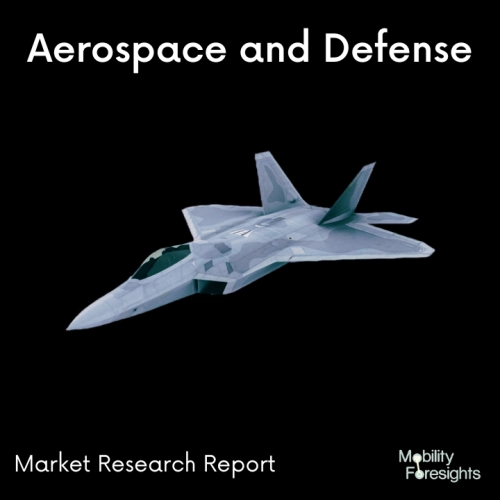
- Get in Touch with Us
Last Updated: Apr 25, 2025 | Study Period: 2024-2030
Aviation refueling is not new, but the technology has advanced significantly since the first in-flight refueling operation. Transferring gasoline from a tanker to another aircraft by aerial refueling, or refueling in the air, is known as aerial refueling (the receiver). A
aerial refueling has been utilised by military aircraft for almost a century. Aerial refueling, often known as mid-air refueling, is the pumping of gasoline from a tanker aircraft to another aircraft. The protocols call for the planes to fly in a line.
In 1921, a canister of gasoline was physically transferred from a Lincoln Standard biplane to a Curtis Jenny aeroplane in order to perform the first airborne refueling.
The altitude requirements of thousands of feet in the air and have a hefty gasoline jug on your back as you jump from one jet to another. Soon, inventors had the bright notion of dropping a hose from a plane to another. Aerial refuelling has made it possible for receiving aircraft to fly large distances without making an actual landing.
A single flying boom can move 6,000 pounds of fuel in a minute. 1 to 2 tonnes of gasoline per minute may be transferred using just one hose and drill. Fighter aircraft, on the other hand, cannot take in as much fuel as bombers and other big aircraft.
Modern fighter aircraft can absorb 1,000 to 3,000 lbs of fuel per minute from the boom or the hose-and-and-drogue.) per minute of fuel intake Refuelling fighter aircraft using the flying boom eliminates the flying boom's main advantage over the hose-and-and-drogue method.
S No | Overview of Development | Development Detailing | Region of Development | Possible Future Outcomes |
1 | Lockheed reveals new LMXT refueling tanker, firing the opening salvo in US Air Force competition | The LMXT is a variant of the Airbus A330 Multi Role Tanker Transport, modified specifically for U.S. Air Force operators. Changes include an upgraded suite of communications for joint all-domain command and control as well as improvements to range and fuel-offload capability. | USA | This would enhance better Technologies and production |
2 | Boeing to build Navy Refuelling drones in new facility at Mascoutah airport | The Boeing Co. is building a production facility at MidAmerica St. Louis Airport in Mascoutah that will be used to make the U.S. Navyâs first aircraft-refuelling drones. | USA | This would enhance better Technologies and production |
As global tensions rise, governments are working to improve their air combat and support capabilities. Several countries are investing in modernizing or replacing their old transport aircraft fleets with newer models.
The sector has seen many transport aircraft acquisition and upgrade operations in the last few years due to an increase in defence spending by a number of countries across the world.
Aerial refueling has grown in importance to military aircraft. The worldwide armed forces are expanding the number of aircraft that can be refuelled in mid-air since having this capability will increase the fighting range.
The United States, which is the world's greatest spender on defence, is a major customer for transport aircraft in the region. The transport aircraft and helicopter fleet of the United States is the largest in the world. The government also intends to expand its fleet of transport aircraft in the near future.
Most nations are putting their efforts into improving their military might. Geographical difficulties, territory and border conflicts, and the need to upgrade military fleets with fourth- and fifth-generation fighter planes with greater payload capacity and range are all prompting militaries to beef up their arsenals.
Currently, Automated Air-to-Air Refueling (A3R) is a concept in its infancy stage and different advancements are carried out to offer it to the market. For A3R to become a reality, more advanced control systems must be developed, including relative positioning systems, data connection systems, and aerial vehicle operations from a distance.
Europe has major capability gaps in air-to-air refueling. This was made clear during operations in Mali, Libya, and Kosovo, where European troops had to largely rely on US assets. The European Defense Agency is working on short, mid, and long-term solutions to this problem. A400M AAR capability, strategic tanker capabilities, and asset optimization have all been EDA's focus.
The Global Air to Air Refuelling market can be segmented into following categories for further analysis.
With the introduction of the Advanced Aerial Refueling Family of Systems (AAR FoS) programme, the Air Force has put yet another nail in the coffin of a future bridge tanker competition.
The Air Force Life Cycle Management Center alerted the aviation sector in a request for information that it is attempting to design a much more capable future system while also seeking significant enhancements to existing tankers.The refuelling of unmanned aircraft and electronic warfare will be two of the new tasks for tankers.
"An evolutionary strategy to add new capability to the present tanker fleet (KC46A/KC-135R/T), while establishing the overall needs for a new tanker aircraft," the AFLCMC described the AAR FoS as. The "most effectively implement solutions that improve tanker fleet operations" will be achieved through this dual-track strategy.
Others "in early stages of development and maturation" will continue to be developed for the still-undefined KC-Z effort, which has been described by transport leaders as a potentially smaller and stealthy aircraft that can escort fighters and bombers into heavily-defended enemy airspace, while some of the "new and mature technologies" sought from industry will be used to upgrade the KC-46 and KCX-135.
Military transport cum refueling planes are essential in combat operations.There are several mission-critical jobs they do, including as carrying soldiers, weapons, and other military equipment to improvised runways in risky locations and conducting multi-role responsibilities such as aerial refueling, information collection, and rescue missions.
From remote vision systems to drones, aerial refuelling technology has made leaps in recent years. If perfected, it could have a lasting impact on the future of military aviation. Ross Davies checks out some of the latest developments.
The automatic refueling system works by having the air tanker's air refueling operator approach and track the receiver at first, as normal.This location is then determined by using innovative passive techniques like image processing. When the automated system is triggered, a completely automated flight control system sends the boom towards the receiver's receptacle.
Usage of the ARO, relative distance-keeping mode, or full auto mode is done to perform contact with the telescopic beam inside the boom. Airbus' Space division first employed the imaging technology that underlies the automated AAR approach to create satellite refueling or debris removal systems.
Airbus Defense and Space's Incubator Laboratory continued to develop and apply it for the tanking application, as well.The other technology which has been brought into latest integrations onboard the aircraft refuelling probes is the Remote vision systems.
The RVS is basically a suite of cameras, sensors and software that is supposed to allow boom operators sitting inside the aircraft to safety steer the boom into the aircraft needing fuel.But in certain conditions, the system produces distorted imagery that increases the risk of the boom hitting another aircraft.
Northrop Grumman's KC-30 Tanker Aerial Refuelling Boom System Successfully Completes Electrostatic Discharge Tests.Northrop Grumman Corporation's KC-30 Tanker innovative Aerial Refuelling Boom System (ARBS) has achieved another important technological milestone with the successful completion of electrostatic discharge testing.
The testing featured an immediate electrical charge of 200,000 volts on the boom's nozzle, replicating the arc that may be created when the ARBS makes contact with a receiver aircraft during in-flight refuelling. The tests were carried out using a fully functional ARBS built by Northrop Grumman KC-30 Team member EADS and deployed on an A310 demonstration aircraft.
Aerial circumstances in flight may generate electrostatic buildup on any aircraft, and when a boom hits the reception aircraft during aerial refuelling, significant voltage discharges could result. The results of the successful ground-based electrostatic testing demonstrated that the ARBS and its fly-by-wire control system are not impacted by such hypothetical significant electrical spikes.
As a consequence, the A310 demonstrator aircraft is ready for its next ARBS flight tests, which will include in-flight interactions and airborne fuel transfers with a broad spectrum of receiver aircraft.
The ARBS, which has a maximum nominal fuel flow rate of 1,200 gallons per minute, is the most advanced boom currently in use. The boom operator and the pilot of the receiving aircraft will benefit substantially from the automated load relief system's broad refuelling envelope and improved controllability during refuelling operations. Traditional failure rates and downtime are considerably decreased by the boom's all-electric construction.
The KC-30 Tanker from Northrop Grumman is equipped with two underwing hose and drogue refuelling pods in addition to an ARBS and hose and drogue unit located on the centerline.
As a result, the KC-30 Tanker can refuel a broad spectrum of military aircraft from the United States and NATO. U.S., German, and Canadian Air Force tankers are already equipped with the hose and drogue system from the KC-30.
The EADS A330 Multi-role Tanker Transport, which was chosen to assist the air forces of Australia, the United Kingdom, and the United Arab Emirates, is the basis for the KC-30 Tanker aircraft. With all refuelling systems fitted, the first KC-30B of the Australian Air Force is putting its rigorous flight test programme to the test.
The KC-30 Tanker aircraft will be built in Mobile, Alabama, and will employ 25,000 Americans at 230 different firms. Northrop Grumman will lead a world-class industrial team that includes EADS North America, General Electric Aviation, and Sargent Fletcher.
Northrop Grumman's KC-30 Tanker carries 45,000 pounds more fuel than a KC-135 or any rival, thus increasing the US Air Force's worldwide reach. The KC-30 is also intended to refuel Navy and coalition aircraft, as well as to act as a multi-role transport plane for people, goods, and medical evacuation patients.
The KC-30 is equipped with defence systems, precise fly-by-wire technology, and the potential to integrate a militarised communications suite as well as a worldwide support network.
Northrop Grumman Corporation is a multinational defence and technology business with 120,000 workers that provides innovative systems, products, and solutions to government and commercial clients worldwide in information and services, electronics, aircraft, and shipbuilding.
However, refueling pods may be added to current aircraft designs if the "probe-and-drogue" method is employed, even if the aircraft supplying the fuel is specifically built for the job at hand.
This activity has only been employed in military operations due to the high expense of the refueling equipment on both tanker and reception planes and the specific handling of the planes to be refuelled (extremely tight "line astern" formation flying).
There isn't any evidence of civilian in-flight refueling taking place on a regular basis.
Boeing has been pioneering in development of the aerial refueling or air to air fueling systems in the market development requirements to have better technological integration placed across the global scale of military operations.
Most recently it has tested upon the MQ-25A Stingray, a navy unmanned aerial tanker prototype, was sent to the test by flying for two and a half hours with an ARS at the MidAmerica Airport in Illinois.
Boeing EA-18G Growler, Lockheed Martin F-35C, and Boeing F/A-18 Super Hornet will all be served by the autonomous system. The development of self-flying aircraft, such as the next-generation unmanned system, will be useful for a variety of military purposes in the future.The aerial refueling systems market is expected to increase in the future years as more of this technology is integrated.
Lockheed Martin has recently made its entry into the transport cum refueling tanker system of operations which are focused upon military branch of requirements in the market.
The LMXT is an Airbus A330 Multi Role Tanker Transport version customized for use by the U.S. Air Force. Upgraded communications enabling joint command and control across all domains, as well as enhancements to range and fuel-offload capabilities, are also part of the changes.
The LMXT will have an open-architecture backbone that will allow additional communication systems to be added, as well as a multi-domain operations node that will increase onboard situational awareness to offer robust communications and datalink for assets throughout the force.
1 | Market Segmentation |
2 | Scope of the report |
3 | Abbreviations |
4 | Research Methodology |
5 | Executive Summary |
6 | Introduction |
7 | Insights from Industry stakeholders |
8 | Cost breakdown of Product by sub-components and average profit margin |
9 | Disruptive innovation in the Industry |
10 | Technology trends in the Industry |
11 | Consumer trends in the industry |
12 | Recent Production Milestones |
13 | Component Manufacturing in US, EU and China |
14 | COVID-19 impact on overall market |
15 | COVID-19 impact on Production of components |
16 | COVID-19 impact on Point of sale |
17 | Market Segmentation, Dynamics and Forecast by Geography, 2024-2030 |
18 | Market Segmentation, Dynamics and Forecast by Product Type, 2024-2030 |
19 | Market Segmentation, Dynamics and Forecast by Application, 2024-2030 |
20 | Market Segmentation, Dynamics and Forecast by End use, 2024-2030 |
21 | Product installation rate by OEM, 2023 |
22 | Incline/Decline in Average B-2-B selling price in past 5 years |
23 | Competition from substitute products |
24 | Gross margin and average profitability of suppliers |
25 | New product development in past 12 months |
26 | M&A in past 12 months |
27 | Growth strategy of leading players |
28 | Market share of vendors, 2023 |
29 | Company Profiles |
30 | Unmet needs and opportunity for new suppliers |
31 | Conclusion |
32 | Appendix |