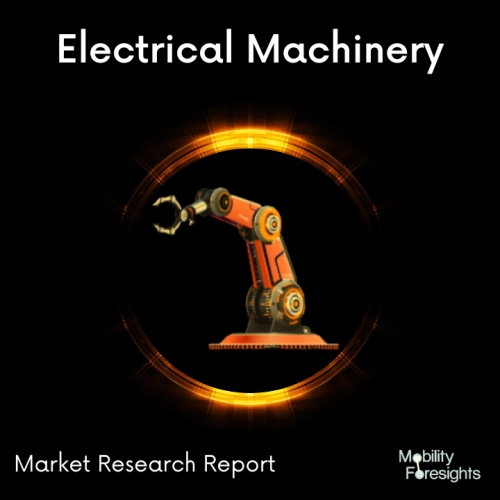
- Get in Touch with Us
Last Updated: Apr 25, 2025 | Study Period: 2024-2030
The sensor head is held steady as the laser beam is scanned across the sample by the XYZ positioning system. The interferometer's probe beam is positioned using the XYZ positioning system, which is also used to scan the area of interest.
Three Smart Act closed-loop positioners are the foundation of the positioning system, and they are housed inside a small protective enclosure. Each positioner has a 50 nm repeatability and a 20 mm maximum scan range.
The lowest positioner is where the sensor head is mounted. The XYZ positioning system is fixed on a post with a 25 mm diameter, allowing for simple height adjustment to accommodate samples of various sizes.
The XYZ stage, which is composed of a motion mechanism driven by actuators for moving an object in the XYZ plane, is a fundamental component of a positioning system used in industries such as micromachining and scanning probe microscopy.
Many of the state-of-the-art ultra-precision XYZ stages have a stage motion mechanism composed of air-bearing or roller bearing supported linear slides, which are driven by linear motors.
Laser interferometers or linear encoders are often used as the feedback sensors. While the conventional XYZ stage is stacked up by two linear stages composed of many components, such as ball screw, bearing, linear slide.
The Global XYZ Positioning System with Controller market accountedfor $XX Billion in 2023 and is anticipated to reach $XX Billion by 2030, registering a CAGR of XX% from 2024 to 2030.
XYZ positioning stages with high accuracy and low cost have been made available by OES (Optimal Engineering Systems) and are simple to integrate into both new and existing applications.
For each axis, they are available in 5 different trip lengths: 50 mm, 100 mm, 150 mm, 200 mm, and 300 mm. There are numerous length, motor, and lead screw options.
Standard on the two-phase stepper motors is a knob for manual adjusting. For position confirmation, the knob can be swapped out for an incremental quadrature encoder.
For closed loop operation and faster operating speeds, a three-phase brushless servo motor with optical encoder is also an option. Lead screws typically have a 4 mm pitch, although a 1 mm per turn lead screw can be used for better resolution.
There are XYZ systems with the appropriate ACS high-performance controller from PI. Two V-417 high-load linear stages with linear motors and absolute-measuring linear encoders make up the basic system, an XY system.
From 204 to 407 mm, combinations of several travel range variations are available. Granite plates are an additional option for the XY systems.
Sl no | Topic |
1 | Market Segmentation |
2 | Scope of the report |
3 | Abbreviations |
4 | Research Methodology |
5 | Executive Summary |
6 | Introduction |
7 | Insights from Industry stakeholders |
8 | Cost breakdown of Product by sub-components and average profit margin |
9 | Disruptive innovation in the Industry |
10 | Technology trends in the Industry |
11 | Consumer trends in the industry |
12 | Recent Production Milestones |
13 | Component Manufacturing in US, EU and China |
14 | COVID-19 impact on overall market |
15 | COVID-19 impact on Production of components |
16 | COVID-19 impact on Point of sale |
17 | Market Segmentation, Dynamics and Forecast by Geography, 2024-2030 |
18 | Market Segmentation, Dynamics and Forecast by Product Type, 2024-2030 |
19 | Market Segmentation, Dynamics and Forecast by Application, 2024-2030 |
20 | Market Segmentation, Dynamics and Forecast by End use, 2024-2030 |
21 | Product installation rate by OEM, 2023 |
22 | Incline/Decline in Average B-2-B selling price in past 5 years |
23 | Competition from substitute products |
24 | Gross margin and average profitability of suppliers |
25 | New product development in past 12 months |
26 | M&A in past 12 months |
27 | Growth strategy of leading players |
28 | Market share of vendors, 2023 |
29 | Company Profiles |
30 | Unmet needs and opportunity for new suppliers |
31 | Conclusion |
32 | Appendix |