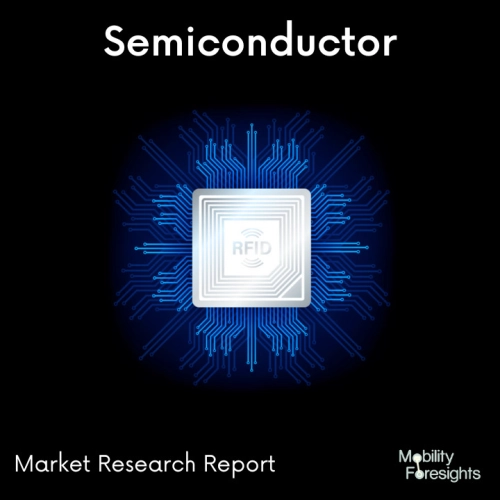
- Get in Touch with Us
Last Updated: Apr 25, 2025 | Study Period: 2024-2030
A wafer sputtering machine is a particular kind of tool used in the semiconductor industry to sputter thin layers onto a substrate, typically a silicon wafer. A target material (often a metal) is bombarded with high-energy ions during sputtering, which causes atoms to be expelled from the target material and deposited onto the substrate.
A wafer sputtering machine typically includes a substrate holder, a vacuum chamber, a target material, and a power source to produce the ion beam. The substrate holder keeps the wafer in position while the thin film is being deposited, and the target material is often constructed of the same material.
To produce thin layers of different materials on wafers for use in integrated circuits, microprocessors, and other electronic devices, the semiconductor industry uses the sputtering technique. Other high-tech uses that call for thin films include the manufacture of solar cells, optical coatings, and other products.
The Global Wafer Sputtering Machine Market accounted for $XX Billion in 2023 and is anticipated to reach $XX Billion by 2030, registering a CAGR of XX% from 2024 to 2030.
The scia Magna 200 is used for precise metal and/or dielectric layer deposition on wafer coatings. The system can be set up to meet the needs of the user thanks to its adjustable sputter modes and combinations. The technology is also appropriate for mass production in a cluster structure with software-controlled automatic production as well as small-scale R&D applications.
Features And Properties includes RF bias for stress reduction and compliance With a rotatable substrate holder, there is greater homogeneity. With helium cooling contact and an electrostatic chuck, the substrate is at a low temperature. Reactive sputtering at high deposition rates in unipolar and bipolar mode. Film characteristics can change due to variable energy substrate bombardment. Using magnetrons in a confocal configuration during co-sputtering.
Sl no | Topic |
1 | Market Segmentation |
2 | Scope of the report |
3 | Abbreviations |
4 | Research Methodology |
5 | Executive Summary |
6 | Introduction |
7 | Insights from Industry stakeholders |
8 | Cost breakdown of Product by sub-components and average profit margin |
9 | Disruptive innovation in the Industry |
10 | Technology trends in the Industry |
11 | Consumer trends in the industry |
12 | Recent Production Milestones |
13 | Component Manufacturing in US, EU and China |
14 | COVID-19 impact on overall market |
15 | COVID-19 impact on Production of components |
16 | COVID-19 impact on Point of sale |
17 | Market Segmentation, Dynamics and Forecast by Geography, 2024-2030 |
18 | Market Segmentation, Dynamics and Forecast by Product Type, 2024-2030 |
19 | Market Segmentation, Dynamics and Forecast by Application, 2024-2030 |
20 | Market Segmentation, Dynamics and Forecast by End use, 2024-2030 |
21 | Product installation rate by OEM, 2023 |
22 | Incline/Decline in Average B-2-B selling price in past 5 years |
23 | Competition from substitute products |
24 | Gross margin and average profitability of suppliers |
25 | New product development in past 12 months |
26 | M&A in past 12 months |
27 | Growth strategy of leading players |
28 | Market share of vendors, 2023 |
29 | Company Profiles |
30 | Unmet needs and opportunity for new suppliers |
31 | Conclusion |
32 | Appendix |