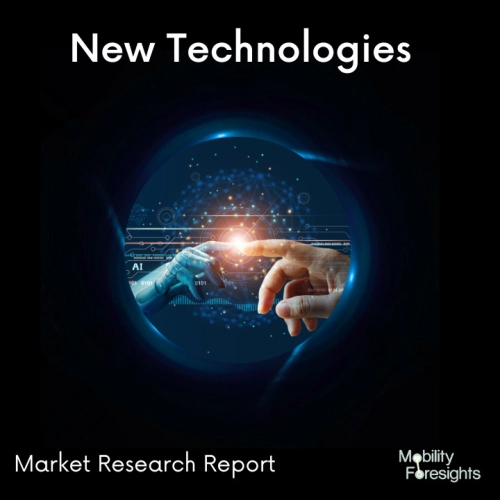
- Get in Touch with Us
Last Updated: Apr 25, 2025 | Study Period: 2024-2030
An advanced imaging technology called a 3D Time of Flight (TOF) camera uses the time-of-flight principle to record three-dimensional data about its surroundings. This state-of-the-art camera sends out brief light pulses and measures how long it takes for the pulses to reach objects and return.
The camera builds a depth map by calculating the time delay, which enables it to precisely sense the distances and sizes of objects in its range of vision. Robotics, augmented reality, virtual reality, and autonomous vehicles are just a few of the areas where 3D TOF cameras are being used to revolutionise how machines perceive and interact with their surroundings.
They are indispensable for activities like object recognition, gesture tracking, and spatial mapping thanks to their accurate depth sensing capabilities, which spur innovation across industries.
The machine vision industry is being revolutionised by 3D Time-of-Flight (TOF) technology, which offers 3D imaging using an active modulated light source and a low-cost CMOS pixel array. TOF cameras are an appealing choice for a variety of applications due to their small size, simplicity of use, excellent accuracy, and frame rate.
A modulated light source is used to illuminate the scene in a 3D time-of-flight (TOF) camera, which then looks at the reflected light. The distance is calculated from the phase shift between the illumination and the reflection.
S No | Company Name | Development |
1 | SICK | Together, we can concentrate on the wider picture by using time-of-flight 3D vision cameras. Industrial automation necessitates the use of 3D time-of-flight cameras, which have an acute eye. SICK has shown impeccable timing in a project involving several departments by simultaneously releasing two such vision systems, each of which has raised the bar in its industry. |
2 | Terabee | By gathering non-intrusive depth image data, Terabee 3D Time-of-Flight technology helps to assure that no one's identity is ever taken.Due to the fact that these devices don't require ambient light for maximum operation, applications can be created for low-light conditions or even complete darkness. |
3 | Schmersal Group | The Schmersal Group will debut a 3D camera for the automated acquisition of digital process data in real time. The AM-T100 is a Time-of-Flight (ToF) camera that employs a Sony DepthSense sensor to create millimetre-accurate 3D depth photographs. The camera employs ToF technology, which is a runtime measurement of emitted infrared light pulses (850 Nm) that are reflected off the things being captured. |
The blaze 3D TOF camera is made by Basler, a top producer of industrial cameras, and employs Time of Flight technology to record 3D data and pictures of the highest quality. Several industrial applications, such as logistics, robotics, and automation, can make use of the blaze camera. The flame camera has a distinctive design that enables it to record 3D data despite poor illumination.
It measures the amount of time it takes for light to bounce off of objects in the scene and return to the camera by combining infrared illumination with a high-speed sensor.With the use of this data, an accurate and detailed 3D representation of the scene is produced. With a variety of choices for modifying its performance to suit certain applications, the blaze camera is also quite adaptable.
In addition to point cloud data, depth maps, and 3D mesh models, it supports a range of output formats. It may be set up to record color information in addition to depth information, enabling the development of rich, accurate 3D representations of real-world situations. The Basler blaze 3D TOF camera, which offers high-quality 3D imaging and data gathering in a durable and dependable compact, is a useful tool for a variety of industrial applications.
Leading semiconductor manufacturer STMicroelectronics creates a variety of cutting-edge sensors and imaging systems. The VL53L1X sensor is one of its main offerings for 3D Time of Flight (TOF) cameras.
Using ST's patented FlightSenseTM technology, the VL53L1X is a tiny, power-efficient sensor that can precisely gauge the distance to an object under a variety of lighting conditions. The sensor is perfect for usage in a range of applications, including mobile devices, robotics, and industrial automation.
It can detect objects up to four meters away with millimeter-level precision. The VL53L1X's tiny size, which makes it simple to integrate into a variety of devices, is one of its important characteristics.
One of the tiniest TOF sensors on the market, the sensor has dimensions of about 4.9mm x 2.5mm x 1.56mm. It is also ideal for battery-powered gadgets because of how little power it uses. Additionally, the VL53L1X has a wide range of settings that can be modified to fit various applications. The sensor may be set to produce data in a number of forms, including raw data, distance, and signal quality. Supported modes include single, continuous, and timed measurements.
A highly powerful and adaptable 3D TOF camera sensor, the STMicroelectronics VL53L1X is ideal for a variety of applications. It is a preferred option for product developers and engineers wishing to implement 3D TOF technology into their creations because to its compact size, low power consumption, and great precision.
Under the DepthSense brand, Sony manufactures a variety of 3D Time of Flight (TOF) cameras. The DepthSense DS311 is one of their best-selling items. A high-performance 3D TOF camera for usage in industrial and commercial applications is the DepthSense DS311.
A wide field of vision, excellent resolution, and quick frame rates are just a few of its many innovative features. The DepthSense DS311's capability to precisely gauge the distance between the camera and scene's objects is one of its standout characteristics.
It is therefore perfect for a variety of uses, such as robotics, automation, and 3D scanning. High Dynamic Range (HDR) photography and low light sensitivity are only two further sophisticated imaging characteristics of the camera.
The AM-T100the first line on which SICK and Microsoft worked together to develop 3D ToF technology. The safeVisionary2 camera, which at first look appears to be nearly identical to the Mini (apart from color), is the first 3D ToF camera in the world to reach the demanding Performance Level c standard in line with ISO 13849, and yellow stands for the highest safety requirements.
Time-of-flight (3D ToF) is a technique for calculating the amount of time it takes for a light signal to simultaneously go from a camera to a target at each point in the image. The distance to the object can be calculated after the arrival time or phase shift of the reflected light is known.
For instance, the SICK Visionary-T Mini offers over 6.5 million 3D distance data points per second on an extremely reliable platform. This technique, often referred to as 3D snapshot technology, uses time-of-flight measurement to obtain a three-dimensional image of even static scenes without the usage of actuators or other moving mechanical components in the camera.
With its small, light, and reasonably priced 3D Time-of-Flight cameras and multi-pixel sensors, it creates apps to measure volume, identify motions, and record movement. Take use of features that enable a variety of applications, such as factory-calibrated depth data, adjustable working modes, and others.
Activate programs that use 88, 8060, or VGA pixel resolution for depth sensing. Create useful and actionable data from people's movement for occupancy monitoring and smart building management. 3D Time-of-Flight technology operates in all lighting circumstances, including complete darkness, and is by design GDPR compliant.
The AM-T100 allows for the rapid production of a 3D image of the scene with millimetre accuracy, which is then provided as a point cloud. The fast image rate of up to 60 frames per second enables efficient application in industrial manufacturing processes, logistics, and robots.
The camera can also identify the current fill level of containers or huge load carriers by 'seeing into' them. Furthermore, the camera aids in general cargo volume determination as well as birds-eye monitoring of staging areas in production, assembly, storage, and order picking. Other applications include dimension and surface quality capture. The AM-T100 reaches a visible range of 67° x 51° at a range of 6 metres thanks to high-performance IR lighting and an image resolution of 640 x 480 pixels.
The Global 3D TOF (Time of Flight) Camera market accounted for $XX Billion in 2023 and is anticipated to reach $XX Billion by 2030, registering a CAGR of XX% from 2024 to 2030.
Launched by e-con Systems, DepthVista is a Time of Flight (ToF) camera that combines a ToF depth sensor for measuring depth with an Onsemi AR0234 colour global shutter sensor for object identification. 640480 depth maps can be recorded using the high-resolution depth camera DepthVista at a frame rate of 30 frames per second.
In a single, portable form-factor, the iTOF (indirect Time-of-Flight) depth camera called DepthVista provides 3D depth information, an IR image, and a corresponding RGB image.
The new HeliosTM2+ 3D Time-of-Flight (ToF) camera has been introduced by LUCID Vision Labs, Inc. High-Speed Mode and HDR Mode are two brand-new on-camera depth processing modes that are available. For correct depth information in high contrast, complex images with both high and low reflectivity objects, the HDR Mode combines many exposures in the phase domain.
Sl no | Topic |
1 | Market Segmentation |
2 | Scope of the report |
3 | Abbreviations |
4 | Research Methodology |
5 | Executive Summary |
6 | Introduction |
7 | Insights from Industry stakeholders |
8 | Cost breakdown of Product by sub-components and average profit margin |
9 | Disruptive innovation in the Industry |
10 | Technology trends in the Industry |
11 | Consumer trends in the industry |
12 | Recent Production Milestones |
13 | Component Manufacturing in US, EU and China |
14 | COVID-19 impact on overall market |
15 | COVID-19 impact on Production of components |
16 | COVID-19 impact on Point of sale |
17 | Market Segmentation, Dynamics and Forecast by Geography, 2024-2030 |
18 | Market Segmentation, Dynamics and Forecast by Product Type, 2024-2030 |
19 | Market Segmentation, Dynamics and Forecast by Application, 2024-2030 |
20 | Market Segmentation, Dynamics and Forecast by End use, 2024-2030 |
21 | Product installation rate by OEM, 2023 |
22 | Incline/Decline in Average B-2-B selling price in past 5 years |
23 | Competition from substitute products |
24 | Gross margin and average profitability of suppliers |
25 | New product development in past 12 months |
26 | M&A in past 12 months |
27 | Growth strategy of leading players |
28 | Market share of vendors, 2023 |
29 | Company Profiles |
30 | Unmet needs and opportunity for new suppliers |
31 | Conclusion |
32 | Appendix |