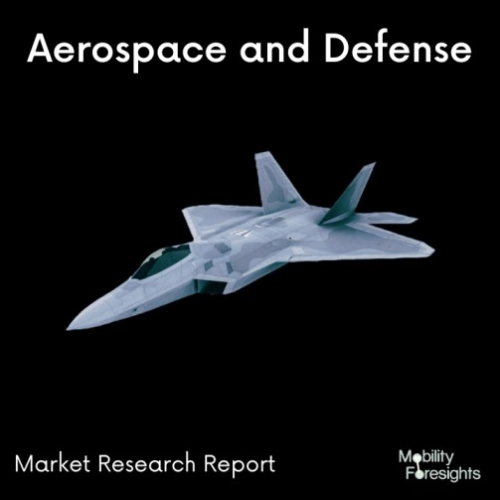
- Get in Touch with Us
Last Updated: Apr 25, 2025 | Study Period: 2024-2030
The Global Aerospace Superalloys Market is expected to take off in the coming years, driven by the rising demand for high-performance aircraft. These superalloys boast exceptional strength, resist extreme temperatures, and combat corrosion, making them vital for turbine blades, engine parts, and other critical components.
This growth is fueled by several factors. Firstly, the need for lightweight yet durable materials in aircraft manufacturing is paramount. Superalloys fit the bill perfectly, enabling the creation of fuel-efficient planes. Secondly, the increasing focus on next-generation aircraft with improved efficiency and performance necessitates these advanced materials.
The Asia-Pacific region is currently leading the pack, with China and Japan being the major consumers. This dominance is due to rapid industrialization and a growing aerospace sector in these countries. Additionally, the shift in global aerospace production towards this region further strengthens its market position.
However, the path isn't without hurdles. Fluctuations in raw material prices can pose a challenge for manufacturers. Moreover, extended periods of low fuel costs might incentivize airlines to explore alternative materials to keep operational expenses down.
Despite these obstacles, the long-term outlook for the market remains positive. The aerospace and defense industries are constantly striving to enhance aircraft capabilities and efficiency. This relentless pursuit of innovation will likely translate into a growing demand for superalloys.
Furthermore, the aging fleet in developed nations demands replacements. These replacements will likely be technologically advanced and fuel-efficient, further propelling the need for superalloys.
Looking ahead, advancements in avionics and component design are expected to create a ripple effect. As these technologies evolve, the demand for superalloys is poised to surge as well.
In conclusion, the global aerospace superalloys market presents an exciting prospect. With the aviation industry continuously pushing boundaries, superalloys are well-positioned to play a critical role in the future of flight.
Aerospace superalloys are a specialized class of high-performance materials designed to withstand extreme conditions prevalent in aerospace applications, particularly in aircraft engines and structural components. These alloys are engineered to exhibit exceptional strength, resistance to high temperatures, and superior mechanical properties, making them indispensable for ensuring the reliability and performance of critical aerospace systems. Common types of aerospace superalloys include nickel-based and cobalt-based alloys, each tailored to specific application requirements.
The benefits of aerospace superalloys are manifold. They enable the construction of lightweight yet durable components, contributing to fuel efficiency and overall performance enhancements in aircraft. Additionally, their excellent resistance to corrosion and oxidation ensures prolonged service life and operational reliability in harsh operating environments. Moreover, aerospace superalloys facilitate the design of advanced engine architectures capable of withstanding extreme temperatures and pressures, leading to enhanced thrust and efficiency.
However, the utilization of aerospace superalloys also entails certain risks and challenges. One primary concern is the high cost associated with the manufacturing and processing of these specialized materials, which can significantly impact overall project budgets. Furthermore, the complex metallurgical compositions and manufacturing processes involved in producing aerospace superalloys necessitate stringent quality control measures to ensure consistency and reliability.
Additionally, as aerospace technologies continue to evolve, the industry faces ongoing challenges in developing new superalloys that meet ever-increasing performance demands while adhering to regulatory requirements and environmental standards.
The Global Aerospace Superalloys Market accounted for $XX Billion in 2023 and is anticipated to reach $XX Billion by 2030, registering a CAGR of XX% from 2024 to 2030.
Haynes International, Inc. introduced the Haynes® 282® alloy. This nickel-based superalloy exhibits exceptional strength, creep resistance, and thermal stability, making it well-suited for demanding aerospace applications. With a nominal composition of nickel, chromium, cobalt, and other alloying elements, Haynes® 282® offers superior mechanical properties at elevated temperatures, ensuring reliable performance in critical engine components and structural parts.
Precision Castparts Corp. (PCC) introduced the PCC SuperAlloy Division's CMSX® series. CMSX® superalloys are cobalt-based and specifically engineered for high-temperature applications, such as turbine blades and vanes in aircraft engines. With exceptional creep resistance, thermal stability, and mechanical strength, CMSX® alloys deliver outstanding performance in extreme operating conditions, contributing to enhanced engine efficiency and reliability.
Special Metals Corporation introduced the Nimonic® 263, known for its exceptional strength, corrosion resistance, and thermal stability at elevated temperatures. Nimonic® 263 is widely utilized in critical components of aircraft engines, such as turbine blades and discs, where it demonstrates excellent creep and fatigue resistance, ensuring long-term reliability and operational efficiency.
SL NO | TOC |
1 | Market Segmentation |
2 | Scope of the Report |
3 | Research Methodology |
4 | Executive Summary |
5 | Introduction |
6 | Average B-2-B Selling Price in Past 5 Years |
7 | Insights from Industry Stakeholders |
8 | Cost Breakdown of Product Components and Average Profit Margin |
9 | Disruptive Innovation in the Industry |
10 | Technological Innovations in Global Aerospace Superalloys Market 2024-2030 |
11 | Advanced Metallurgical Techniques |
12 | Additive Manufacturing Innovations |
13 | Sustainable Alloy Development |
14 | Computational Modeling and Simulation |
15 | Digitalization and Smart Manufacturing |
16 | Multi-Material Integration Strategies |
17 | High-Temperature Materials Research |
18 | Nanotechnology Applications in Superalloys |
19 | Sensor and Monitoring Technologies |
20 | Advanced Coating and Surface Treatments |
21 | New Product Development in the Past 12 Months |
22 | Market Size, Dynamics, and Forecast by Geography (2024-2030) |
23 | Market Size, Dynamics, and Forecast by Alloy Type (2024-2030) |
24 | Market Size, Dynamics, and Forecast by Application (2024-2030) |
25 | Market Size, Dynamics, and Forecast by End-User (2024-2030) |
26 | Competitive Landscape and Market Share Analysis |
27 | Growth Strategy of Leading Players |
28 | Market Share of Vendors (2023) |
29 | Company Profiles |
30 | Unmet Needs and Opportunities for New Suppliers |
31 | Conclusion |