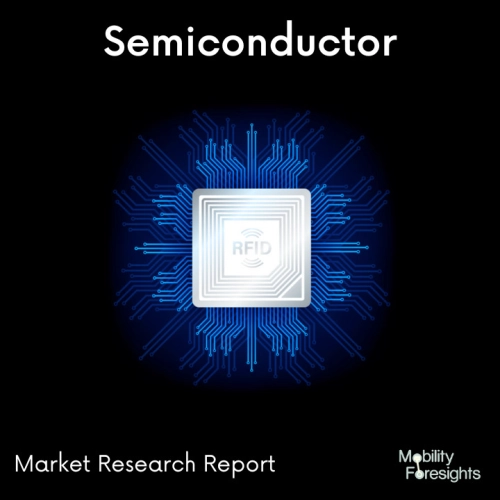
- Get in Touch with Us
Last Updated: Apr 25, 2025 | Study Period: 2024-2030
Wafer Surface Planer used to create flat faces and square edges on wood during initial preparation. Fingers dragged between the fence and guard and coming into contact with the cutters can cause issues. There are four cutters, and eight allen screws are used to hold them horizontally. A gauge is used to adjust the cutter height.
The guard should be set to a distance of no more than 10mm, although caution must be taken to avoid placing it too near to the workpiece because irregular sizes can lead to jamming. Some bridge guards are spring-loaded to accommodate this.
Another risk is using a piece of wood that is too tiny, as backlash might result in fingers coming into touch with cutters. Push blocks must be utilized, and if there aren't enough, take into account other choices like using a sander.
The Global Wafer Surface Planer market accounted for $XX Billion in 2023 and is anticipated to reach $XX Billion by 2030, registering a CAGR of XX% from 2024 to 2030.
Researchers reduced the within-die and within-wafer non uniformity brought on by the inefficient Cu pillar and Si thinning procedures by using the Wafer Surface Planer technique. In a 300-mm wafer, the planarized Cu pillars' height variance was 3.5% of the within-wafer uniformity, which is a significant decrease from the post-electrodeposition height variation.
In addition, after going through the surface planer operation, the topography of the Cu pillar surface was level and consistent. The total thickness variation on the backgrind tape-laminated Cu pillar wafer was 31.77 m. By using a surface planer, this deviation was decreased to 14.55 m.
Grinding was used to thin the bulk Si of the Cu pillar wafer with the planarized backgrind tape to 100 m. Si's overall thickness variation was 1.52 m.Copper pillars that are imbedded in resin are carved out by the surface planer, revealing the pillars.The planarization of these pillars' upper surfaces improves the connection dependability with other devices.
Additionally, we are researching a technique for joining resin pieces that involves planarizing and exposing solder bumps on each resin piece.
Sl no | Topic |
1 | Market Segmentation |
2 | Scope of the report |
3 | Abbreviations |
4 | Research Methodology |
5 | Executive Summary |
6 | Introduction |
7 | Insights from Industry stakeholders |
8 | Cost breakdown of Product by sub-components and average profit margin |
9 | Disruptive innovation in the Industry |
10 | Technology trends in the Industry |
11 | Consumer trends in the industry |
12 | Recent Production Milestones |
13 | Component Manufacturing in US, EU and China |
14 | COVID-19 impact on overall market |
15 | COVID-19 impact on Production of components |
16 | COVID-19 impact on Point of sale |
17 | Market Segmentation, Dynamics and Forecast by Geography, 2024-2030 |
18 | Market Segmentation, Dynamics and Forecast by Product Type, 2024-2030 |
19 | Market Segmentation, Dynamics and Forecast by Application, 2024-2030 |
20 | Market Segmentation, Dynamics and Forecast by End use, 2024-2030 |
21 | Product installation rate by OEM, 2023 |
22 | Incline/Decline in Average B-2-B selling price in past 5 years |
23 | Competition from substitute products |
24 | Gross margin and average profitability of suppliers |
25 | New product development in past 12 months |
26 | M&A in past 12 months |
27 | Growth strategy of leading players |
28 | Market share of vendors, 2023 |
29 | Company Profiles |
30 | Unmet needs and opportunity for new suppliers |
31 | Conclusion |
32 | Appendix |