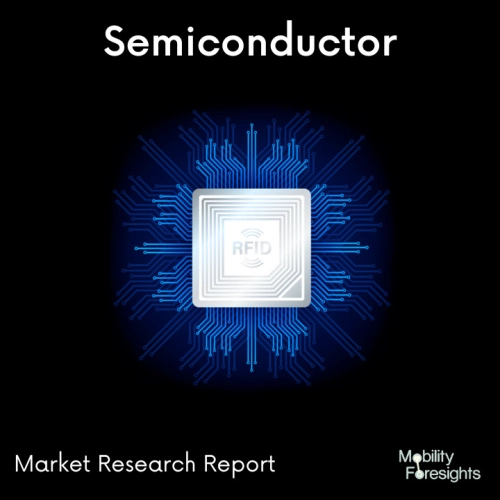
- Get in Touch with Us
Last Updated: Apr 25, 2025 | Study Period: 2023-2030
Plasma etching is the process of removing material from a surface using a plasma source. In order to treat a sample, a suitable plasma gas mixture must be pulsed at the sample. There are two types of plasma sources: charged (ions) and neutral (etch species) (atoms and radicals).
The use of plasma to etch or remove material from a polymer substrate, oxide, metal, glass, or ceramic is known as a plasma etcher. It is possible to clean, etch, and deposit compounds on surfaces using the highly ionised gas known as plasma.
Chemical etching is the process of removing material from a substrate with chemicals. The use of plasma to etch or remove material from a polymer substrate, oxide, metal, glass, or ceramic is known as a plasma etcher. It is possible to clean, etch, and deposit compounds on surfaces using the highly ionised gas known as plasma. Chemical etching is the process of removing material from a substrate with chemicals.
The global 12-chamber plasma etch system market accounted for $XX Billion in 2022 and is anticipated to reach $XX Billion by 2030, registering a CAGR of XX% from 2023 to 2030.
The Episode UL series of etch systems was introduced and allows for flexible configuration with up to 12 chambers. EpisodeTM UL dramatically increases clients' fab production thanks to footprint savings, ease of maintenance, and TEL's unique smart tool technology. Its high productivity and outstanding process performance assist semiconductor devices' expanding range of applications and hasten their growth.
Episode UL was created to increase the productivity of TEL clients' fabs. It has a number of benefits, such as variable multi-chamber configurations, considerable footprint savings, ease of maintenance, and cutting-edge Smart tool features.
The first rectangular cluster system with processing chambers arranged in two rows that are horizontally opposed was created by TEL. Depending on the fab layouts of the customer, Episode UL may flexibly accommodate between 4 and 12 chambers to maximise loading capacity.
The new platform's horizontally opposed cluster design delivers a considerable reduction in footprint per chamber for both cleanroom and utility areas, with a maximum 12 chamber configuration. Additionally, EpisodeTM UL is easier to maintain than its predecessors because to a wider room for maintenance.
A multitude of sensors and high-speed control systems are included into its transfer system and process modules, enabling autonomous process control using big data analytics and TEL's in-house smart tool technology.
Sl no | Topic |
1 | Market Segmentation |
2 | Scope of the report |
3 | Abbreviations |
4 | Research Methodology |
5 | Executive Summary |
6 | Introduction |
7 | Insights from Industry stakeholders |
8 | Cost breakdown of Product by sub-components and average profit margin |
9 | Disruptive innovation in the Industry |
10 | Technology trends in the Industry |
11 | Consumer trends in the industry |
12 | Recent Production Milestones |
13 | Component Manufacturing in US, EU and China |
14 | COVID-19 impact on overall market |
15 | COVID-19 impact on Production of components |
16 | COVID-19 impact on Point of sale |
17 | Market Segmentation, Dynamics and Forecast by Geography, 2023-2030 |
18 | Market Segmentation, Dynamics and Forecast by Product Type, 2023-2030 |
19 | Market Segmentation, Dynamics and Forecast by Application, 2023-2030 |
20 | Market Segmentation, Dynamics and Forecast by End use, 2023-2030 |
21 | Product installation rate by OEM, 2023 |
22 | Incline/Decline in Average B-2-B selling price in past 5 years |
23 | Competition from substitute products |
24 | Gross margin and average profitability of suppliers |
25 | New product development in past 12 months |
26 | M&A in past 12 months |
27 | Growth strategy of leading players |
28 | Market share of vendors, 2023 |
29 | Company Profiles |
30 | Unmet needs and opportunity for new suppliers |
31 | Conclusion |
32 | Appendix |