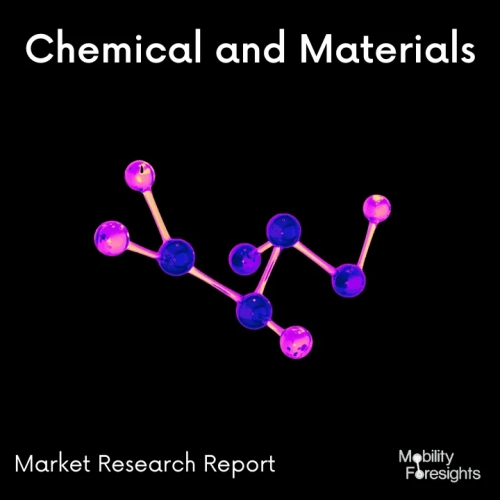
- Get in Touch with Us
Last Updated: Jul 14, 2025 | Study Period: 2025-2031
Acrylic polymers are high-performance synthetic resins derived from acrylic and methacrylic acid used in coatings, adhesives, textiles, and construction applications.
These polymers exhibit excellent weatherability, transparency, water resistance, and adhesion, making them highly versatile across end-use industries.
Growing demand for water-based and low-VOC formulations in paints, coatings, and sealants is driving the rapid adoption of acrylic polymers as a sustainable alternative.
Technological advancements in self-healing, UV-curable, and high-solid acrylics are opening new applications in automotive, electronics, and biomedical industries.
Construction and packaging sectors are the two largest consumers of acrylic polymers due to high usage in sealants, waterproofing systems, and barrier coatings.
Asia-Pacific dominates the global market with China and India as key manufacturing hubs, owing to strong demand from paints & coatings, plastics, and textile sectors.
Increased use of acrylic binders in nonwoven hygiene products and pressure-sensitive adhesives (PSAs) is expanding the application base.
Major companies include BASF SE, Arkema, Dow Inc., Mitsubishi Chemical, and Sika AG, among others.
R&D is focused on bio-based acrylic polymers, high-performance emulsions, and thermoplastic blends for specialized end-use cases.
Market is seeing a shift from solvent-based to aqueous acrylic systems due to increasing environmental regulations globally.
The acrylic polymer market has evolved as a cornerstone of modern material science, supplying key inputs to a broad range of industries such as construction, automotive, packaging, personal care, and textiles. These polymers are characterized by their tunable properties—clarity, durability, chemical resistance, and elasticity—which make them suitable for both structural and decorative applications.
They are produced through free-radical polymerization of acrylic monomers and can be tailored to form emulsions, resins, and solutions depending on the use-case. In coatings, acrylic polymers enhance surface appearance, UV resistance, and durability. In construction, they are used in cement modifiers, waterproofing membranes, and elastomeric coatings. In adhesives, acrylic polymers provide excellent bonding on diverse substrates with good peel and tack strength.
As global industries move toward sustainable and low-emission materials, water-based acrylic emulsions are increasingly preferred over solvent-based formulations. Innovation in nanostructured acrylics and hybrid polymers is also enabling high-performance applications in electronics, packaging, and biomedicine.
The global acrylic polymer market was valued at USD 19.4 billion in 2024 and is projected to reach USD 31.7 billion by 2031, growing at a CAGR of 7.2% during the forecast period.
The growth is driven by strong demand in construction, automotive, textiles, and personal care, where acrylic polymers offer eco-friendly, durable, and cost-effective solutions. Government regulations phasing out VOCs and mandating the use of green building materials further accelerate the adoption of waterborne acrylic emulsions. Expansion of manufacturing capacities in emerging economies and technological advancements in emulsion polymerization are also supporting market growth.
Furthermore, the rise in disposable hygiene products, flexible packaging, and electronics coatings is opening new frontiers for specialty-grade acrylics. Regions such as Asia-Pacific and Latin America are poised for high-volume consumption, while North America and Europe focus on specialty applications and sustainability.
Over the next decade, the acrylic polymer market will continue to benefit from the global shift toward sustainability, lightweight materials, and functional coatings. Acrylics will increasingly replace conventional resins in architectural paints, automotive OEM coatings, sealants, and nonwoven adhesives due to their low environmental impact and tunable mechanical properties.
Key trends expected to shape the market include the rise of bio-based acrylic monomers, the development of multi-functional polymers (e.g., anti-microbial, self-cleaning), and integration of smart polymers in packaging and medical sectors. As digital printing and 3D printing grow, demand for tailored acrylic formulations will rise to meet specific performance and curing needs.
Advancements in controlled radical polymerization techniques such as RAFT and ATRP will enable new grades of high-performance acrylics for microelectronics, wearable devices, and aerospace coatings. Market participants will also increasingly focus on backward integration to ensure raw material security and cost optimization.
Growth in Waterborne Acrylic Emulsions:
Due to rising environmental regulations on solvent-based coatings, waterborne acrylic emulsions are witnessing increased adoption. These emulsions offer excellent film-forming capabilities and low odor, making them ideal for indoor applications such as architectural coatings, DIY paints, and furniture lacquers.
Bio-Based Acrylic Polymers:
Manufacturers are investing in bio-based feedstocks such as bio-acrylic acid and glycerin to produce sustainable acrylic polymers. These bio-acrylics reduce dependency on petrochemicals and are gaining traction in eco-certified adhesives, paints, and hygiene products.
Use in Flexible Packaging and Labeling:
Acrylic polymers are widely used in pressure-sensitive adhesives (PSAs) for labels, tapes, and packaging films. With the growth of e-commerce and food delivery, demand for flexible packaging has surged, boosting usage of acrylic-based adhesives and coatings that offer clarity, bond strength, and recyclability.
Smart and Functional Acrylics:
Emerging applications in electronics and healthcare are driving the need for smart acrylic polymers with antimicrobial, anti-fog, UV-blocking, and conductive properties. Such polymers are being integrated into wearable sensors, medical films, and advanced coatings for touchscreens and flexible devices.
Rising Demand in Construction and Infrastructure:
Acrylic polymers are used in sealants, waterproof coatings, exterior paints, and cement additives. With increasing infrastructure projects and urbanization, especially in developing economies, the construction sector is a major growth driver for the acrylic polymer market.
Boom in Hygiene and Personal Care Products:
The nonwoven industry is a significant consumer of acrylic binders, used in disposable hygiene products such as diapers, wipes, and feminine care. The growing population, urban lifestyle, and rising health awareness are boosting demand for these products globally.
Automotive and Transportation Sector Growth:
Acrylics are used in automotive coatings, plastic parts, and adhesives due to their UV resistance and durability. As vehicle production grows and consumers demand higher aesthetic and performance standards, acrylic polymers are increasingly integrated into OEM and aftermarket applications.
Shift to Low-VOC and Sustainable Materials:
Environmental concerns and regulations (e.g., REACH, EPA) are encouraging industries to switch to low-emission materials. Acrylic polymers, particularly water-based variants, are gaining ground in paints, sealants, and adhesives as safer alternatives to solvent-based products.
Volatility in Raw Material Prices:
Acrylic polymers rely heavily on petrochemical derivatives such as acrylates and methacrylates. Fluctuations in crude oil prices and raw material availability can affect production costs and pricing strategies, particularly for high-volume applications like coatings.
Competition from Alternative Polymers:
Polyurethanes, vinyl acetate-based polymers, and epoxy resins offer overlapping functionality in some end-uses, creating competitive pressure. In adhesives and coatings, customers often compare cost-performance ratios, which can challenge acrylic polymer adoption in price-sensitive markets.
Environmental Concerns for Solvent-Based Acrylics:
While waterborne systems are growing, solvent-based acrylic polymers still dominate in certain applications. Their high VOC emissions pose environmental and regulatory challenges, necessitating additional compliance measures or reformulation costs for manufacturers.
Complex Manufacturing and Processing Costs:
Producing high-performance or specialty acrylic polymers requires sophisticated emulsion or solution polymerization setups. The high capital and technical requirements can limit the entry of new players and constrain cost-effective production in low-volume niche segments.
Waterborne Acrylic Polymers
Solvent-Based Acrylic Polymers
Specialty Acrylic Polymers (UV-curable, Thermoplastic, Bio-based)
Emulsions
Resins
Beads and Powders
Solutions
Paints and Coatings
Adhesives and Sealants
Construction Additives
Nonwoven Hygiene Products
Textiles and Leather Finishing
Printing Inks and Packaging
Medical and Biomedical Applications
Construction
Automotive and Transportation
Packaging
Personal Care and Hygiene
Electronics and Electricals
Textiles and Apparel
Healthcare
North America
Europe
Asia-Pacific
Latin America
Middle East & Africa
BASF SE
Dow Inc.
Arkema Group
Mitsubishi Chemical Corporation
Sika AG
H.B. Fuller
Lubrizol Corporation
Asian Paints
DIC Corporation
Ashland Global Holdings
BASF SE partnered with OMV to develop bio-acrylic acid production pathways, advancing the commercialization of renewable acrylic polymers for packaging and hygiene.
Dow Inc. collaborated with Johnson Controls to develop low-VOC acrylic emulsions for use in green-certified construction products.
Arkema launched a joint R&D initiative with Hexcel Corporation to develop high-strength acrylic composites for aerospace applications.
Sika AG acquired MBCC Group’s polymer dispersion unit, expanding its portfolio of high-performance acrylic systems for the global construction industry.
H.B. Fuller entered into a strategic agreement with Covestro for the supply of climate-neutral raw materials for water-based acrylic adhesives.
How many Acrylic Polymers are manufactured per annum globally? Who are the sub-component suppliers in different regions?
Cost Breakdown of a Global Acrylic Polymer and Key Vendor Selection Criteria
Where is the Acrylic Polymer manufactured? What is the average margin per unit?
Market share of Global Acrylic Polymer market manufacturers and their upcoming products
Cost advantage for OEMs who manufacture Global Acrylic Polymer in-house
Key predictions for next 5 years in the Global Acrylic Polymer market
Average B2B Acrylic Polymer market price in all segments
Latest trends in the Acrylic Polymer market, by every market segment
The market size (both volume and value) of the Acrylic Polymer market in 2025–2031 and every year in between
Production breakup of the Acrylic Polymer market, by suppliers and their OEM relationship
Sl no | Topic |
1 | Market Segmentation |
2 | Scope of the report |
3 | Research Methodology |
4 | Executive summary |
5 | Key Predictions of Acrylic Polymer Market |
6 | Avg B2B price of Acrylic Polymer Market |
7 | Major Drivers For Acrylic Polymer Market |
8 | Global Acrylic Polymer Market Production Footprint - 2024 |
9 | Technology Developments In Acrylic Polymer Market |
10 | New Product Development In Acrylic Polymer Market |
11 | Research focus areas on new Acrylic Polymer |
12 | Key Trends in the Acrylic Polymer Market |
13 | Major changes expected in Acrylic Polymer Market |
14 | Incentives by the government for Acrylic Polymer Market |
15 | Private investements and their impact on Acrylic Polymer Market |
16 | Market Size, Dynamics And Forecast, By Type, 2025-2031 |
17 | Market Size, Dynamics And Forecast, By Output, 2025-2031 |
18 | Market Size, Dynamics And Forecast, By End User, 2025-2031 |
19 | Competitive Landscape Of Acrylic Polymer Market |
20 | Mergers and Acquisitions |
21 | Competitive Landscape |
22 | Growth strategy of leading players |
23 | Market share of vendors, 2024 |
24 | Company Profiles |
25 | Unmet needs and opportunities for new suppliers |
26 | Conclusion |