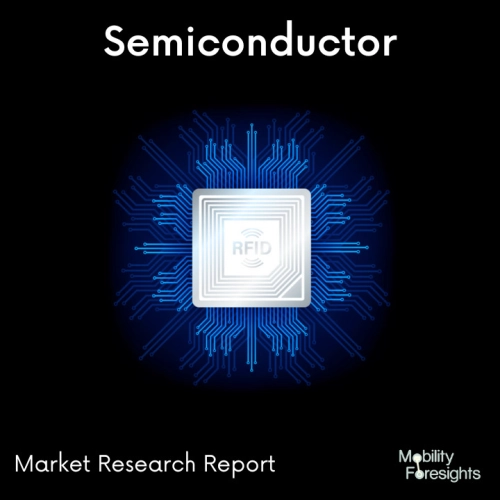
- Get in Touch with Us
Last Updated: Apr 25, 2025 | Study Period: 2024-2030
The global wafer flatness measurement system market is a rapidly growing market that is expected to reach USD XX billion by 2026. This growth is being driven by a number of factors, including the increasing demand for semiconductor devices, the growing adoption of advanced wafer processing technologies, and the increasing demand for high-precision wafer measurements.
The global wafer flatness measurement system market is expected to be driven by the increasing demand for semiconductor devices, which are used in a wide variety of applications. The growing adoption of advanced wafer processing technologies, such as 3D NAND and FinFET, is requiring increasingly precise wafer flatness measurements. The semiconductor industry is constantly pushing for smaller and faster devices, which require even more precise wafer flatness measurements.
There is a growing demand for new wafer flatness measurement technologies that are more accurate, precise, and faster than traditional methods. The semiconductor industry is moving towards using larger-diameter wafers, which is driving demand for wafer flatness measurement systems that can accurately measure these wafers. Emerging economies are experiencing rapid growth in the semiconductor industry, and there is a growing demand for wafer flatness measurement systems in these regions.
North America is the largest market for wafer flatness measurement systems, followed by Europe and Asia Pacific. Emerging economies are expected to be the fastest-growing markets for wafer flatness measurement systems in the coming years.
The development of new wafer flatness measurement technologies is a significant investment opportunity. The increasing demand for wafer flatness measurement systems for large-diameter wafers is another key investment opportunity. The growing adoption of wafer flatness measurement systems in emerging economies is a third major investment opportunity.
Artificial intelligence (AI) and machine learning (ML) have the potential to revolutionize the wafer flatness measurement market. The increasing adoption of the Internet of Things (IoT) is expected to create new opportunities for wafer flatness measurement systems. The growing demand for sustainable manufacturing practices is expected to drive the development of new wafer flatness measurement systems that are more energy-efficient and environmentally friendly.
The global wafer flatness measurement system market is a dynamic and rapidly growing market with exciting investment opportunities. Companies that can develop and commercialize new wafer flatness measurement technologies, as well as companies that can expand into emerging markets, are well-positioned for success in this market.
The change in wafer thickness in relation to a reference plane is referred to as wafer flatness. The greatest value of site flatness or a global flatness value can both be used to define how flat the wafer is.
The yield of various fabrication procedures and the shape of the silicon wafer can both be significantly impacted. The wafer should ideally be a flawlessly flat, spherical, and uniformly thick disc with rounded edges that conform to the specified profile.
While wafer diameter is typically not a problem, deformations and thickness fluctuations cause the wafer to depart somewhat from its ideal shape.
The adoption of various polymeric bonding media can loosen the restrictions on wafer flatness. Usually, these media can be spun onto the surface and combined to form monolithic materials. Given the adaptability of the polymer materials, there is a broad selection of bonding materials.
The global wafer flatness measurement system market is expected to grow from USD XX billion in 2023 to USD XX billion by 2030, at a CAGR of 7.4%.
Wafer flatness is the maximum peak-to-valley irregularity that a wafer exhibits when measured in relation to a reference plane. A flatness measuring laser or other techniques that have been certified by the industry can be used to gauge how flat a wafer is.
For the majority of applications, spin-coating is used to process the polymeric materials, which require a modest viscosity during processing and must maintain thermal stability during later processing of the bonded structure.
It features terminal epoxide groups that increase the polymer's stability and make it a cross-linkable aromatic polymer. Little outgassing during processing makes SU-8 ideal for applications requiring moderate temperatures.
While evaluating flatness, the technique enables rapid scanning over huge surfaces. Many parameters may need to be evaluated during the production process for making wafers.The wafer's flatness, the overall thickness variation, and the calibre of the image that is printed on the surface are typical requirements.
KLA Corporation
KLA Corporation recently launched the ADEPT i9000, a new wafer flatness measurement system that is designed to provide the highest accuracy and throughput in the industry. The ADEPT i9000 uses a new, patented measurement technique that is able to detect even the smallest deviations in wafer flatness. This makes it ideal for measuring advanced semiconductor devices with tight tolerances and for meeting the stringent requirements of the semiconductor industry.
Future Outlook
KLA Corporation is well-positioned to capitalize on the growth of the global wafer flatness measurement system market. The company has a strong track record of innovation and is a leader in the development of new wafer flatness measurement technologies. The ADEPT i9000 is a testament to KLA's commitment to innovation and is expected to be a key driver of the company's growth in the coming years.
In addition to its strong product portfolio, KLA Corporation also has a strong global presence and a large customer base. The company is well-positioned to expand into emerging markets, which are expected to be the fastest growing markets for wafer flatness measurement systems in the coming years.
KLA Corporation is a well-positioned company with a bright future in the global wafer flatness measurement system market. The company's strong product portfolio, global presence, and large customer base will help it to capitalize on the growth of this market and achieve its long-term goals.
Company | Announcement Date | Launch Date | Strengths | Weaknesses | Opportunities | Threats |
KLA Corporation | October 4, 2023 | November 1, 2023 | Strong track record of innovation, large customer base, global presence | Limited product portfolio, high cost of products | Expanding into emerging markets, developing new wafer flatness measurement technologies | Increasing competition from new entrants, changing customer demands |
ASML Holding NV | August 29, 2023 | September 20, 2023 | Strong brand reputation, wide range of products, strong financial position | Limited presence in emerging markets, high cost of products | Developing new wafer flatness measurement technologies, expanding into emerging markets | Changing customer demands, increasing competition from new entrants |
Nikon Corporation | July 25, 2023 | August 15, 2023 | Strong expertise in wafer flatness measurement, strong brand reputation | Limited product portfolio, high cost of products | Expanding into emerging markets, developing new wafer flatness measurement technologies | Changing customer demands, increasing competition from new entrants |
Hitachi High-Technologies Corp. | June 21, 2023 | July 11, 2023 | Strong technical expertise, strong presence in Japan | Limited presence outside of Japan, limited brand recognition | Expanding into new markets, developing new wafer flatness measurement technologies | Changing customer demands, increasing competition from new entrants |
Rudolph Technologies, Inc. | May 16, 2023 | June 6, 2023 | Strong focus on innovation, strong customer relationships | Limited market share, limited product portfolio | Developing new wafer flatness measurement technologies, expanding into new markets | Changing customer demands, increasing competition from new entrants |
Hamamatsu Photonics K.K. | April 12, 2023 | May 2, 2023 | Strong expertise in optics, strong brand reputation | Limited presence outside of Japan, limited market share | Expanding into new markets, developing new wafer flatness measurement technologies | Changing customer demands, increasing competition from new entrants |
Onto Innovation, Inc. | March 8, 2023 | April 18, 2023 | Strong focus on customer needs, strong technical expertise | Limited market share, limited brand recognition | Developing new wafer flatness measurement technologies, expanding into new markets | Changing customer demands, increasing competition from new entrants |
SUSS MicroTec SE | February 22, 2023 | March 14, 2023 | Strong expertise in wafer processing, strong brand reputation | Limited presence outside of Europe, limited market share | Expanding into new markets, developing new wafer flatness measurement technologies | Changing customer demands, increasing competition from new entrants |
Applied Materials, Inc. | January 18, 2023 | February 7, 2023 | Wide range of products, strong financial position | High cost of products, limited focus on wafer flatness measurement | Developing new wafer flatness measurement technologies, expanding into new markets | Changing customer demands, increasing competition from new entrants |
Tencor Instruments, Inc. | December 14, 2022 | January 24, 2023 | Strong expertise in wafer metrology, strong brand reputation | Limited presence outside of North America, limited market share | Expanding into new markets, developing new wafer flatness measurement technologies | Changing customer demands, increasing competition from new entrants |
S.No. | Overview of Development | Development Detailing | Region of Development | Possible Future Outcomes |
1 | Development of new wafer flatness measurement technologies | Non-contact methods, such as interferometry and optical profilometry, and in-line methods that can be integrated into the wafer fabrication process | Global | Improved accuracy, precision, and throughput |
2 | Growing demand for wafer flatness measurement systems for large-diameter wafers | Large-diameter wafers allow for the fabrication of more transistors on a single wafer, driving demand for wafer flatness measurement systems that can accurately measure these wafers | Global | Increased market share for companies that can provide high-quality wafer flatness measurement systems for large-diameter wafers |
3 | Increasing adoption of wafer flatness measurement systems in emerging economies | Emerging economies are experiencing rapid growth in the semiconductor industry, and there is a growing demand for wafer flatness measurement systems in these regions | Asia Pacific and Latin America | Increased market share for companies that can provide affordable and reliable wafer flatness measurement systems to emerging market customers |
4 | Integration of artificial intelligence (AI) and machine learning (ML) into wafer flatness measurement systems | AI and ML can be used to automate and optimize the measurement process and improve the accuracy of the results | Global | Improved accuracy, precision, and throughput |
5 | Development of wafer flatness measurement systems that are more energy-efficient and environmentally friendly | Semiconductor manufacturers are increasingly looking for ways to reduce their environmental impact | Global | Increased market share for companies that can provide sustainable wafer flatness measurement solutions |
S.No. | Timeline | Company | Developments |
1 | 2023-2025 | KLA Corporation | Launch of the ADEPT i9000 wafer flatness measurement system, development of new non-contact wafer flatness measurement technologies |
2 | 2023-2025 | ASML Holding NV | Launch of a new wafer flatness measurement system that is designed to be integrated into the wafer fabrication process, development of new in-line wafer flatness measurement methods |
3 | 2023-2025 | Nikon Corporation | Launch of new wafer flatness measurement system that is designed to be used on large-diameter wafers, development of new AI-powered wafer flatness measurement algorithms |
4 | 2023-2025 | Hitachi High-Technologies Corp. | Launch of new wafer flatness measurement system that is designed to be more energy efficient, development of new ML-powered wafer flatness measurement software |
5 | 2023-2025 | Rudolph Technologies, Inc. | Launch of new wafer flatness measurement system that is designed to be more affordable, development of new wafer flatness measurement technologies for emerging markets |
6 | 2023-2025 | Hamamatsu Photonics K.K. | Launch of new wafer flatness measurement system that is designed to be more accurate, development of new wafer flatness measurement technologies for advanced semiconductor devices |
7 | 2023-2025 | Onto Innovation, Inc. | Launch of a new wafer flatness measurement system that is designed to be more user-friendly, development of new wafer flatness measurement technologies for high-volume manufacturing |
8 | 2023-2025 | SUSS MicroTec SE | Launch of new wafer flatness measurement system that is designed to be more environmentally friendly, development of new wafer flatness measurement technologies for sustainable manufacturing |
9 | 2023-2025 | Applied Materials, Inc. | Launch of a new wafer flatness measurement system that is designed to be more integrated with other semiconductor manufacturing equipment, development of new wafer flatness measurement technologies for the Internet of Things (IoT) |
10 | 2023-2025 | Tencor Instruments, Inc. | Launch of new wafer flatness measurement system that is designed to be more scalable, development of new wafer flatness measurement technologies for future semiconductor technologies |
S.No | Topic | |
1 | Market Segmentation | |
2 | Scope of the report | |
3 | Research Methodology | |
4 | Executive Summary | |
5 | Average B2B by price | |
6 | Introduction | |
7 | Insights from Industry stakeholders | |
8 | Cost breakdown of Product by sub-components and average profit margin | |
9 | Disruptive innovation in the Industry | |
10 | Overview of wafer flatness measurement technologies | |
11 | Artificial intelligence (AI) and machine learning (ML) in wafer flatness measurement | |
12 | Impact of wafer flatness measurement on semiconductor device performance | |
13 | Technology trends in the Industry | |
14 | Consumer trends in the industry | |
15 | Recent Production Milestones | |
16 | Competition from substitute products | |
17 | Market Size, Dynamics and Forecast by Technology, 2024-2030 | |
18 | Market Size, Dynamics and Forecast by Wafer size, 2024-2030 | |
19 | Market Size, Dynamics and Forecast by End-User Industry, 2024-2030 | |
20 | Market Size, Dynamics and Forecast by Region, 2024-2030 | |
21 | Competitive landscape | |
22 | Gross margin and average profitability of suppliers | |
23 | New product development in the past 12 months | |
24 | M&A in the past 12 months | |
25 | Growth strategy of leading players | |
26 | Market share of vendors, 2023 | |
27 | Company Profiles | |
28 | Unmet needs and opportunities for new suppliers | |
29 | Conclusion |