there are several dry etching systems for 200mm/300mm wafers on the market today, there was no dry etching system for 600mm substrate that provided a uniform Descum process and Ti etching procedure. ULVAC created the technology to meet this need while also supporting mass-produced packaging processes.
Because the plasma source is also suitable for fluorine gases, seed layer Ti etching, which needs a wet procedure, can be carried out without the need for side etching.
The NA-1500 also supports SiO2 and SiN etching. The NA-1500 dry etching system also offers reliable transfer and operations that are free of anomalous discharge, guaranteeing that warpage from the expanded substrate is never a concern.
S.NO | Overview of Partnership | Details of Partnership |
1. | Amtech Adds Etching System to Solar Product Portfolio | Amtech Systems, Inc., a global provider of production and automation systems and associated supplies for the production of silicon wafers, semiconductors, and solar cells, announced that it has signed a license agreement with PST Co., LTD., based in Youngin-City, Korea, to market PST's exclusive PSG dry etch system and to create and produce additional models for use with Amtech's current solar products. |
Phosphorus silicate glass (PSG), which naturally forms during the diffusion process, is removed during this process stage in the production of solar cells.
Amtech will use the license it has been granted for this special PSG technology, which will be produced by PST, to increase its market share in the expanding solar industry. During the dry etching process, PST employs a proprietary technology that enables high productivity and lower total cost of ownership.
Sl no | Topic |
1 | Market Segmentation |
2 | Scope of the report |
3 | Abbreviations |
4 | Research Methodology |
5 | Executive Summary |
6 | Introdauction |
7 | Insights from Industry stakeholders |
8 | Cost breakdown of Product by sub-components and average profit margin |
9 | Disruptive innovation in theIndustry |
10 | Technology trends in the Industry |
11 | Consumer trends in the industry |
12 | Recent Production Milestones |
13 | Component Manufacturing in US, EU and China |
14 | COVID-19 impact on overall market |
15 | COVID-19 impact on Production of components |
16 | COVID-19 impact on Point of sale |
17 | Market Segmentation, Dynamics and Forecast by Geography, 2024-2030 |
18 | Market Segmentation, Dynamics and Forecast by Product Type, 2024-2030 |
19 | Market Segmentation, Dynamics and Forecast by Application, 2024-2030 |
20 | Market Segmentation, Dynamics and Forecast by End use, 2024-2030 |
21 | Product installation rate by OEM, 2023 |
22 | Incline/Decline in Average B-2-B selling price in past 5 years |
23 | Competition from substitute products |
24 | Gross margin and average profitability of suppliers |
25 | New product development in past 12 months |
26 | M&A in past 12 months |
27 | Growth strategy of leading players |
28 | Market share of vendors, 2023 |
29 | Company Profiles |
30 | Unmet needs and opportunity for new suppliers |
31 | Conclusion |
32 | Appendix |