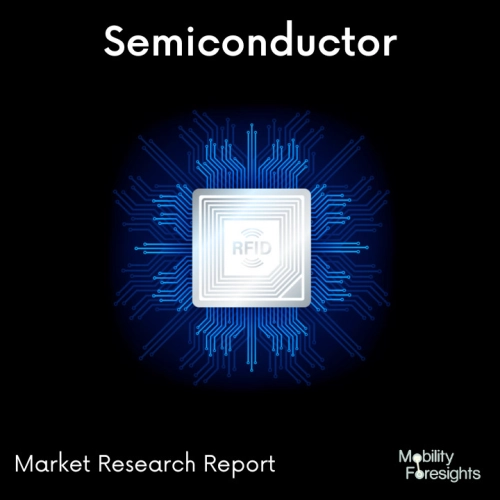
- Get in Touch with Us
Last Updated: Apr 25, 2025 | Study Period:
An important tool for determining the strength of a magnetic field is a 3D magnetic position sensor. It can detect linear, angular, rotational, and three-dimensional motions, and it can communicate the data using an output interface.
Using a wide variety of sensing technologies, position sensors can be utilised to monitor either linear or rotating position.
Position sensors are utilised in a wide range of applications; anything that calls for the measurement of movement will employ a particular sort of position sensor.
A 3D position sensor is a specialized device that measures and reports the three-dimensional coordinates of an object or point in space. These sensors are employed in various applications where precise spatial information is crucial. One notable application is in virtual reality (VR) and augmented reality (AR) systems.
In VR gaming, for instance, headsets often incorporate 3D position sensors to track the movement and orientation of the user's head in real-time. In robotics, 3D position sensors play a fundamental role in enabling robots to perceive and interact with their environment.
Medical applications also benefit from 3D position sensors. Surgical navigation systems use these sensors to track the position of surgical instruments and create 3D maps of the patient's anatomy in real-time during surgeries.
S.NO | Overview of Development | Details of Development |
1. | Allegro introduces a new magnetic-position sensor for automotive use. | The newest member of the 3DMAG family of rotary and linear magnetic-position sensor ICs for automotive and industrial applications, the A31315 sensor, has been released, according to Allegro MicroSystems, Inc., a global provider of power and sensing solutions for motion control and energy-efficient systems. In order to measure magnetic-field components along three axes (X, Y, and Z), |
2. | TI Introduces a 3D Hall-Effect Position Sensor | The most precise 3D Hall-effect position sensor in the industry was unveiled by Texas Instruments (TI). Engineers can obtain uncalibrated ultra-high precision with the TMAG5170 at rates up to 20 kSPS for quicker and more precise real-time control in motor-drive and factory automation applications. While utilizing at least slightly less power than comparable devices, the sensor also offers integrated functions and diagnostics to maximize design flexibility and system safety. |
3. | Allegro MicroSystems Releases a PCB-Free 3D Magnetic Sensor for Vehicle Safety and ADAS Applications.
| The A31316 3D Hall-effect position sensor was introduced by Allegro MicroSystems, Inc., a world pioneer in sensing and power solutions for motion control and energy-efficient systems. This new sensor is perfect for automotive safety and advanced driver assistance systems (ADAS) applications that need high levels of flexibility and reliable performance in challenging conditions like powertrain and chassis applications, as well as industrial applications that need linear or rotary sensing. It is offered in the industry's smallest 4 4 mm body PCB-less package. |
the new 3DMAG sensors integrate Allegro's tried-and-tested planar and vertical Hall-effect technologies. This gives them real 3D-sensing capabilities with a broad magnetic dynamic range without saturation.
Due to the sensors' adaptable 3D Hall front-end and configurable signal processing architecture, they can measure absolute linear position and rotating position up to 360° with high accuracy, which reduces the difficulty of system integration.
The TMAG5170 is the first product in a new series of 3D Hall-effect position sensors that will serve a variety of industrial demands, from general use to ultra-high performance.
A growing number of highly automated systems in smart factories are required to work in a more integrated manufacturing flow while also gathering data to govern processes. Automated equipment needs 3D position-sensing technology to instantly give precise real-time control for better system efficiency and performance while minimizing downtime. This technology has higher precision, speed, and power efficiency.
Vibrations and pollutants from the environment can impair the functioning of shifter systems, passenger restraint systems, and powertrain and chassis applications. When a position sensor is needed in a dirty, high-vibration environment, the assembly of system components can become corrupted by debris and vibration, which can impair the performance of the assembly.
Support components, such as PCBs and capacitors, are typically required for position sensors used in powertrain and chassis applications. In many industrial linear and rotational sensing applications, the same is true. Fitting strong designs within the available unclean, noisy space is a problem for designers.
The Global 3D position sensor market accounted for $XX Billion in 2023 and is anticipated to reach $XX Billion by 2030, registering a CAGR of XX% from 2024 to 2030.
Melexis' 3D magnetic position sensors completely transform the market. With the launch of the MLX9042x series, Melexis broadened its selection of 3D magnetic position sensing systems.
These sensors are designed for automotive customers that are on a budget but yet need to correctly and safely monitor absolute position in loud, demanding situations.
The primary target market for the solutions is the automobile industry, specifically customers working on applications like powertrain actuators, transmission sensors, pedal position sensors, and chassis sensors. Improvements made possible by them will also help industrial clients.
The MLX9042x devices all include analogue signal conditioning, data conversion, and signal processing, as well as output stage drivers.
They are based on Triaxis Hall sensor technology, which Melexis invented.The MLX9042x offer comparable performance to the items in the MLX9037x family to assure first-time-right EMC testing.
Because only one test cycle is needed, the design may advance fast and affordably. Reverse polarity is included in the high absolute maximum ratings (AMR), which lowers the frequency of quality events brought on by electrical overstress and enables the fulfilment of varied OEM standards.
These tools enable the design of functionally safe actuators and sensors to guarantee the safe functioning of the vehicle, and they are ASIL B ready (per ISO 26262).
Dual die variants are additionally offered to single die versions for applications demanding a higher level of availability and safety.Support for operational temperatures of 160 °C is another important benefit.
Position sensing applications in hot situations, such as compact engine compartments or when start-stop conditions result in higher heat soaks, are made possible by the high temperature capability.
Sl no | Topic |
1 | Market Segmentation |
2 | Scope of the report |
3 | Abbreviations |
4 | Research Methodology |
5 | Executive Summary |
6 | Introduction |
7 | Insights from Industry stakeholders |
8 | Cost breakdown of Product by sub-components and average profit margin |
9 | Disruptive innovation in the Industry |
10 | Technology trends in the Industry |
11 | Consumer trends in the industry |
12 | Recent Production Milestones |
13 | Component Manufacturing in US, EU and China |
14 | COVID-19 impact on overall market |
15 | COVID-19 impact on Production of components |
16 | COVID-19 impact on Point of sale |
17 | Market Segmentation, Dynamics and Forecast by Geography, 2024-2030 |
18 | Market Segmentation, Dynamics and Forecast by Product Type, 2024-2030 |
19 | Market Segmentation, Dynamics and Forecast by Application, 2024-2030 |
20 | Market Segmentation, Dynamics and Forecast by End use, 2024-2030 |
21 | Product installation rate by OEM, 2023 |
22 | Incline/Decline in Average B-2-B selling price in past 5 years |
23 | Competition from substitute products |
24 | Gross margin and average profitability of suppliers |
25 | New product development in past 12 months |
26 | M&A in past 12 months |
27 | Growth strategy of leading players |
28 | Market share of vendors, 2023 |
29 | Company Profiles |
30 | Unmet needs and opportunity for new suppliers |
31 | Conclusion |
32 | Appendix |