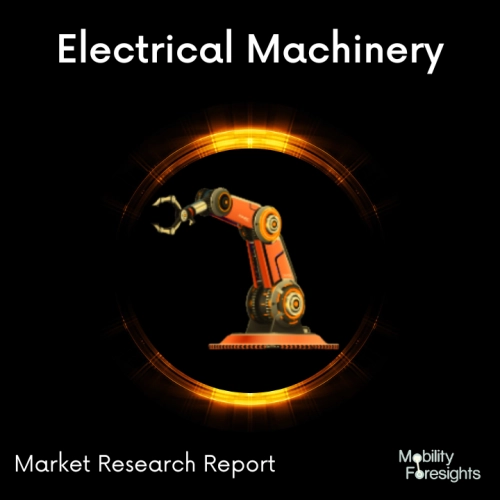
- Get in Touch with Us
Last Updated: Apr 25, 2025 | Study Period: 2024-2030
Any refrigeration or air conditioning system must have an Air Conditioning Filter Drier. The basic operation of these devices and the distinctions between the numerous varieties that are now on the market are described for technicians .
In a refrigeration or air conditioning system, a filter-drier serves two vital purposes: first, it adsorbs system impurities like water, which can produce acids, and second, it provides physical filtering.
Each component must be evaluated to ensure proper and cost-effective dryer design.The most crucial role of a dryer is to be able to drain water from a refrigeration system.Water can originate from a variety of places, including motor windings, system leaks, trapped air from poor evacuation, and others.
Another source results from incorrect handling of hygroscopic polyolester (POE) lubricants, which rapidly absorb moisture. Compared to the previously used mineral oils, POEs can absorb more moisture from their environment and hold it much tighter.
This water can lead to freeze-ups and metallic component corrosion.Hydrolysis, a reaction between POEs and water in the system, can also result in the formation of organic acids.Reduce the amount of water in the system to stop the development of these acids.
Desiccants are used inside the filter-drier to achieve this. Molecular sieve, activated alumina, and silica gel are the three desiccants that are most frequently used. Crystalline sodium alumina-silicate materials (synthetic zeolites) called molecular sieves have cubic crystals and are used to selectively adsorb molecules based on their size and polarity. The crystal structure is honeycombed with pores or cavities that are spaced regularly.
The Global Air Conditioning Filter Drier Market accounted for $XX Billion in 2023 and is anticipated to reach $XX Billion by 2030, registering a CAGR of XX% from 2024 to 2030.
The Danfoss DMB/DCB bi-flow Air Conditioning Filter Drier makes sure that the refrigerant liquid always passes through the filter drier moving from the outside of the filter core into the center.
In this manner, regardless of flow direction, all dirt particles are kept. The core blend of DCB filter dryers, which is 80% Molecular Sieve and 20% Activated Alumina, is ideal for systems that operate at high condensing temperatures and demand great drying capacity.
They are specifically advised for use with HCFC and mineral oil, as well as HFC and polyolester oil refrigerants. The 100% molecular sieve core of DMB filter dryers has a high drying capacity, reducing the possibility of acid generation (hydrolysis). They are advised for use with polyolester, HFC, and HCFC refrigerants.
Sl no | Topic |
1 | Market Segmentation |
2 | Scope of the report |
3 | Abbreviations |
4 | Research Methodology |
5 | Executive Summary |
6 | Introduction |
7 | Insights from Industry stakeholders |
8 | Cost breakdown of Product by sub-components and average profit margin |
9 | Disruptive innovation in the Industry |
10 | Technology trends in the Industry |
11 | Consumer trends in the industry |
12 | Recent Production Milestones |
13 | Component Manufacturing in US, EU and China |
14 | COVID-19 impact on overall market |
15 | COVID-19 impact on Production of components |
16 | COVID-19 impact on Point of sale |
17 | Market Segmentation, Dynamics and Forecast by Geography, 2024-2030 |
18 | Market Segmentation, Dynamics and Forecast by Product Type, 2024-2030 |
19 | Market Segmentation, Dynamics and Forecast by Application, 2024-2030 |
20 | Market Segmentation, Dynamics and Forecast by End use, 2024-2030 |
21 | Product installation rate by OEM, 2023 |
22 | Incline/Decline in Average B-2-B selling price in past 5 years |
23 | Competition from substitute products |
24 | Gross margin and average profitability of suppliers |
25 | New product development in past 12 months |
26 | M&A in past 12 months |
27 | Growth strategy of leading players |
28 | Market share of vendors, 2023 |
29 | Company Profiles |
30 | Unmet needs and opportunity for new suppliers |
31 | Conclusion |
32 | Appendix |