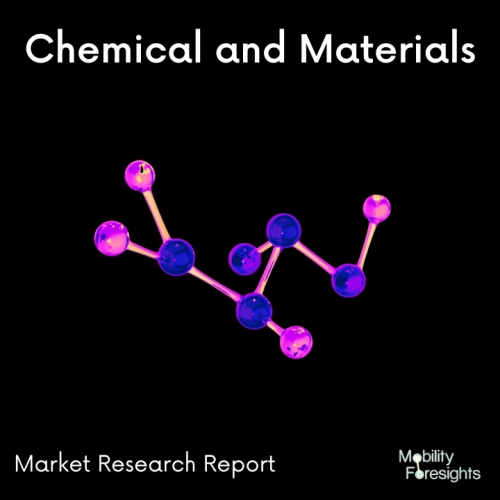
- Get in Touch with Us
Last Updated: Apr 25, 2025 | Study Period: 2024-2030
Aluminium alloy is the most commonly used in aerospace development. The alloy has a high yield strength and is a high-grade alloy with excellent fatigue resistance. It is commonly used in sheet form for the wings and fuselage.
This is a non-heat treatable alloy grade. It has the highest strength and is also highly ductile. It can be formed into a variety of shapes and is highly corrosion resistant, making it an ideal addition for a variety of aerospace applications.
Especially with the recently developed aluminium-lithium alloys that could decrease aircraft weight and increase performance, the demand for aluminium in the aerospace industry will most likely double in the next few years.
The Global Aerospace-grade aluminium market accounted for $XX Billion in 2021 and is anticipated to reach $XX Billion by 2030, registering a CAGR of XX% from 2024 to 2030.
Aerospace-grade aluminium and eco-friendly materials are used in Apple's iPhone 14 series. The latest generation of the new iPhone14 was produced using eco-friendly materials, according to the American global technology giant Apple Inc.
The aerospace-grade aluminium used to make the iPhone 14 and iPhone 14 Plus is strong and sleek, and it comes in five different colours. The advantage of this smartphone, however, is that it was constructed using 100% recycled tungsten metal for the Taptic Engine and 100% recycled rare earth elements for all magnets, including those used in MagSafe, to safeguard the environment from the negative impacts of various metals in products.
Using haptic technology, the Taptic Engine replicates actions like clicks on a fixed touch screen to give users physical interaction. The iPhone 14 and iPhone 14 Plus also include a tough Ceramic Shield front shell, which is exclusive to iPhone and is more durable than any other smartphone glass. To protect them from common spills and accidents, they also have dust and water resistance.
The hybrid technology developer and producer Infinity X1 has introduced their newest flashlights made of aviation-grade aluminium. High lumen counts, three illumination modes, dual power options, IPx4 water resistance, and 1-metre drop protection are all features of the Infinity X1 LED Hybrid Powered flashlight series.
There are four different lumen strengths for the flashlight as well. It includes two power sources: a USB-A connector for backup power for other devices and a rechargeable battery core with a built-in USB-A cable for easy charging.
The most prevalent aluminium alloy used in the aircraft industry is 7075, which mostly consists of zinc as an alloying element. It is crucial, comparable to many steels, and has good fatigue strength, medium machinability, and a lower corrosion resistance than many other aluminium alloys.
The hybrid-powered flashlight series was created by Infinity X1 to help users switch to rechargeable technology while providing a convenient, adaptable dry-cell battery option when recharging is not an option to decrease the environmental impact of technology.
SLM Solutions and Elementum 3D have partnered to create aerospace grade 7050 and 7075 as well as premium aluminium alloys 2024 and 6061. As of right now, SLM has announced its most recent acquisition of the NXG XII 600E coupled with a flexible manufacturing solution to address the challenges the AM sector is now experiencing due to building envelope restrictions.
Despite everything, the biggest obstacle to creating precision-engineered AM components is the scarcity of suitable materials. A significant demand for AM goods comes from the aviation sector, but sadly, high-performing, crack-resistant materials are hard to come by. They must order flawless components since high-precision businesses would not accept damaged parts.
Once more, the aircraft industry needs high-strength, adaptable, and corrosion-resistant materials to survive. Because it is not very resilient, pure aluminium cannot be used for such components, despite the fact that it plays a crucial role in lifting the particular sector. But by combining powerful elements in the compound, aluminium alloys can be designed to become stiff.
To mark their partnership, Elementum 3D purchased the outstanding SLM machine NXG XII 600 to produce cutting-edge technologies and materials. Their plan was to develop Elementum 3D materials that could be used with SLM equipment, primarily the NXG XII 600. Both businesses stand to gain from this coalition's potential to generate superior aluminium alloys or raw materials compatible with SLM Solutions' machines.
Sl no | Topic |
1 | Market Segmentation |
2 | Scope of the report |
3 | Abbreviations |
4 | Research Methodology |
5 | Executive Summary |
6 | Introduction |
7 | Insights from Industry stakeholders |
8 | Cost breakdown of Product by sub-components and average profit margin |
9 | Disruptive innovation in the Industry |
10 | Technology trends in the Industry |
11 | Consumer trends in the industry |
12 | Recent Production Milestones |
13 | Component Manufacturing in US, EU and China |
14 | COVID-19 impact on overall market |
15 | COVID-19 impact on Production of components |
16 | COVID-19 impact on Point of sale |
17 | Market Segmentation, Dynamics and Forecast by Geography, 2022-2030 |
18 | Market Segmentation, Dynamics and Forecast by Product Type, 2022-2030 |
19 | Market Segmentation, Dynamics and Forecast by Application, 2022-2030 |
20 | Market Segmentation, Dynamics and Forecast by End use, 2022-2030 |
21 | Product installation rate by OEM, 2022 |
22 | Incline/Decline in Average B-2-B selling price in past 5 years |
23 | Competition from substitute products |
24 | Gross margin and average profitability of suppliers |
25 | New product development in past 12 months |
26 | M&A in past 12 months |
27 | Growth strategy of leading players |
28 | Market share of vendors, 2022 |
29 | Company Profiles |
30 | Unmet needs and opportunity for new suppliers |
31 | Conclusion |
32 | Appendix |