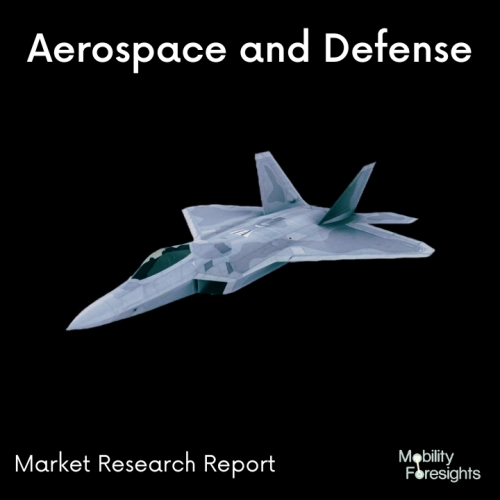
- Get in Touch with Us
Last Updated: Apr 25, 2025 | Study Period: 2023-2030
The flight deck and cabin temperatures of the aircraft are monitored using the cabin temperature sensors. Thermocouples and resistance temperature detectors are the two most popular temperature sensors used in aircraft. (RTD).These temperature sensors are quite similar, however the thermocouples can survive higher, more extreme temperatures while the RTDs are far more accurate.
Since AMETEK is familiar with the essential performance characteristics, it assesses them at an early stage of the development program for the application in question to further reduce risk. Due to comprehensive testing and field validation, AMETEK sensors are used.
Aircraft temperature measuring equipment provides immediate, accurate input for tracking temperature changes in real time. These sensors may be found in an aircraft's cabin or engine. Temperature sensors in engines gauge the temperature of coolants, hydraulic oils, and fuel.
The sensors stop the engine's internal parts from overheating and posing a safety hazard.Resistors with known resistance vs. temperature are known as RTDs.
The two types of RTD elements that are most frequently employed are either thin film elements where platinum is coated on ceramic substrates or elements made of platinum wire wound around a ceramic core. Due to its tiny and reproducible package, the thin film RTD type is used in the majority of AMETEK's air temperature sensors.
A special kind of NTC thermistor sensor called the "cabin temperature sensor" keeps track of the air temperature in the passenger area to ensure the comfort of the passengers. It aids the system in adjusting cooling load, fan speed, and volume in accordance with various situations and temperatures.
The Global Aircraft cabin temperature sensorMarket accountedfor $XX Billion in 2022 and is anticipated to reach $XX Billion by 2030, registering a CAGR of XX% from 2023 to 2030.
The main advantage of wireless sensor networks is their capacity to gather more correlated data than isolated sensor monitors, which allows them to produce a more comprehensive picture of the perceived environment. They are thus perfectly suited for applications that require the monitoring of complicated environments with plenty of interdependent elements.
One such instance of a highly dynamic environment that calls for the employment of an advanced sensing system is the cabin of an aeroplane. Thus, a wireless sensor network was created and prototyped in order to better comprehend the surroundings of the aeroplane cabin.
A variable number of nodes make up the network, and each node has the ability to adapt in order to monitor a wide range of environmental conditions.
The system has now started the testing phase as mentioned in earlier releases. Twelve nodes that sense temperature, humidity, carbon dioxide, and barometric pressure are part of the current setup.
The tests were carried out using the prototype hardware and software in a mockup of the cabin environment, and the outcomes are discussed in this paper. To imitate variations in the cabin atmosphere, tests used humidifiers, heaters, and carbon dioxide.
Sl no | Topic |
1 | Market Segmentation |
2 | Scope of the report |
3 | Abbreviations |
4 | Research Methodology |
5 | Executive Summary |
6 | Introdauction |
7 | Insights from Industry stakeholders |
8 | Cost breakdown of Product by sub-components and average profit margin |
9 | Disruptive innovation in theIndustry |
10 | Technology trends in the Industry |
11 | Consumer trends in the industry |
12 | Recent Production Milestones |
13 | Component Manufacturing in US, EU and China |
14 | COVID-19 impact on overall market |
15 | COVID-19 impact on Production of components |
16 | COVID-19 impact on Point of sale |
17 | Market Segmentation, Dynamics and Forecast by Geography, 2023-2030 |
18 | Market Segmentation, Dynamics and Forecast by Product Type, 2023-2030 |
19 | Market Segmentation, Dynamics and Forecast by Application, 2023-2030 |
20 | Market Segmentation, Dynamics and Forecast by End use, 2023-2030 |
21 | Product installation rate by OEM, 2023 |
22 | Incline/Decline in Average B-2-B selling price in past 5 years |
23 | Competition from substitute products |
24 | Gross margin and average profitability of suppliers |
25 | New product development in past 12 months |
26 | M&A in past 12 months |
27 | Growth strategy of leading players |
28 | Market share of vendors, 2023 |
29 | Company Profiles |
30 | Unmet needs and opportunity for new suppliers |
31 | Conclusion |
32 | Appendix |