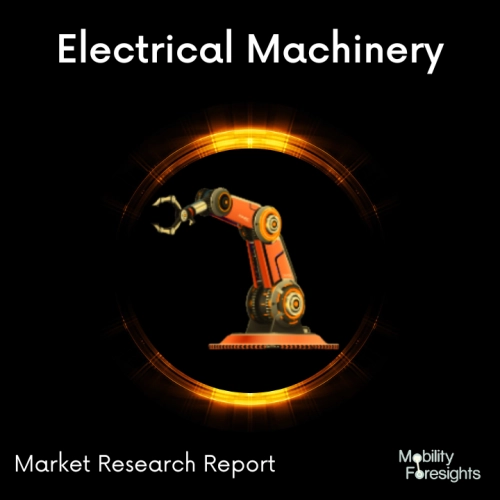
- Get in Touch with Us
Last Updated: Apr 25, 2025 | Study Period: 2024-2030
The Zipper Tester, also known as the Zipper Reciprocating Fatigue Tester, is used to measure the zipper's (or slide fasteners) resistance to reciprocation.
The test specimen is put through a predetermined number of cyclic operations while being put under lateral and longitudinal tension.
To perform the reciprocating movement at a steady speed for 30 times per minute, the Zipper Tester grabs the zipper's head. When the counter reaches a predetermined number of times, the tester immediately ends the test. A sensor in the machine will cause it to shut off automatically before the zipper breaks.
The Global Zipper Testing equipment market accounted for $XX Billion in 2023 and is anticipated to reach $XX Billion by 2030, registering a CAGR of XX% from 2024 to 2030.
To assess the effectiveness of zippers in products with zippers, such as clothing, textiles, auxiliary materials, bags, shoes, etc., a zipper reciprocating tester is employed.
The zipper is reciprocated on the tester at a constant speed of 30 times per minute for the predetermined number of times by the horizontal and vertical tension to assess the zipper's wear resistance and durability. The instrument is made up of a clamp set, a reciprocating motion transmission system, and a display system.
The device moves the sample back and forth 30 times per minute, but it is also possible to adjust the speed (20, 25, 35, and 40 times per minute).
The transverse width of the test fixture is 25 mm wide, the vertical width is 10 mm, and the instrument stroke is 75 mm.
The tool is frequently used to assess the toughness and service life of zippers of various lengths in the fields of clothing accessories, the luggage industry, shoe materials, etc. It provides a database for informing material development and assisting users in accurately assessing the performance of the products.
The results of the test can be used to estimate the service life of zippers that reciprocate based on the vertical and horizontal stress during actual operation. More testing criteria can be met with variable test spacing.
A knob-type clamp with a standard tooth surface can hold the sample securely and rapidly. It also has an automatic counting feature and is convenient and quick.
Sl no | Topic |
1 | Market Segmentation |
2 | Scope of the report |
3 | Abbreviations |
4 | Research Methodology |
5 | Executive Summary |
6 | Introduction |
7 | Insights from Industry stakeholders |
8 | Cost breakdown of Product by sub-components and average profit margin |
9 | Disruptive innovation in the Industry |
10 | Technology trends in the Industry |
11 | Consumer trends in the industry |
12 | Recent Production Milestones |
13 | Component Manufacturing in US, EU and China |
14 | COVID-19 impact on overall market |
15 | COVID-19 impact on Production of components |
16 | COVID-19 impact on Point of sale |
17 | Market Segmentation, Dynamics and Forecast by Geography, 2024-2030 |
18 | Market Segmentation, Dynamics and Forecast by Product Type, 2024-2030 |
19 | Market Segmentation, Dynamics and Forecast by Application, 2024-2030 |
20 | Market Segmentation, Dynamics and Forecast by End use, 2024-2030 |
21 | Product installation rate by OEM, 2023 |
22 | Incline/Decline in Average B-2-B selling price in past 5 years |
23 | Competition from substitute products |
24 | Gross margin and average profitability of suppliers |
25 | New product development in past 12 months |
26 | M&A in past 12 months |
27 | Growth strategy of leading players |
28 | Market share of vendors, 2023 |
29 | Company Profiles |
30 | Unmet needs and opportunity for new suppliers |
31 | Conclusion |
32 | Appendix |