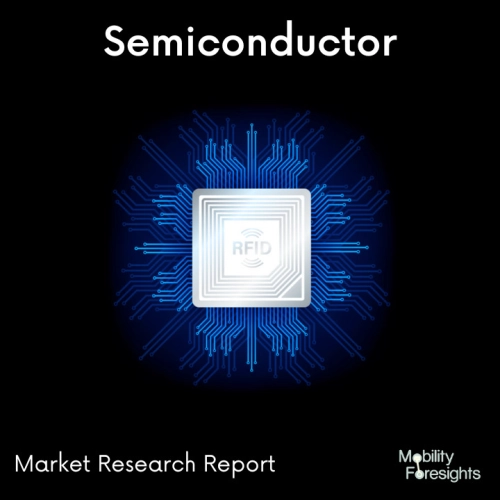
- Get in Touch with Us
Last Updated: Apr 25, 2025 | Study Period: 2023-2030
Spin coating is a centrifugal force-based technique for spreading uniform thin films on flat substrates. A spin coater, often known as a spinner, is the machine used for spin coating. A material solution is poured onto the centre of a wafer, which is subsequently rotated at high speed.
Spin coating is frequently utilised in the microfabrication of functional oxide layers on glass or single crystal substrates using sol-gel precursors, where it can be used to make homogeneous thin films with nanoscale thicknesses. It is often used in photolithography to deposit layers of photoresist around 1 micrometre thick.
The Global Wafer Spin Coater Market accounted for $XX Billion in 2022 and is anticipated to reach $XX Billion by 2030, registering a CAGR of XX% from 2023 to 2030.
Check function for wafer spin coating system with photoresist pumping unit A wafer spin coating system consists of a spin coating unit, a pumping unit, and a sensor unit for coating a layer of photoresist on a wafer. The operation of a spinning device with the wafer mounted on it is controlled by a first controller in the spin coating unit.
A photoresist pumping operation order is also output by the first controller. The pumping unit's second controller receives the pumping operation order and outputs a pumping operation commencing signal as well as a valve operation signal that opens and closes a valve to control a gas feeding operation The wafer is exposed to light and developed after a thin film of photoresist is put on it, often by spin coating.
To generate a desired photoresist pattern, either the exposed portion (in the case of positive resist) or the unexposed portion (in the case of negative resist) of the photoresist is removed. Following that, photolithography or ion implantation is performed using the mask pattern created in the preceding step.
The thickness of the thin photoresist layer placed on the wafer by the spin coating process is determined by factors such as the photoresist's viscosity coefficient and polymeric content, as well as the spin coater's spinning speed and acceleration.
When the spinning operation is finished, 80%-90% of the solvent in the photoresist is evaporated, leaving the thin film deposited on the wafer practically dry. The wafer is subjected to additional processing procedures after the thin coating has completely dried..
Sl no | Topic |
1 | Market Segmentation |
2 | Scope of the report |
3 | Abbreviations |
4 | Research Methodology |
5 | Executive Summary |
6 | Introdauction |
7 | Insights from Industry stakeholders |
8 | Cost breakdown of Product by sub-components and average profit margin |
9 | Disruptive innovation in theIndustry |
10 | Technology trends in the Industry |
11 | Consumer trends in the industry |
12 | Recent Production Milestones |
13 | Component Manufacturing in US, EU and China |
14 | COVID-19 impact on overall market |
15 | COVID-19 impact on Production of components |
16 | COVID-19 impact on Point of sale |
17 | Market Segmentation, Dynamics and Forecast by Geography, 2023-2030 |
18 | Market Segmentation, Dynamics and Forecast by Product Type, 2023-2030 |
19 | Market Segmentation, Dynamics and Forecast by Application, 2023-2030 |
20 | Market Segmentation, Dynamics and Forecast by End use, 2023-2030 |
21 | Product installation rate by OEM, 2023 |
22 | Incline/Decline in Average B-2-B selling price in past 5 years |
23 | Competition from substitute products |
24 | Gross margin and average profitability of suppliers |
25 | New product development in past 12 months |
26 | M&A in past 12 months |
27 | Growth strategy of leading players |
28 | Market share of vendors, 2023 |
29 | Company Profiles |
30 | Unmet needs and opportunity for new suppliers |
31 | Conclusion |
32 | Appendix |