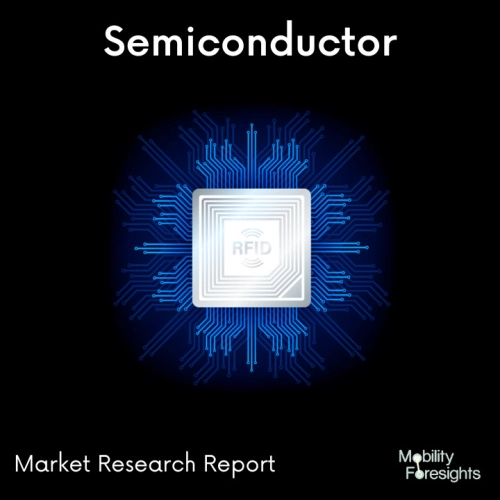
- Get in Touch with Us
Last Updated: Apr 25, 2025 | Study Period: 2024-2030
Three monomersâacrylonitrile, styrene, and acrylic esterâare combined to form the thermoplastic polymer known as Acrylonitrile Styrene Acrylate (ASA). A copolymer called ASA has special qualities like impact resistance, weather resistance, UV stability, and dimensional stability.
For its outstanding performance in outdoor settings and its resilience to weathering, ASA is highly appreciated. It is a fantastic option for applications requiring long-term durability in outdoor environments because it is specially designed to endure exposure to sunshine, rain, and environmental conditions. ASA keeps its color stability, mechanical qualities, and surface quality even after extended exposure to UV radiation and severe weather.
The exceptional resilience of ASA to UV damage is one of its main benefits. When exposed to sunshine, it can successfully withstand the damaging effects of UV radiation and maintain its mechanical integrity. Due to its lengthy performance and color retention, ASA is a suitable material for outdoor applications.
Additionally, ASA exhibits substantial impact resistance, giving end products robustness and durability. It is suitable for applications that call for strength and dependability since it can bear moderate blows without cracking or breaking. This quality is especially useful in the automotive sector, where ASA is frequently used to make exterior parts including bumpers, grilles, and mirror housings.
Additionally, ASA demonstrates outstanding dimensional stability. It has a low coefficient of thermal expansion, which means that changes in temperature have little effect on how its dimensions change. Due to this property, it is particularly suited for applications needing precise dimensions and tight tolerances, such as electrical enclosures or components requiring precision fit and assembly.
Different plastic production processes, such as injection molding, extrusion, and thermoforming, can be used to process ASA. It has advantageous flow characteristics that make it easier to create elaborate patterns and complex structures. Additionally, the production technique for ASA makes it simple to color it, negating the need for additional painting or coating steps.
Applications for ASA can be found in numerous sectors. It is extensively used in the fabrication of external parts for automobiles, as was already mentioned. Due to its weather ability and UV resistance, ASA is well-suited for outdoor athletic and recreational equipment, consumer goods, electrical enclosures, and even building materials.
Acrylonitrile Styrene Acrylate (ASA), a thermoplastic polymer composed of acrylonitrile, styrene, and acrylic ester monomers, can be summarized as follows. It offers great dimensional stability, weatherability, UV resistance, and impact resistance.
In outdoor applications, where long-lasting durability and color retention are crucial, ASA is widely used. Due to its characteristics, it is excellent for a variety of items that require resistance to environmental elements, including automotive components, outdoor recreational equipment, electrical enclosures, and more.
The Global Acrylonitrile Styrene Acrylate Market accounted for $XX Billion in 2023 and is anticipated to reach $XX Billion by 2030, registering a CAGR of XX% from 2024 to 2030.
New gray and T max translucent 3D printing materials have been introduced by the Italian company We erg, which also offers CNC and 3D printing services. The resins are made to have the same mechanical properties as ABS materials, and they can be used in place of ABS to make prototypes, parts, and functioning parts for the mechanical and automotive industries.
Customers can upload 3D files to We erg's online 3D printing service, which the company subsequently manufactures using its CNC machines and 3D printers. Additionally, We erg offers clients advising, delivery, and quote services, as well as complete Non-Disclosure Agreement (NDA) security for any CAD files provided.
Three resin formulations are offered for the newly added materials: classic, performance, and top mechanical. Based on the amount of stress that the molded component will experience, customers can thus select the resin that best meets their processing needs.
We erg's new resins enable solid, high-surface quality 3D printing of items up to 58x120x159 mm with 0.5 mm resolution. As a result, the materials have potential uses in the mechanical and automotive industries as well as in the development of beautiful models.
The grey color of the resin, which resembles ABS, makes it possible to apply additional finishes like paint. Grey surfaces also help to prevent the product from turning yellow, which can occasionally happen with black and white surfaces. The glossy and satin varieties of T max, on the other hand, make it the perfect material for creating prototypes or parts that must be seen in the finished product.
The two resins, which join the company's current collection of Nylon PA12 materials, were created by We erg using its unique 4KSPERTM technology, according to Riga Monti.
1 | Market Segmentation |
2 | Scope of the report |
3 | Abbreviations |
4 | Research Methodology |
5 | Executive Summary |
6 | Introduction |
7 | Insights from Industry stakeholders |
8 | Cost breakdown of Product by sub-components and average profit margin |
9 | Disruptive innovation in the Industry |
10 | Technology trends in the Industry |
11 | Consumer trends in the industry |
12 | Recent Production Milestones |
13 | Component Manufacturing in US, EU and China |
14 | COVID-19 impact on overall market |
15 | COVID-19 impact on Production of components |
16 | COVID-19 impact on Point of sale |
17 | Market Segmentation, Dynamics and Forecast by Geography, 2024-2030 |
18 | Market Segmentation, Dynamics and Forecast by Product Type, 2024-2030 |
19 | Market Segmentation, Dynamics and Forecast by Application, 2024-2030 |
20 | Market Segmentation, Dynamics and Forecast by End use, 2024-2030 |
21 | Product installation rate by OEM, 2023 |
22 | Incline/Decline in Average B-2-B selling price in past 5 years |
23 | Competition from substitute products |
24 | Gross margin and average profitability of suppliers |
25 | New product development in past 12 months |
26 | M&A in past 12 months |
27 | Growth strategy of leading players |
28 | Market share of vendors, 2023 |
29 | Company Profiles |
30 | Unmet needs and opportunity for new suppliers |
31 | Conclusion |
32 | Appendix |