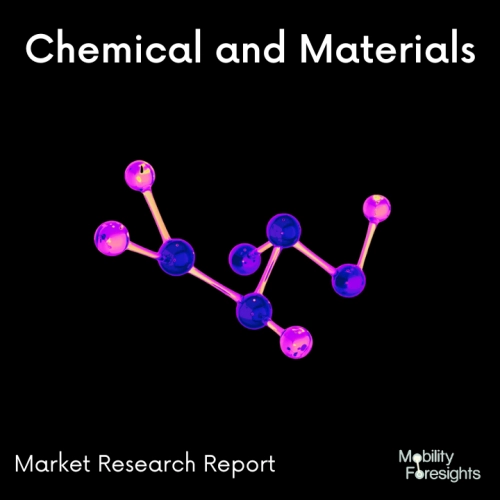
- Get in Touch with Us
Last Updated: Apr 25, 2025 | Study Period: 2024-2030
Due to its much improved rigidity and tensile characteristics compared to fiberglass, carbon fiber has long been recognized as having advantages for lowering the mass of wind turbine blades. Although originally created for the aerospace industry, the high relative cost of carbon fiber materials has prevented their widespread application in the cost-conscious wind business.
While the aerospace industry uses carbon fiber materials in its military applications and aircraft, the principal structural material used in the manufacture of wind turbine blades is fiberglass.
The Global Aircraft carbon fiber turbine blade market accounted for $XX Billion in 2022 and is anticipated to reach $XX Billion by 2030, registering a CAGR of XX% from 2024 to 2030.
Future land-based and offshore wind turbines will have longer blades in large part due to carbon fibre, which is seen as a crucial technology in this regard.The capacity to construct long, slender wind turbine blades and lower mass of carbon fibre composites led to system-level advantages for employing them to cut the levelized cost of wind energy, according to the project.
In proportion to their length, wind turbine blades increase greatly in mass. For rotor size to increase further and the levelized cost of wind energy to decrease, controlling blade mass is essential. These goals can be achieved with the help of carbon fibre, which will facilitate a greater spread of wind energy in the US.
Because of the specific loading requirements of wind turbines, there is a considerable opportunity for innovation in the development of carbon fibre to make materials that are better suited for them. Comparing the performance of the textile carbon fibre material they studied to that of currently available commercial materials, they found that it performed at a higher level.
This type of material would allow carbon fibre to be more widely used in wind turbine blade designs, expanding the market for fibre producers.
The demand for the type of material used in wind turbines is driven by compressive strength, which is more important than tensile strength. Regardless of material performance, the wind sector normally chooses materials based on final cost.
When spar caps were produced from either of the carbon fibre materials instead of fibreglass, a 25% reduction in blade mass was seen, demonstrating the benefits of carbon fibre materials. Blades for wind turbines with spar caps made of heavy-tow textile carbon fibre cost 40% cheaper to make than blades with spar caps made of standard commercial carbon fibre.
Sl no | Topic |
1 | Market Segmentation |
2 | Scope of the report |
3 | Abbreviations |
4 | Research Methodology |
5 | Executive Summary |
6 | Introduction |
7 | Insights from Industry stakeholders |
8 | Cost breakdown of Product by sub-components and average profit margin |
9 | Disruptive innovation in the Industry |
10 | Technology trends in the Industry |
11 | Consumer trends in the industry |
12 | Recent Production Milestones |
13 | Component Manufacturing in US, EU and China |
14 | COVID-19 impact on overall market |
15 | COVID-19 impact on Production of components |
16 | COVID-19 impact on Point of sale |
17 | Market Segmentation, Dynamics and Forecast by Geography, 2024-2030 |
18 | Market Segmentation, Dynamics and Forecast by Product Type, 2024-2030 |
19 | Market Segmentation, Dynamics and Forecast by Application, 2024-2030 |
20 | Market Segmentation, Dynamics and Forecast by End use, 2024-2030 |
21 | Product installation rate by OEM, 2023 |
22 | Incline/Decline in Average B-2-B selling price in past 5 years |
23 | Competition from substitute products |
24 | Gross margin and average profitability of suppliers |
25 | New product development in past 12 months |
26 | M&A in past 12 months |
27 | Growth strategy of leading players |
28 | Market share of vendors, 2023 |
29 | Company Profiles |
30 | Unmet needs and opportunity for new suppliers |
31 | Conclusion |
32 | Appendix |