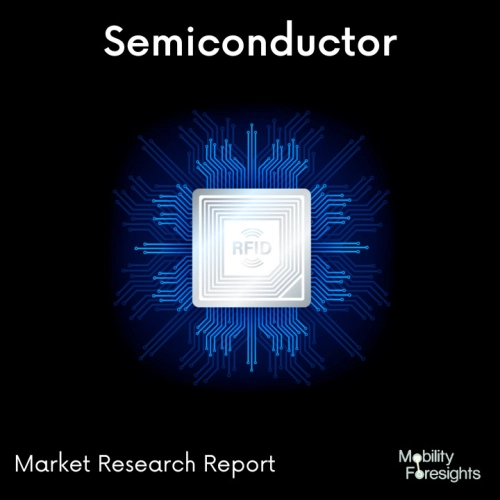
- Get in Touch with Us
Last Updated: Apr 25, 2025 | Study Period: 2024-2030
The quantity and frequency of vibration in a system, machine, or piece of equipment are measured by a vibration sensor. These metrics can be used to identify imbalances or other problems with the asset and foresee upcoming failures.
Vibration sensors, which assist in quickly identifying abnormal vibration in industrial equipment, reduce the risk of machine failure. Numerous end-use sectors, such as oil & gas, processing, automotive, energy & power, consumer electronics, aerospace & military, healthcare, and others, have adopted the use of vibration sensors.
A vibration sensor can either wirelessly monitor an asset or connect directly to it. Depending on the type of sensor used, it will use different techniques to detect vibrations coming from the asset after it is in place.
The Global 3-axis vibration sensor market accounted for $XX Billion in 2023 and is anticipated to reach $XX Billion by 2030, registering a CAGR of XX% from 2024 to 2030.
The M-A342VD10 and the M-A542VR10, both new vibration sensors from Seiko Epson Corporation, include RS422 interfaces that are water- and dust-resistant. Both products meet the requirements of ISO 10816 and ISO 20816's motor assessment criteria.
Due to the crystal vibration sensor components being made utilising Epson's exclusive microfabrication technique, both are three-axis vibration sensors with digital velocity and displacement output that exhibit low noise, high stability, and low power consumption.
A new vibration-sensing solution from STMicroelectronics has been released that is designed to facilitate intelligent maintenance of production equipment. The STEVAL-STWINKT1 multi-sensor evaluation kit with ST's IIS3DWB vibration sensor speeds up the creation of condition-monitoring systems that increase production by predicting the need for equipment maintenance.
Sl no | Topic |
1 | Market Segmentation |
2 | Scope of the report |
3 | Abbreviations |
4 | Research Methodology |
5 | Executive Summary |
6 | Introduction |
7 | Insights from Industry stakeholders |
8 | Cost breakdown of Product by sub-components and average profit margin |
9 | Disruptive innovation in the Industry |
10 | Technology trends in the Industry |
11 | Consumer trends in the industry |
12 | Recent Production Milestones |
13 | Component Manufacturing in US, EU and China |
14 | COVID-19 impact on overall market |
15 | COVID-19 impact on Production of components |
16 | COVID-19 impact on Point of sale |
17 | Market Segmentation, Dynamics and Forecast by Geography, 2024-2030 |
18 | Market Segmentation, Dynamics and Forecast by Product Type, 2024-2030 |
19 | Market Segmentation, Dynamics and Forecast by Application, 2024-2030 |
20 | Market Segmentation, Dynamics and Forecast by End use, 2024-2030 |
21 | Product installation rate by OEM, 2023 |
22 | Incline/Decline in Average B-2-B selling price in past 5 years |
23 | Competition from substitute products |
24 | Gross margin and average profitability of suppliers |
25 | New product development in past 12 months |
26 | M&A in past 12 months |
27 | Growth strategy of leading players |
28 | Market share of vendors, 2023 |
29 | Company Profiles |
30 | Unmet needs and opportunity for new suppliers |
31 | Conclusion |
32 | Appendix |