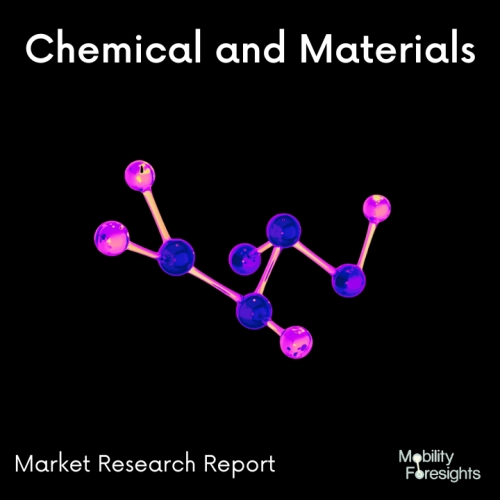
- Get in Touch with Us
Last Updated: Apr 25, 2025 | Study Period: 2024-2030
The use of carbon fibre in the construction of aircraft bodies makes them lighter, more aerodynamic, and more fuel-efficient. Reduced production and operational expenses are the result of all these variables.On an aeroplane, there are three different kinds of doors: service doors, emergency exits, and exits for passengers.
The front, middle, and back regions of big passenger aircraft are where the passenger doors that are used during boarding are particularly situated. Passengers can enter planes through a variety of doors because of these doors.
Elevators, spoilers, outboard ailerons, wing-body fairings, fore- and main landing gear doors, wing trailing-edge panels of main wings and stabilisers, and vertical and horizontal stabiliser ribs were only a few of the secondary structural components that Boeing adopted almost simultaneously.
Stress resistance - Carbon fibre components are less likely to break or wear out. Carbon is a durable and long-lasting substance that does not experience fatigue or begin to rot or disintegrate in unfavourable conditions. Resistance to corrosion - Carbon fibre is resilient in corrosive situations as well.
Polyacrylonitrile is the material used to make about 90% of the carbon fibres produced (PAN). The remaining 10% are made of petroleum pitch or rayon. These substances are all organic polymers, which have lengthy chains of molecules joined by carbon atoms.Carbon fiber-reinforced plastic is referred to as CFRP.
A material known as CFRP is made up of a base or carrier substance also known as matrix and a second reinforcing component known as carbon fibre that is incorporated into the matrix.
The Global Aircraft carbon fiber doors market accounted for $XX Billion in 2022 and is anticipated to reach $XX Billion by 2030, registering a CAGR of XX% from 2024 to 2030.
Forenge Technologies Private LimitedSimilar to the numerous layers of a phyllo-dough pastry, the fuselage of a modern aeroplane is constructed from numerous sheets of various composite materials. After being piled and shaped into a fuselage, these layers are fused together to create a strong, aerodynamic shell in ovens and autoclaves the size of storage facilities.
Now, MIT engineers have created a process for making composite materials of the highest quality without using huge ovens and pressure vessels. The method might facilitate the production of huge, high-performance composite structures like wind turbine blades and aeroplanes.
Sl no | Topic |
1 | Market Segmentation |
2 | Scope of the report |
3 | Abbreviations |
4 | Research Methodology |
5 | Executive Summary |
6 | Introduction |
7 | Insights from Industry stakeholders |
8 | Cost breakdown of Product by sub-components and average profit margin |
9 | Disruptive innovation in the Industry |
10 | Technology trends in the Industry |
11 | Consumer trends in the industry |
12 | Recent Production Milestones |
13 | Component Manufacturing in US, EU and China |
14 | COVID-19 impact on overall market |
15 | COVID-19 impact on Production of components |
16 | COVID-19 impact on Point of sale |
17 | Market Segmentation, Dynamics and Forecast by Geography, 2024-2030 |
18 | Market Segmentation, Dynamics and Forecast by Product Type, 2024-2030 |
19 | Market Segmentation, Dynamics and Forecast by Application, 2024-2030 |
20 | Market Segmentation, Dynamics and Forecast by End use, 2024-2030 |
21 | Product installation rate by OEM, 2023 |
22 | Incline/Decline in Average B-2-B selling price in past 5 years |
23 | Competition from substitute products |
24 | Gross margin and average profitability of suppliers |
25 | New product development in past 12 months |
26 | M&A in past 12 months |
27 | Growth strategy of leading players |
28 | Market share of vendors, 2023 |
29 | Company Profiles |
30 | Unmet needs and opportunity for new suppliers |
31 | Conclusion |
32 | Appendix |