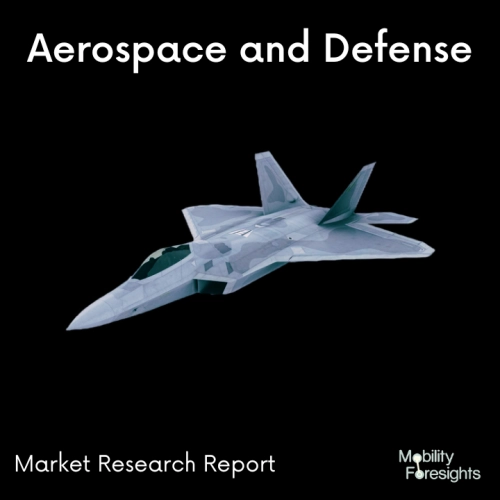
- Get in Touch with Us
Last Updated: Apr 25, 2025 | Study Period: 2024-2030
A self-contained network of parts that produce, transfer, distribute, use, and store electrical energy makes up an aircraft electrical system.
General Description All but the most basic aircraft designs require an electrical system, which is a crucial and fundamental part of the aircraft.
With the exception of the simplest aircraft designs, an electrical system is a crucial and vital part of any aircraft.
Between a light, piston-powered, single-engine general aviation aircraft and a contemporary, multi-engine commercial jet aircraft, there are significant differences in electrical system capacity and complexity.
Nevertheless, the electrical systems for aircraft at both extremes of complexity contain a lot of the same fundamental parts.
There are parts that can produce electricity in any airplane electrical system. Generators or alternators are employed, depending on the aircraft, to generate electricity.
These are typically engine-driven but can also be APU, hydraulic, or Ram Air Turbine-powered (RAT).
The output of a generator is typically 115â120V/400HZ AC, 28V DC, or 14V DC. It is possible to use generator power straight away or to change the voltage or type of current by passing it through transformers, rectifiers, or inverters.
The Global aircraft electrical energy storage system accounted for $XX Billion in 2023 and is anticipated to reach $XX Billion by 2030, registering a CAGR of XX% from 2024 to 2030.
According to a Rolls-Royce announcement, the company will create energy storage systems (ESS) that will allow aircraft to fly over 100 miles without emitting any pollutants on a single charge.
Rolls-Royce announced that it will spend GBP80 million on energy storage systems over the following ten years in order to provide this revolutionary technology.
According to the firm, the investment would reinforce its position as the industry's top provider of all-electric and hybrid-electric power and propulsion systems for aviation and result in the creation of about three hundred new jobs.
Electric and hybrid-electric propulsion systems for eVTOLs in the urban air mobility (UAM) industry as well as fixed-wing aircraft with up to 19 seats in the commuter market will be powered by aerospace-certified ESS technologies from Rolls-Royce.
The development of electric aviation prototypes is made easier with the launch of a new energy storage unit by aviation energy storage expert Electroflight.
According to Electroflight, its new SEED (Scalable, Expandable Energy Device) can be quickly installed without requiring the development of a customised battery system.
SEED was created to meet the growing demand from aerospace innovators for pre-certification electric and hybrid aircraft for test operations, which call for a battery system with the highest standards of quality and safety.
SEED is intended for use in early-stage product development.
The new battery has a 4.3 kWh capacity and 196 Wh/kg of specific energy. It operates between -20 and 60 degrees Celsius at discharge and 0 to 60 degrees Celsius at charge. It has quick charging capabilities and an independent battery management system.
By investigating and testing a wide range of technologies targeted at improving the environmental performance of aircraft, Boeing, a global leader in aerospace innovation, has set out on a mission to transform the aviation landscape.
Electrical energy storage systems (EESS) have been a crucial focus among these transformational technologies. Boeing's initiatives in this area, driven by a dedication to sustainability and a desire to lessen aviation's carbon footprint, have the potential to completely transform the market.
The aviation industry is under increasing pressure to adopt more eco-friendly methods in a time when environmental issues are at the forefront of international discussions.
Traditional airplane propulsion, which is dependent on fossil fuels, has long been linked to air pollution and greenhouse gas emissions. Given this difficulty, Boeing has made it a strategic priority to invent for a greener future.
EESS have emerged as a crucial component of Boeing's sustainability strategy due to their potential to drastically cut emissions and increase operational efficiency. Boeing's EESS initiatives are driven by a dedication to electric propulsion technologies.
Boeing wants to migrate away from using internal combustion engines and toward more electric and hybrid-electric propulsion by incorporating these technologies into airplanes.
This paradigm change offers prospects for quieter and more energy-efficient flight in addition to decreased emissions. The ecoDemonstrator program is one of Boeing's ground-breaking projects in this area.
For a variety of cutting-edge technologies, including EESS, this ongoing effort acts as a testbed. Boeing tests the viability of these technologies in real-world circumstances by working with industry partners and regulatory organizations.
In order to determine the most efficient ways to incorporate electric propulsion and energy storage into aircraft, Boeing has investigated a variety of EESS-related topics through the ecoDemonstrator effort, ranging from new battery chemistries to energy management systems.
Beyond lowering emissions and fuel usage, EESS has many benefits. When compared to conventional mechanical systems, electric systems often have fewer moving parts and are therefore more reliable.
The operational economics of airlines may benefit from decreased maintenance requirements and higher aircraft availability. EESS may also provide new design possibilities for airplanes, enhancing aerodynamics and weight distribution. Unmanned aerial vehicles (UAVs) and platforms for urban air mobility (UAM) are also included in Boeing's venture into EESS.
These developing industries stand to gain a great deal from electric propulsion and energy storage technology. Boeing's participation in these initiatives demonstrates its dedication to transforming the whole aviation ecosystem with sustainability in mind.
Boeing makes significant investments in research and development, working with academic institutions, research facilities, and technology partners to further these objectives.
In order to ensure that EESS meets the exacting safety and performance criteria required by the aviation industry, it is important to push the limits of already available technology and create new innovations.
Despite Boeing's tremendous EESS advancements, difficulties still exist. Battery technology, a foundational component of EESS, has to advance in order to attain higher energy densities, quicker charging times, and better thermal control. In order to encourage widespread adoption, regulatory frameworks and infrastructure for electric aviation must advance concurrently.
1 | Market Segmentation |
2 | Scope of the report |
3 | Abbreviations |
4 | Research Methodology |
5 | Executive Summary |
6 | Introduction |
7 | Insights from Industry stakeholders |
8 | Cost breakdown of Product by sub-components and average profit margin |
9 | Disruptive innovation in theIndustry |
10 | Technology trends in the Industry |
11 | Consumer trends in the industry |
12 | Recent Production Milestones |
13 | Component Manufacturing in US, EU and China |
14 | COVID-19 impact on overall market |
15 | COVID-19 impact on Production of components |
16 | COVID-19 impact on Point of sale |
17 | Market Segmentation, Dynamics and Forecast by Geography, 2024-2030 |
18 | Market Segmentation, Dynamics and Forecast by Product Type, 2024-2030 |
19 | Market Segmentation, Dynamics and Forecast by Application, 2024-2030 |
20 | Market Segmentation, Dynamics and Forecast by End use, 2024-2030 |
21 | Product installation rate by OEM, 2023 |
22 | Incline/Decline in Average B-2-B selling price in past 5 years |
23 | Competition from substitute products |
24 | Gross margin and average profitability of suppliers |
25 | New product development in past 12 months |
26 | M&A in past 12 months |
27 | Growth strategy of leading players |
28 | Market share of vendors, 2023 |
29 | Company Profiles |
30 | Unmet needs and opportunity for new suppliers |
31 | Conclusion |
32 | Appendix |