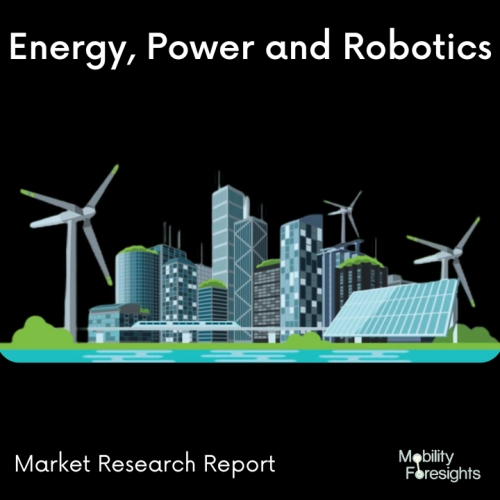
- Get in Touch with Us
Last Updated: Apr 25, 2025 | Study Period: 2023-2030
3D BinPick is a hardware/software solution for swiftly recognising and picking pieces that are randomly displayed in a bin.Bin picking is an automation method that detects, picks, and conveys chaotically arranged things using 3D sensors and robotics.
The sensor, which is installed stationary above the container, initially generates a point cloud using structured light. This results in the creation of a three-dimensional representation of the surface.Picker Robots are mobile equipment meant to retrieve and transport merchandise in a warehouse independently.
The robots are guided by AI-powered software that determines the most effective routes for picking, replenishing, returning, and counting products.
The Global AI 3D Bin Picking System market accounted for $XX Billion in 2022 and is anticipated to reach $XX Billion by 2030, registering a CAGR of XX% from 2023 to 2030.
KUKA and Roboception Bring a Smart Bin Picking System to Market According to KUKA, its SmartBinPicking software and associated components are accessible as a vision toolkit package. While a human can reach into a bin and pick up a screw without hitting an arm on the bin's edge, a robot requires precise motion planning.
KUKA AG teamed with Roboception GmbH last week to create and provide a vision tool kit that they claim is simple to integrate into the manufacturing process and does not require extensive programming. To reach into a bin at the optimal angle and grab the correct part, a robot must correctly calculate picking parameters.
Automation, according to KUKA, has the potential to relieve humans of repetitive bin-picking labour with adequate planning. Roboception enables collision-free image selection. Roboception's 3D camera sends photos of picking things and their surroundings to a computer for "perfect, singularity-free" path planning, according to KUKA. The camera is included as part of the bundle.
THE KUKA. SmartBinPicking software analyses the most effective path for the robot arm to take to reach the desired item, taking the robot structure and gripper into account. According to the companies, this collision-free path planning minimises downtime.
When detecting sorted or unsorted objects, the software prioritises the parts that the robot should grip first, possibly because they are on top.