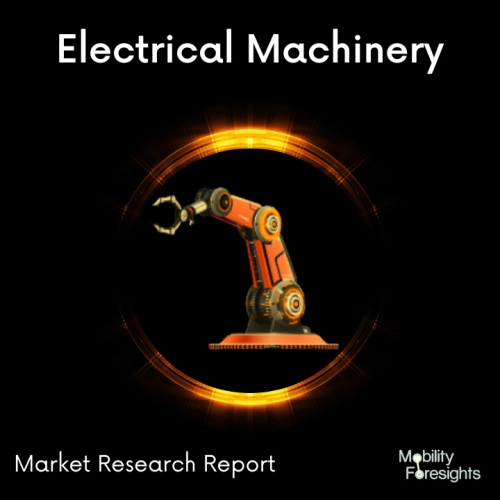
- Get in Touch with Us
Last Updated: Apr 26, 2025 | Study Period: 2023-2030
The Active Welding System is a revolutionary welding technology that provides an efficient and safe welding environment. It is designed to maximize precision and speed while reducing the risk of weld defects.
The system utilizes a combination of advanced welding techniques, automated welding process control, and real-time monitoring to ensure the highest quality welds.
The system includes robot-assisted welding, automated welding process control, and real-time monitoring and data logging. The process is monitored in real-time to provide feedback on weld quality and accuracy.
The robot-assisted welding system uses a robotic arm to guide the welding torch and adjust welding parameters, such as speed, travel speed, and arc length, in real-time. Automated process control ensures a consistent, repeatable weld quality and also prevents operator errors.
The system is designed to reduce the cost of welding operations while improving the quality of welds. The system is capable of welding a wide range of materials without the need for manual intervention. Additionally, the system is designed to reduce fumes, smoke, and other environmental hazards associated with welding.
Active Welding System is a revolutionary technology that has the potential to revolutionize the welding industry by providing safer, more efficient, and more cost-effective welding operations. The system is designed to reduce costs, improve weld quality, and reduce environmental hazards associated with welding.
The Global Active Welding System market accounted for $XX Billion in 2022 and is anticipated to reach $XX Billion by 2030, registering a CAGR of XX% from 2023 to 2030.
TRUMPF recently launched a new welding system, the TruLaser Weld 5000. This system offers users the ability to weld in a wide range of materials, including aluminum, stainless steel, and titanium.
The system has been designed to ensure maximum accuracy and repeatability, and it offers an advanced process monitoring system to ensure that the welds are of the highest quality. The system is also equipped with an intuitive user interface, allowing users to easily program and control the welding process.
Additionally, TRUMPF has announced the development of its new TruLaser Cell 3000. This welding system isdesigned to increase productivity and reduce costs, as it uses automated processes to improve efficiencyand reduce material waste.
The system is equipped with multiple laser sources, allowing for faster welding speeds and the ability to weld multiple materials in a single pass. The system is also equipped with an advanced monitoring system that can detect potential problems and alert operators when changes are needed to maintain quality standards.
Kemppi recently announced the launch of its new ArcMaster welding system. This system offers users the ability to weld in a wide range of materials, including aluminum, stainless steel, and titanium.
The system is designed to ensure maximum accuracy and repeatability, and it is equipped with an intuitive user interface that allows users to easily program and control the welding process.
The system is also equipped with an advanced process monitoring system that can detect potential problems and alert operators when changes are needed to maintain quality standards.
Sl no | Topic |
1 | Market Segmentation |
2 | Scope of the report |
3 | Abbreviations |
4 | Research Methodology |
5 | Executive Summary |
6 | Introduction |
7 | Insights from Industry stakeholders |
8 | Cost breakdown of Product by sub-components and average profit margin |
9 | Disruptive innovation in the Industry |
10 | Technology trends in the Industry |
11 | Consumer trends in the industry |
12 | Recent Production Milestones |
13 | Component Manufacturing in US, EU and China |
14 | COVID-19 impact on overall market |
15 | COVID-19 impact on Production of components |
16 | COVID-19 impact on Point of sale |
17 | Market Segmentation, Dynamics and Forecast by Geography, 2023-2030 |
18 | Market Segmentation, Dynamics and Forecast by Product Type, 2023-2030 |
19 | Market Segmentation, Dynamics and Forecast by Application, 2023-2030 |
20 | Market Segmentation, Dynamics and Forecast by End use, 2023-2030 |
21 | Product installation rate by OEM, 2023 |
22 | Incline/Decline in Average B-2-B selling price in past 5 years |
23 | Competition from substitute products |
24 | Gross margin and average profitability of suppliers |
25 | New product development in past 12 months |
26 | M&A in past 12 months |
27 | Growth strategy of leading players |
28 | Market share of vendors, 2023 |
29 | Company Profiles |
30 | Unmet needs and opportunity for new suppliers |
31 | Conclusion |
32 | Appendix |