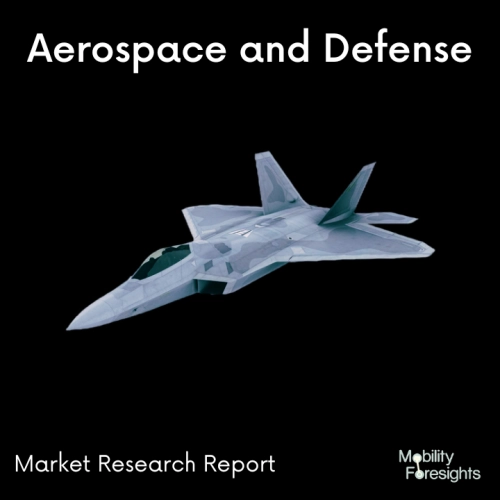
- Get in Touch with Us
Last Updated: Apr 25, 2025 | Study Period: 2023-2030
The aircraft's cockpit and cabin are cooled both on the ground and while in flight thanks to the vapour cycle technology. An electric motor operates the compressor at a consistent speed and capacity.
The warm low pressure gas is compressed by the compressor to create a hot high pressure gas. The heated high pressure gas is then transported through the condenser, which creates high pressure subcooled liquid refrigerant by rejecting heat to the atmosphere.
The moisture in this liquid is subsequently removed by a desiccant as it passes through a receiver/dryer. In low ambient temperatures, the receiver/dryer also serves as a reservoir for the liquid refrigerant.
The forward and aft thermostatic expansion valves are where the high pressure subcooled liquid is expanded into a low pressure, low temperature liquid/vapour mixture.
The thermostatic expansion valve controls the refrigerant flow necessary for various operating situations by means of a thermal bulb located on the low side's horizontal line.
Then, as the mixture of liquid and vapour passes through the evaporators, cabin air heat is absorbed. A blower positioned on the evaporator blows air over the refrigeration coil.
The air heats the liquid refrigerant, turning it into a superheated vapour. The low pressure superheated vapour then makes its way back to the compressor to complete the cycle.
A binary pressure switch is used by the system to carry out two tasks. In the first place, it serves as a low pressure safety switch to stop system operation in the case of low refrigerant pressure or at low ambient temperatures.
The Global Aerospace Vapour Cycle System market accountedfor $XX Billion in 2021 and is anticipated to reach $XX Billion by 2030, registering a CAGR of XX% from 2022 to 2030.
AMETEK Aircontrol Technologies uses its knowledge and experience to the design and production of environmental control equipment and systems for aerospace applications in addition to its considerable engagement in the application of systems for military vehicles.
The company has a track record of success in the creation of Vapour Cycle Systems (VCS) for environmental management and equipment cooling applications.
These systems must be sized and packed to fit the customers' equipment because they are made for particular cooling requirements.
We have created a number of vapour cycle systems (described in more detail below) for usage in a variety of aerospace applications.
These systems range in size and cooling capacity from our tiny VCS for the cooling of the F35 pilot to a much bigger radar and crew VCS for the Sea King Helicopter.
For designers of urban air mobility (UAM) and electric aircraft, Honeywell Aerospace has announced a lightweight, low-maintenance cooling system, and has selected the Deviation Alice as the launch platform.
In order to prepare for the prototype's first flight later this year, the company's micro vapour cycle system (MicroVCS) will be fitted into the nine-seat, all-electric commuter aircraft.
Aircraft in the upcoming UAM and electric air taxi categories will need to be lightweight and minimise maintenance downtime, according to Honeywell Aerospace's for air and thermal systems.
Sl no | Topic |
1 | Market Segmentation |
2 | Scope of the report |
3 | Abbreviations |
4 | Research Methodology |
5 | Executive Summary |
6 | Introduction |
7 | Insights from Industry stakeholders |
8 | Cost breakdown of Product by sub-components and average profit margin |
9 | Disruptive innovation in the Industry |
10 | Technology trends in the Industry |
11 | Consumer trends in the industry |
12 | Recent Production Milestones |
13 | Component Manufacturing in US, EU and China |
14 | COVID-19 impact on overall market |
15 | COVID-19 impact on Production of components |
16 | COVID-19 impact on Point of sale |
17 | Market Segmentation, Dynamics and Forecast by Geography, 2023-2030 |
18 | Market Segmentation, Dynamics and Forecast by Product Type, 2023-2030 |
19 | Market Segmentation, Dynamics and Forecast by Application, 2023-2030 |
20 | Market Segmentation, Dynamics and Forecast by End use, 2023-2030 |
21 | Product installation rate by OEM, 2023 |
22 | Incline/Decline in Average B-2-B selling price in past 5 years |
23 | Competition from substitute products |
24 | Gross margin and average profitability of suppliers |
25 | New product development in past 12 months |
26 | M&A in past 12 months |
27 | Growth strategy of leading players |
28 | Market share of vendors, 2023 |
29 | Company Profiles |
30 | Unmet needs and opportunity for new suppliers |
31 | Conclusion |
32 | Appendix |