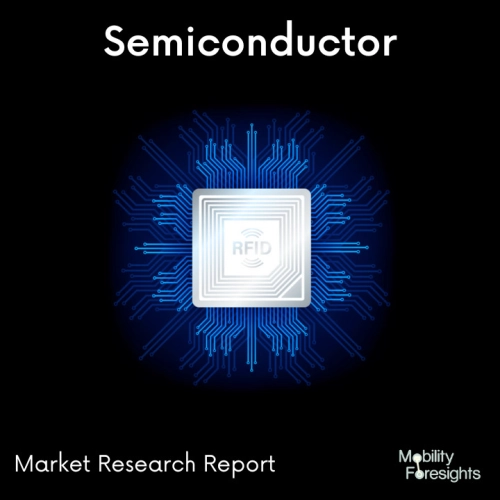
- Get in Touch with Us
Last Updated: Apr 25, 2025 | Study Period:
A system or device that acquires and analyses three-dimensional (3D) visual data is known as a 3D vision sensor. Historically, 3D machine vision systems that offer height, width, and depth data have been expensive, challenging to install, and difficult to maintain. These devices are difficult to program and maintain while also posing extra eye safety problems due to their laser light, even if they are factory calibrated to create 3D data.
A more effective system would combine a sensor, laser, and potent computer in a small package, together with all the other elements required for a 3D solution.
Additionally, it would use real 3D algorithms on 3D point clouds in an intuitive programming environment rather than requiring designers to learn specific code to implement 2D algorithms in 3D applications using less precise surface maps.
As a result, accuracy would be increased while complexity was decreased, and it would also be more capable and sturdy for a range of installations.
S No | Company Name | Development |
---|---|---|
1 | Fanuc | Fanuc has introduced a new 3D vision sensor with a larger field of view. In comparison to existing models in the lineup, the new sensor has a wider field of view and is intended for use in a variety of tasks, such as bin picking, supplying an assembly line or stacking pallets. |
2 | Oxford Vision and Sensor Technology (OVST) | The smallest 3D vision sensor developed by Oxford Vision and Sensor Technology (OVST) has been launched. With a footprint akin to a smartphone, the new MaxVision sensor is intended to be the smallest on the market. With the help of extremely bright LEDs, the MaxVision sensor creates its own illumination. |
3 | SICK | The TriSpector 1000, a self-contained, easily installed, and 'plug-and-play' 3D vision sensor from SICK, has been made available in the UK. It offers real-time 3D quality assessment. The TriSpector 1000, developed by SICK in close collaboration with customers throughout the world, is anticipated to make 3D vision sensing accessible and cost-effective for a variety of processing and packaging activities. |
The Fanuc 3DV/600 is a complete 2D Camera Package, 3D Laser Sensor, and 3D Area Sensor that is a part of a high-performance, highly-integrated portfolio for industrial image processing. The 3DV/600 is a useful and user-friendly addition to the line that may be permanently installed in a system or temporarily mounted on a robot's last axis.
The 3DV/600 can be used with the iRPickTool for usage on a conveyor belt, and it can pick up things even if they are irregularly shaped or lack a clearly defined pick-up point due to its high level of integration and swift image processing. Because the 3DV/600 is pre-calibrated, installation is as simple as feasible. After the sensor is placed, all the robot has to do is determine where its "eyes" are.
Oxford Vision and Sensor Technology (OVST) Depending on the sensor mode, white and red LEDs are utilised in combination to produce the ideal lighting. One GigE connection serves as the medium for all communication. The high-bandwidth transmission assures that the sensor will sample images quickly.
To guard against unintentional damage, the MaxVision sensor is enclosed in a durable anodized aluminium casing.This functionality is contained in a container that weighs less than 600 grammes and measures just 180 mm by 46 mm. This sensor can be utilised for almost any machine vision guided robot application thanks to its light weight and ease of installation on almost any robot.
SICK It will offer real 'out-of-the-box' 3D vision without the complexity or expense of current 3D vision solutions to FMCG product pick, placement & packaging operations, contract packers, and warehouse operators. Without the need to create customised programmes, the SICK TriSpector 1000 can be configured as a fully self-contained machine utilising SICK's SOPAS software interface.
The Global 3D vision sensor market accounted for $XX Billion in 2023 and is anticipated to reach $XX Billion by 2030, registering a CAGR of XX% from 2024 to 2030.
A new 3D vision sensor from the FH-SMD Series has been launched by OMRON Corporation. The FH-SMD Series may be put on a robot to recognize randomly positioned automotive parts in three dimensions, allowing for more productive and space-efficient pick & place, inspection, and assembly tasks that are challenging for traditional robotics.
Through comprehensive solutions that incorporate robots and automation tools, OMRON continues to contribute to bringing innovation to manufacturing sites. These days, finding production personnel is difficult, and labor expenses have increased significantly.
Manufacturers are under a lot of pressure right now to automate procedures that depend on the perception of skilled human workers. The new FH-SMD Series 3D Vision Sensor is so compact and light that it can be attached to a robot arm without the use of special mounting tools, saving both time and space.
This sensor may be adjusted to adjust perspectives and quickly identify components, minimizing blind areas and supplying dependable detection. Additionally, regardless of shape or location, the newly created 3D measurement technology enables part detection in about 0.4 seconds. Bulk part assembly can be easily mechanized.
In addition to seeing their surroundings, 3D machine vision systems are also able to locate and determine the orientation of objects. The typical components of these systems are a number of cameras or a single or several laser displacement sensors.
Surface inspection and volume measurement are two examples of applications that use laser displacement sensors and can generate 3D data with as few as one camera. Similar to line scanning, in these circumstances the object or camera needs to be moved to scan the complete product.
Then the location of the reflected lasers on an item is displaced, producing a height map. Displacement sensors can detect factors like surface height and planarity with accuracy to within 20 m with the aid of a calibrated offset laser.
A distinct method is employed by multi-camera systems in 3D vision applications. These systems use laser triangulation to produce a point cloud, or a digital representation of an object's form and location. Changes in contrast, colour, illumination, and position are just a few unanticipated factors that are taken into consideration by 3D mapping.
For applications like metrology, navigation, and defect detection that demand high precision while tolerating fluctuations in the environment and the objects being analysed, this kind of machine vision is therefore ideal.
Manufacturers can automate tasks long thought to be beyond the scope of conventional automation by including an additional dimension into picture analysis while still utilising all the characteristics and advantages of 2D vision.
Sl no | Topic |
1 | Market Segmentation |
2 | Scope of the report |
3 | Abbreviations |
4 | Research Methodology |
5 | Executive Summary |
6 | Introduction |
7 | Insights from Industry stakeholders |
8 | Cost breakdown of Product by sub-components and average profit margin |
9 | Disruptive innovation in the Industry |
10 | Technology trends in the Industry |
11 | Consumer trends in the industry |
12 | Recent Production Milestones |
13 | Component Manufacturing in US, EU and China |
14 | COVID-19 impact on overall market |
15 | COVID-19 impact on Production of components |
16 | COVID-19 impact on Point of sale |
17 | Market Segmentation, Dynamics and Forecast by Geography, 2024-2030 |
18 | Market Segmentation, Dynamics and Forecast by Product Type, 2024-2030 |
19 | Market Segmentation, Dynamics and Forecast by Application, 2024-2030 |
20 | Market Segmentation, Dynamics and Forecast by End use, 2024-2030 |
21 | Product installation rate by OEM, 2023 |
22 | Incline/Decline in Average B-2-B selling price in past 5 years |
23 | Competition from substitute products |
24 | Gross margin and average profitability of suppliers |
25 | New product development in past 12 months |
26 | M&A in past 12 months |
27 | Growth strategy of leading players |
28 | Market share of vendors, 2023 |
29 | Company Profiles |
30 | Unmet needs and opportunity for new suppliers |
31 | Conclusion |
32 | Appendix |