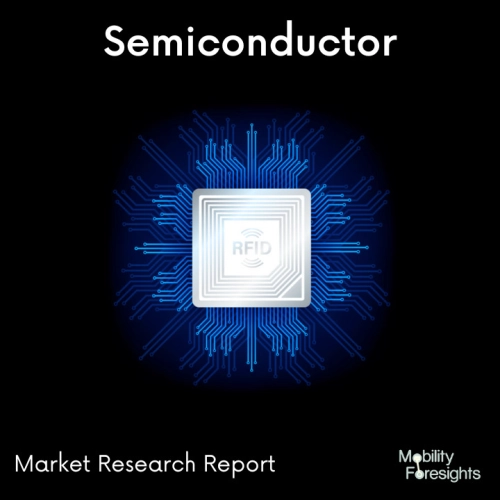
- Get in Touch with Us
Last Updated: Apr 25, 2025 | Study Period:
Wafer Surface Cleaning System is used in order to ensure clean surfaces, the increased number of etch and deposition steps, new materials, and novel structures utilized in 2.5D and 3D packaging strongly rely on cleaning procedures such photoresist strip and descum.
In order to reach the necessary clean levels to assure good devices and high yield, it is increasingly crucial to provide a variety of cleaning alternatives. Devices require variable levels of cleanliness utilizing different materials throughout the production process.
Surface activation, a crucial procedure associated with cleaning, conditions and gets the surface ready for the following step of the process, assuring good adhesion and a high-quality die.
A wafer's surface needs to be cleaned to get rid of any clinging debris and organic/inorganic contaminants before it enters the fabrication process. Additionally, silicon native oxide must be eliminated.
Cleaning methods are becoming more and more crucial to maintaining acceptable product yields as device design regulations are continuously being slashed.
Wafer cleaning processes can account for 30% to 40% of the stages in the overall production process in the creation of contemporary devices. The semiconductor industry has a lengthy development history with wafer cleaning.
S No | Company Name | Development |
1 | Tokyo Electron (TEL) | The single wafer cleaning system for CELLESTA SCD has been introduced by Tokyo Electron (TEL). The CELLESTA line of products from TEL is frequently used to clean silicon wafers for use in the production of semiconductors. The soon-to-be-available CELLESTA SCD incorporates a special supercritical drying chamber on the CELLESTA platform, which has been successfully used in mass production.Low surface tension alcohol solutions are typically used in the drying step of wafer cleaning. |
2 | SCREEN SPE | SCREEN SPE has created the SB-3300 single wafer cleaning system, a first for the industry. The SB-3300 has been specifically created for back-side wafer cleaning and includes scrubber-style brush cleaning as well as chemical cleaning functions. To ensure very efficient removal of particles on the reverse side of wafers, the system executes chemical and brush cleaning procedures simultaneously.During the photolithographic process of developing cutting-edge semiconductor devices, these particles are a key cause of defocusing. |
3 | ACM | In order to provide customers with a cost reduction plan that addresses chemical waste as well as performance goals, ACM has developed a complete system like the Ultra C Tahoe that combines higher throughput with noticeably lower chemical usage. The need to dispose of waste without endangering the environment was a major motivator. The business highlighted that rising demand for cleaning systems that may lower consumption of process chemicals without compromising performance is being driven by (global) regulatory curbs on semiconductor industry waste and awareness of environmental dangers. |
However, CELLESTA SCD pattern collapse during the drying process has emerged as one of the main problems as a result of continuing semiconductor scaling and the usage of multi-layer architectures in highly advanced devices.
TEL has created a pattern collapse-free drying technique that employs a supercritical fluid in reaction and has introduced the technology to the market as machinery for mass production.
With the addition of CELLESTA SCD and its significantly enhanced cleaning and drying technologies to the current line of single wafer cleaning systems.
TEL is able to meet the high-tech requirements of semiconductor manufacture and promote continued expansion of the semiconductor industry.
The SB-3300 is outfitted with SCREEN SPE's unique chuck mechanism, which securely guards the device surface of wafers, preventing both chemical wraparound onto the device surface and etching residue along the wafer edge.
Using densification processing of the nozzle sequence and a chemical dispense control feature, it also offers highly controlled etching. This results in exceptional accuracy and homogeneity over the entire wafer surface, which reduces warping.
The corporation claimed that disposal procedures for sulfuric acid in particular are inadequate. In nations like the United States, landfilling decontaminated garbage is still an option, although it does not entirely eliminate the risk of environmental contamination.
High-temperature purification is the next alternative in places like Korea, Taiwan, and Shanghai where there is little to no space for landfills.Two modules are combined into one wet-clean system by the Ultra C Tahoe cleaning system.
When compared to single wafer SPM cleaning, sulfuric acid waste is reduced due to the recirculation of the SPM process chemicals in the bench module during sulfuric acid-peroxide mixture (SPM) cleaning and quick dump rinsing (QDR).
Wafers are moved to the single wafer module for advanced cleaning while still wet after bench washing in the Tahoe.
The Global Wafer Surface Cleaning System market accounted for $XX Billion in 2023 and is anticipated to reach $XX Billion by 2030, registering a CAGR of XX% from 2024 to 2030.
Sl no | Topic |
1 | Market Segmentation |
2 | Scope of the report |
3 | Abbreviations |
4 | Research Methodology |
5 | Executive Summary |
6 | Introduction |
7 | Insights from Industry stakeholders |
8 | Cost breakdown of Product by sub-components and average profit margin |
9 | Disruptive innovation in the Industry |
10 | Technology trends in the Industry |
11 | Consumer trends in the industry |
12 | Recent Production Milestones |
13 | Component Manufacturing in US, EU and China |
14 | COVID-19 impact on overall market |
15 | COVID-19 impact on Production of components |
16 | COVID-19 impact on Point of sale |
17 | Market Segmentation, Dynamics and Forecast by Geography, 2024-2030 |
18 | Market Segmentation, Dynamics and Forecast by Product Type, 2024-2030 |
19 | Market Segmentation, Dynamics and Forecast by Application, 2024-2030 |
20 | Market Segmentation, Dynamics and Forecast by End use, 2024-2030 |
21 | Product installation rate by OEM, 2023 |
22 | Incline/Decline in Average B-2-B selling price in past 5 years |
23 | Competition from substitute products |
24 | Gross margin and average profitability of suppliers |
25 | New product development in past 12 months |
26 | M&A in past 12 months |
27 | Growth strategy of leading players |
28 | Market share of vendors, 2023 |
29 | Company Profiles |
30 | Unmet needs and opportunity for new suppliers |
31 | Conclusion |
32 | Appendix |