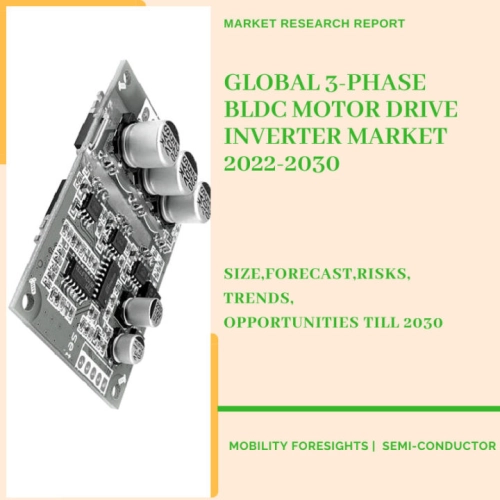
- Get in Touch with Us
Last Updated: Apr 25, 2025 | Study Period: 2022-2030
A brushless DC motor is operated by a three phase inverter. They operate on the same basis as brushless DC motors. In a variety of application areas, small high-speed BLDC motors have gained tremendous popularity. Because it lacks a mechanical commutator, the BLDC motor is more dependable than the DC motor.
Small, high-speed BLDC motors have a significantly lower inductance than standard BLDC motors. A BLDC motor's current follows the PWM voltage's rectangular shape when PWM control is used to control the motor's phases.
The motor iron is magnetised and demagnetized by this quickly varying current at a frequency equal to the PWM frequency. The motor may heat up to the point of failure due to magnetic hysteresis losses, and the high current ripple will result in further losses.
The Global 3-phase BLDC motor drive inverter market accounted for $XX Billion in 2021 and is anticipated to reach $XX Billion by 2030, registering a CAGR of XX% from 2022 to 2030.
Shortening the rise and fall times of the VDS of the MOSFET(s) being driven is made possible by the 3.5 and 4.5 amp peak source and sink gate drive currents provided by the DRV325x-Q1 set of MOSFET gate driver units (GDU). The units have a MOSFET operating voltage range of 90 volts and are designed for 48-volt applications.
Texas Instruments (TI) asserts that the DRV3255-Q1 is the first 3-phase half-bridge BLDC motor driver in the market to have both high-side and low-side active short circuit logic.
It offers protection against switching transients of up to 95 volts and is intended for 48-volt power systems. It accommodates hybrid cars with up to 30 kW of electric motor power.
The unit's high level of integration will also help to eliminate between 12 and 24 passive components, according to TI.
Sl no | Topic |
1 | Market Segmentation |
2 | Scope of the report |
3 | Abbreviations |
4 | Research Methodology |
5 | Executive Summary |
6 | Introduction |
7 | Insights from Industry stakeholders |
8 | Cost breakdown of Product by sub-components and average profit margin |
9 | Disruptive innovation in the Industry |
10 | Technology trends in the Industry |
11 | Consumer trends in the industry |
12 | Recent Production Milestones |
13 | Component Manufacturing in US, EU and China |
14 | COVID-19 impact on overall market |
15 | COVID-19 impact on Production of components |
16 | COVID-19 impact on Point of sale |
17 | Market Segmentation, Dynamics and Forecast by Geography, 2022-2030 |
18 | Market Segmentation, Dynamics and Forecast by Product Type, 2022-2030 |
19 | Market Segmentation, Dynamics and Forecast by Application, 2022-2030 |
20 | Market Segmentation, Dynamics and Forecast by End use, 2022-2030 |
21 | Product installation rate by OEM, 2022 |
22 | Incline/Decline in Average B-2-B selling price in past 5 years |
23 | Competition from substitute products |
24 | Gross margin and average profitability of suppliers |
25 | New product development in past 12 months |
26 | M&A in past 12 months |
27 | Growth strategy of leading players |
28 | Market share of vendors, 2022 |
29 | Company Profiles |
30 | Unmet needs and opportunity for new suppliers |
31 | Conclusion |
32 | Appendix |