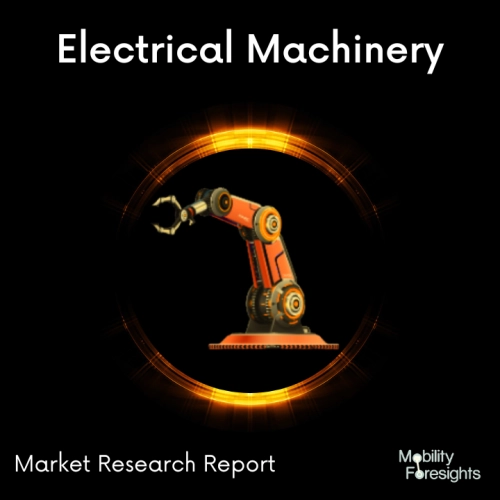
- Get in Touch with Us
Last Updated: Apr 25, 2025 | Study Period: 2024-2030
Without requiring product disassembly, X-ray/CT inspection technologies measure the intricate inner workings of products and find any flaws therein. High-precision nondestructive inspection is a tool that helps manufacturers.
Several imaging modalities, such as Film Radiography, Real Time Radiography (RTR), Computed Tomography (CT), Digital Radiography (DR), and Computed Radiography, are accessible in industrial radiography (CR).
By photographing the projected X-rays that pass through a sample, these devices produce 2D images. In order to create 3D volumetric representations for 3D CT (computed tomography) images, sequential 2D images taken while rotating the sample are reconstructed.
By directing heated electrons at a metal component known as the target, inspection devices generate X-rays.In general, by increasing the voltage in the tube where thermal electrons are produced, stronger X-rays can be produced to penetrate thicker samples.
The resulting X-ray image loses sharpness due to a higher "spot size" (the size of the point on the target at which the heated electrons are concentrated).
Global X-ray CT inspection system market accounted for $XX Billion in 2023 and is anticipated to reach $XX Billion by 2030, registering a CAGR of XX% from 2024 to 2030.
The VT-X750-V3 system, the quickest CT-type X-ray inspection equipment to date, has been developed by OMRON Corporation and it will be made available worldwide on November 20.
To meet the expanding demands of fifth-generation mobile communication systems (5G), electric vehicles (EVs), and autonomous driving application products, the VT-X750-V3 offers advanced, true 3D inspection of electronic substrates.
Through high-speed, 100% X-ray inspection of electronic substrate assemblies with no PCB design constraints, OMRON helps to maintain and improve productivity while simultaneously ensuring the quality of client products.
The need for electronic substrates to support 5G, EVs, and autonomous driving applications has increased quickly in recent years, which is driving up the standards for these substrates' quality. To ensure the dependability, performance, and safety of the finished products, the most stringent inspection is required for these cutting-edge applications because they may involve risks to human life.
As PCBA densification through IC chipping, which involves mounting components on both sides of the board, and further part consolidation to increase the number of components mounted on the board, are advanced, design, manufacturing, and inspection challenges are becoming more complex.
Traditional 2D X-ray imaging techniques are insufficient or incapable of inspecting these components with true accuracy and stability, so 3D inspection has become crucial.
Sl no | Topic |
1 | Market Segmentation |
2 | Scope of the report |
3 | Abbreviations |
4 | Research Methodology |
5 | Executive Summary |
6 | Introduction |
7 | Insights from Industry stakeholders |
8 | Cost breakdown of Product by sub-components and average profit margin |
9 | Disruptive innovation in the Industry |
10 | Technology trends in the Industry |
11 | Consumer trends in the industry |
12 | Recent Production Milestones |
13 | Component Manufacturing in US, EU and China |
14 | COVID-19 impact on overall market |
15 | COVID-19 impact on Production of components |
16 | COVID-19 impact on Point of sale |
17 | Market Segmentation, Dynamics and Forecast by Geography, 2024-2030 |
18 | Market Segmentation, Dynamics and Forecast by Product Type, 2024-2030 |
19 | Market Segmentation, Dynamics and Forecast by Application, 2024-2030 |
20 | Market Segmentation, Dynamics and Forecast by End use, 2024-2030 |
21 | Product installation rate by OEM, 2023 |
22 | Incline/Decline in Average B-2-B selling price in past 5 years |
23 | Competition from substitute products |
24 | Gross margin and average profitability of suppliers |
25 | New product development in past 12 months |
26 | M&A in past 12 months |
27 | Growth strategy of leading players |
28 | Market share of vendors, 2023 |
29 | Company Profiles |
30 | Unmet needs and opportunity for new suppliers |
31 | Conclusion |
32 | Appendix |