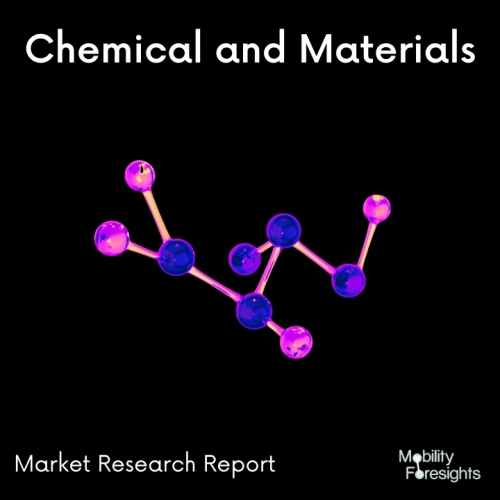
- Get in Touch with Us
Last Updated: Apr 25, 2025 | Study Period: 2024-2030
An integrated thermoplastic composite window frame's design and analysis for use in regional aircraft. A composite window frame that has been subjected to shear pressures representative of the stress distribution in the fuselage skin caused by flight loads is being studied for its ability to buckle, damage, and fail.
The investigation of the bonding of the contact between the thermoplastic window frame and the thermoset fuselage skin included both adhesive bonding and riveting. The majority of an aircraft's fuselage, wings, and tail are made of carbon fibres, such as the Boeing 787 Dreamliner.
The Global Aircraft carbon fiber window frame market accounted for $XX Billion in 2022 and is anticipated to reach $XX Billion by 2030, registering a CAGR of XX% from 2024 to 2030.
Onyx FR-A and Carbon Fiber FR-A are two new composite materials launched by Markforged that are intended for use in aerospace and other highly regulated industries.
The National Center for Advanced Materials Performance (NCAMP), a division of the National Institute for Aviation Research (NIAR), at Wichita State University, is conducting a qualification program for these two novel materials on the X7 industrial 3D printer.
As soon as it is finished, Markforged will have the first continuous fibre-reinforced additive manufacturing (AM) method certified by NCAMP, one of the two organisations recognized by the Federal Aviation Administration (FAA) to certify materials for flight.
Materials made of Onyx FR-A and Carbon Fiber FR-A are traceable, adhere to NCAMP regulations, and are intended to meet Flame, Smoke, and Toxicity (FST) requirements for various parts in aircraft interiors.
Due to their superior strength-to-weight ratio, flawless surface quality, and high consistency, they are especially designed for end-use applications in demanding industries like aerospace and military.
The use of Onyx FR-A and Carbon Fiber FR-A materials allows aerospace manufacturers and other businesses in highly regulated sectors that demand higher levels of documentation to more freely investigate the potential of additive manufacturing and high strength continuous fibre reinforced end-use parts.
Window frames made of thermoplastic composite to reduce aeroplane weightTo minimise part weight and production costs, the Eurecat technology centre created thermoplastic composite window frames for regional aeroplanes utilising modern industrial manufacturing technologies.
The development is part of the WINFRAME 4.0 project, which "has allowed us to draw on thermoplastic composites for building regional aircraft as well as develop faster and more reliable processes by using carbon fibre-reinforced polymers and innovative manufacturing concepts," according to Mara Eugenia Rodrguez, director of Eurecat's Composites Unit.
The project "demonstrates the potential of Industry 4.0 when it comes to solving technological problems in manufacturing processes for complex thermoplastic-based structures," she says. This demonstrates that they "can meet the challenges posed by new sustainability standards and the circular economy."
WINFRAME 4.0 was coordinated by Eurecat and ran under the CleanSky 2 call, with LEONARDO as subject manager with the support of Sofitec Aero.
On the technological side, WINFRAME 4.0 included the use of "out-of-autoclave" technology, which resulted in considerable cost reductions in the fabrication of lightweight structural elements in the aviation sector.
The Composite Materials Unit led the design and manufacturing of the tooling, as well as the process validation by constructing the thermoplastic composite window frame demonstrators, which Sofitec Aero built.
Sl no | Topic |
1 | Market Segmentation |
2 | Scope of the report |
3 | Abbreviations |
4 | Research Methodology |
5 | Executive Summary |
6 | Introduction |
7 | Insights from Industry stakeholders |
8 | Cost breakdown of Product by sub-components and average profit margin |
9 | Disruptive innovation in the Industry |
10 | Technology trends in the Industry |
11 | Consumer trends in the industry |
12 | Recent Production Milestones |
13 | Component Manufacturing in US, EU and China |
14 | COVID-19 impact on overall market |
15 | COVID-19 impact on Production of components |
16 | COVID-19 impact on Point of sale |
17 | Market Segmentation, Dynamics and Forecast by Geography, 2024-2030 |
18 | Market Segmentation, Dynamics and Forecast by Product Type, 2024-2030 |
19 | Market Segmentation, Dynamics and Forecast by Application, 2024-2030 |
20 | Market Segmentation, Dynamics and Forecast by End use, 2024-2030 |
21 | Product installation rate by OEM, 2023 |
22 | Incline/Decline in Average B-2-B selling price in past 5 years |
23 | Competition from substitute products |
24 | Gross margin and average profitability of suppliers |
25 | New product development in past 12 months |
26 | M&A in past 12 months |
27 | Growth strategy of leading players |
28 | Market share of vendors, 2023 |
29 | Company Profiles |
30 | Unmet needs and opportunity for new suppliers |
31 | Conclusion |
32 | Appendix |