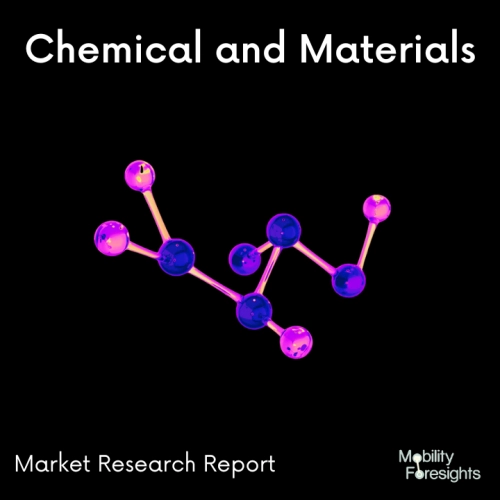
- Get in Touch with Us
Last Updated: Apr 25, 2025 | Study Period: 2024-2030
High performance zinc-nickel alloys provide superior corrosion resistance, especially for items used in challenging situations.A special composition that will corrode less quickly than zinc alone is produced by alloying nickel and zinc. This alloy coating, with a composition of roughly 10-15% nickel and the remaining zinc, can offer up to ten times the protection of traditional zinc plating.
Large Zinc Nickel Parts Zinc-Nickel's excellent corrosion resistance is becoming more and more in demand across industries as a result of things like increased product warranties, longer life cycle requirements, stricter safety regulations, and decreased environmental effect.
Zinc-Nickel alloy application is a two-step technique. A layer of zinc-nickel must be applied to the surface of the component using an electrical current, and the zinc-nickel layer must then be protected with a chromate conversion coating.
The chromate improves the overall performance of the finish by avoiding the production of white rust, while the zinc-nickel deposit shields the part against moisture and corrosion. When choosing the proper chromate, one should take into account the part's intended usage.Hexavalent and trivalent conversion coatings are the two varieties.
Hexavalent chromates provide exceptional corrosion protection at a reasonable price. However, the Reduction of Hazardous Substances Directive (RoHS), which forbids the use of hexavalent chromium in goods exported to the European Union, has resulted in a steady decline in its use.
The Global Zinc Nickel Alloy Market accounted for $XX Billion in 2023 and is anticipated to reach $XX Billion by 2030, registering a CAGR of XX% from 2024 to 2030.
Zinc sacrificial coatings can last longer when coated with alloys like zinc-nickel. Compared to other zinc alloy coatings, zinc-nickel alloy coating has a longer history and is thought to be the best corrosion resistant zinc alloy.
The ductility of coated steel pieces is one of the essential characteristics of this type of coatings, as after thermal treatment and shaping operations, the corrosion resistance is increased to an ideal level. Due to these characteristics, this alloy is being looked into for coating items like connection bolts, brake system parts, and fuel systems.
These coatings also exhibit resistance to heat, ultraviolet radiation, hydraulic fluids, and fuels. The market for bolts and threaded parts is expanding its usage of zinc-nickel alloy coatings.
Sl no | Topic |
1 | Market Segmentation |
2 | Scope of the report |
3 | Abbreviations |
4 | Research Methodology |
5 | Executive Summary |
6 | Introdauction |
7 | Insights from Industry stakeholders |
8 | Cost breakdown of Product by sub-components and average profit margin |
9 | Disruptive innovation in theIndustry |
10 | Technology trends in the Industry |
11 | Consumer trends in the industry |
12 | Recent Production Milestones |
13 | Component Manufacturing in US, EU and China |
14 | COVID-19 impact on overall market |
15 | COVID-19 impact on Production of components |
16 | COVID-19 impact on Point of sale |
17 | Market Segmentation, Dynamics and Forecast by Geography, 2024-2030 |
18 | Market Segmentation, Dynamics and Forecast by Product Type, 2024-2030 |
19 | Market Segmentation, Dynamics and Forecast by Application, 2024-2030 |
20 | Market Segmentation, Dynamics and Forecast by End use, 2024-2030 |
21 | Product installation rate by OEM, 2023 |
22 | Incline/Decline in Average B-2-B selling price in past 5 years |
23 | Competition from substitute products |
24 | Gross margin and average profitability of suppliers |
25 | New product development in past 12 months |
26 | M&A in past 12 months |
27 | Growth strategy of leading players |
28 | Market share of vendors, 2023 |
29 | Company Profiles |
30 | Unmet needs and opportunity for new suppliers |
31 | Conclusion |
32 | Appendix |