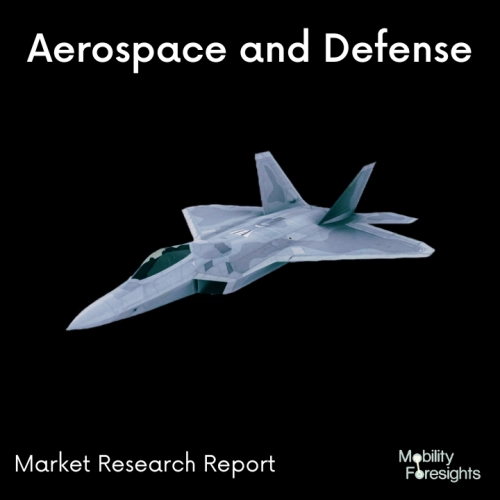
- Get in Touch with Us
Last Updated: Apr 25, 2025 | Study Period:
Brakes are generally used to slow down the aircraft during the runway rollout and at the time of landing. It is necessary to ensure safety and directional control of aircraft during ground operations. With the development of new technologies, electronic braking systems provide anti-skid and fully integrated brake control.
The airlines tend to use electric brakes to avoid fuel consumption and high maintenance costs, which further adding better performance than air brakes/disc brakes. The dependent factors on designing the braking system are: minimum stopping distance, a higher amount of heat dissipation, ease of use and design parameters are dependent on the size of the aircraft.
SI No | Timeline | Company | Developments |
1 | November 2021 | Collins Aerospace | Collins Aerospace partnered with Taqnia Space in order to expand the ACARS coverage of Saudi Arabia. |
2 | November 2021 | Collins Aerospace | Collins Aerospace has opened a new facility and decided to expand its operations in Lenexa, Kansas. |
3 | July 2021 | Collins Aerospace | For the expansion of its global repair facility in Monroe, Collins Aerospace has invested $30 million for it. |
The rise in the traffic of air passengers in recent years has led to an increase in aircrafts demand. The growing demand for aircraft increasing the demand for the sophisticated aircraft braking system.
Moreover, brakes need to work at extreme conditions, which results in degradation of the material due to wear and corrosion, which creates an opportunity for industries to develop materials with a good life. Another key condition is in search of lighter aircraft brakes. This opens the research opportunities in the metallurgy sector.
In commercial aviation segment, companies are facing disruption in production of aircraft as workers affected due to COVID-19, passengers stop travelling like before, and new changes demanding by the customers according to the pandemic situation in the aircraft (technology, safe interiors, delivery time). This effects key component suppliers.
Honeywellâs aerospace segment has seen a decline in revenues from $14.8 billion in 2017 to $14.0 billion in 2019 due to spin-off of the companyâs transportation business. Including the recent COVID-19 pandemic this segment is likely to be the worst hit for the company, expected to a revenue drop of 14% to $12.1 billion in 2020.
Parker Hannifin aerospace segment has experienced a loss of 4.19% of total net sales from $14.3 billion previous years to $13.7 billion. Sales for the aerospace segment in 2020 were higher than in 2019 due to the higher volume of military OEM and aftermarket businesses.
Operating income margin has decreased from 19.4% to 17.4% due to production half of Boeing 737 MAX during 2020. There is a huge decline in diversified industrial segment operating income by approximately 14% in the North America region and approximately 17% international regions (Asia-Pacific, Europe combined).
Crane Co. operating sales were $798 million during the first quarter of 2020 which is 4% less compared to 2019, which reduced operating profits range from $114 million in 2019 to $80 million in the first quarter of 2020.
In aerospace segment, Crane Co. experienced loss in net sales from $194.6 million in 2019 to $192.9 million in the first quarter of 2020 and loss in operating profits from $44.8 million in 2019 to $43.8 million in the first quarter of 2020.
The global aircraft brakes market is estimated at $XX Million in 2023 growing at --% CAGR till 2030
SI No | Timeline | Company | Developments |
1 | September 2021 | Collins Aerospace | Collins Aerospace was selected by the US Air Force and Lockheed Martin for the delivery of boltless wheels and carbon brakes for 60 C-130J super Hercules Aircraft. |
2 | August 2021 | Collins Aerospace | The second largest 737 Copa Airlines has selected Collins Aerospace for its 737NG aircraft with new wheels and carbon brakes. |
3 | May 2021 | Collins Aerospace | Collins Aerospace has upgraded its US Navy C-130 Fleet by providing long-lasting wheels and carbon brakes. |
4 | April 2021 | Collins Aerospace | Collins Aerospace was selected by the US Air Force in order to modernize the wheels and brakes of B-52 aircraft. |
5 | - | APS | APS has launched the new brakes for the Pilatus PC-12 with Cleveland brakes. |
6 | - | Collins Aerospace | Collins Aerospace has released the DURACARB carbon brake technology with lower weight and longer life. |
Aircraft brakes are becoming greener and cleaner, with longer on-wing life. Manufacturers are stressing electric brake actuation [eBrake] for next-generation aircraft, as well as a desire to use more ecologically friendly components in the braking system.
While both carbon and steel remain the dominant materials for brakes, all new programs have shifted away from steel braking systems. Focusing on carbon manufacturing techniques in order to build a long-lasting carbon heat sink, and focusing on extending the life of the current material set.
Greater resistance to damage from the heat created when the brakes are applied is preferred.Honeywell is working on an eBrake device that will eliminate the need for hydraulics and provide extended service.
Honeywell is nearing completion on the conversion of its legacy brake for the Airbus A330ceo to its Carbenix brake, which will be utilized on both the A330ceo and A330neo.
Cabenix features a sophisticated integrated design and proprietary anti-oxidant protection from the OEM's latest generation of carbon friction materials. Its advantages include increased durability, improved stopping power, decreased weight, and lower cost.
Carbon-Carbon Brakes: Both commercial and military aircraft are increasingly using carbon-carbon brakes. The composite material used to create these brakes is composed of carbon fibers encased in a carbon matrix. High heat resistance, superior performance in high-energy braking scenarios, longer life than conventional steel brakes, and lower weight are just a few benefits of carbon-carbon brakes.
Technology for using brakes by wire: Brake-by-wire systems are being created and used in contemporary airplanes. In these systems, electronic sensors and actuators are employed in place of conventional hydraulic systems to convey brake commands from the pilot's input to the brakes. Increased control, lighter weight, easier maintenance, and the potential for integrating braking systems with other aircraft systems are among the benefits of brake-by-wire technology.
Electric motors and mechanical components are used in electro-mechanical brakes to activate the braking system. These brakes have benefits like precise control, quick responses, increased dependability, and fewer maintenance requirements. Electro-mechanical brakes are being investigated in electric aircraft and hybrid electric propulsion systems.
Health Monitoring Systems: Aircraft brakes are being equipped with cutting-edge health monitoring systems. These systems track brake performance, spot irregularities, and give maintenance teams real-time feedback using sensors and data processing algorithms. Systematic maintenance, early problem diagnosis, and increased brake reliability are all made possible via health monitoring.
Heat Management and Cooling: For airplane brakes, efficient heat management and cooling systems are essential. Modern brake cooling systems help dissipate heat produced during braking and prevent overheating. Examples include forced air cooling and heat sink designs.A more effective heat management system guarantees consistent braking performance, lessens wear and tear, and increases the lifespan of the brakes.
SI No | Timeline | Company | Updates |
1 | Q3-2021 | Crane | The net sales of Crane at the end of the third quarter was $834 million and in 2020 the net sales was $686 million. |
2 | H1-2021 | Meggitt | The revenue of Meggitt at the end of the first half was £680 million and in the previous year the revenue was £916.8 million. |
3 | November 2021 | Collins Aerospace | Collins Aerospace acquired the Dutch Thermoplastic Components in order to deliver light, cost-efficient and sustainable aircraft structures. |
4 | August 2021 | Collins Aerospace | Collins Aerospace completed the acquisition of FlightAware for the purpose of flight tracking and data platform. |
The key prominent suppliers of aircraft braking systems/parts in the market are Honeywell, Crane Co., Meggitt PLC, Parker Hannifin Corp., Mersen Corporate services SAS. They produce and supply brakes, wheels, braking systems with latest technological progression to most of military and civil aircraft.
The companies now likely improve and make more integrated electric brake technology and develop steel braking systems for better performance factor.
Sl no | Topic |
1 | Market Segmentation |
2 | Scope of the report |
3 | Abbreviations |
4 | Research Methodology |
5 | Executive Summary |
6 | Introduction |
7 | Insights from Industry stakeholders |
8 | Cost breakdown of Product by sub-components and average profit margin |
9 | Disruptive innovation in the Industry |
10 | Technology trends in the Industry |
11 | Consumer trends in the industry |
12 | Recent Production Milestones |
13 | Component Manufacturing in US, EU and China |
14 | COVID-19 impact on overall market |
15 | COVID-19 impact on Production of components |
16 | COVID-19 impact on Point of sale |
17 | Market Segmentation, Dynamics and Forecast by Geography, 2024-2030 |
18 | Market Segmentation, Dynamics and Forecast by Product Type, 2024-2030 |
19 | Market Segmentation, Dynamics and Forecast by Application, 2024-2030 |
20 | Market Segmentation, Dynamics and Forecast by End use, 2024-2030 |
21 | Product installation rate by OEM, 2023 |
22 | Incline/Decline in Average B-2-B selling price in past 5 years |
23 | Competition from substitute products |
24 | Gross margin and average profitability of suppliers |
25 | New product development in past 12 months |
26 | M&A in past 12 months |
27 | Growth strategy of leading players |
28 | Market share of vendors, 2023 |
29 | Company Profiles |
30 | Unmet needs and opportunity for new suppliers |
31 | Conclusion |
32 | Appendix |