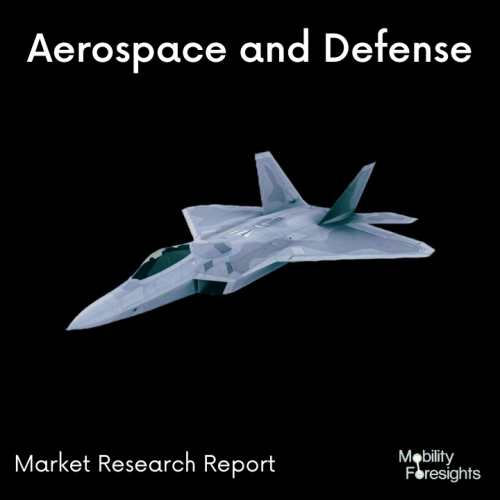
- Get in Touch with Us
Last Updated: Apr 25, 2025 | Study Period: 2023-2030
A cutting-edge microprocessor-based system called High Lift Control Systems (HLCS) offers fly-by-wire control, protection, and built-in test and maintenance. access options for the trailing edge and leading edge slats. systems for driving and actuating flaps.
A part or mechanism on an aircraft wing known as a high-lift device boosts lift, primarily during takeoff and landing situations. Wing flaps and slats are typical movable high-lift components. Modern high-lift systems are frequently hydraulically or mechanically deployed and can be rather complicated.
High lift devices are used by aircraft to enable them to fly at lower speeds without coming dangerously close to stalling. This is crucial for secure takeoffs and landings because they require the aircraft to be drastically slowed down. Every aeroplane has a wing with a specific function in mind.
Slats are extendable, high lift components on the leading edge of some fixed wing aircraft's wings. During low speed activities like takeoff, beginning climb, approach, and landing, they are meant to increase lift.
There are two major widely accepted explanations for lift on an airfoil, as previously mentioned under "Simplified Physical Explanations of Lift on an Airfoil": one based on downward deflection of the flow (Newton's laws), and one based on pressure differences coupled with changes in flow speed.
The Global Aircraft High lift monitoring system market accounted for $XX Billion in 2022 and is anticipated to reach $XX Billion by 2030, registering a CAGR of XX% from 2023 to 2030.
Modern aeroplanes need high-lift systems to fly successfully. In order to create lift during takeoff and drag during landing, these hydraulic systems extend surfaces on the leading and trailing edges of an airplane's wings.
UTC Aerospace Systems is creating a cutting-edge next-generation high-lift system that will offer operators significant benefits in terms of improved performance, reduced weight, and lower cost, despite the fact that the architecture for high-lift systems has not undergone a significant change in several decades.
The next-generation high-lift system should require fewer parts than current systems, which will cut down on the time it takes to manufacture an aeroplane. It should also minimise the loads applied to the aircraft structure, which will lead to smaller, lighter, and more fuel-efficient structural components.
Thanks to its novel gearing layout, the system should also be lightweight. To further reduce weight, the system might be constructed additively utilising cutting-edge materials.
Sl no | Topic |
1 | Market Segmentation |
2 | Scope of the report |
3 | Abbreviations |
4 | Research Methodology |
5 | Executive Summary |
6 | Introduction |
7 | Insights from Industry stakeholders |
8 | Cost breakdown of Product by sub-components and average profit margin |
9 | Disruptive innovation in the Industry |
10 | Technology trends in the Industry |
11 | Consumer trends in the industry |
12 | Recent Production Milestones |
13 | Component Manufacturing in US, EU and China |
14 | COVID-19 impact on overall market |
15 | COVID-19 impact on Production of components |
16 | COVID-19 impact on Point of sale |
17 | Market Segmentation, Dynamics and Forecast by Geography, 2023-2030 |
18 | Market Segmentation, Dynamics and Forecast by Product Type, 2023-2030 |
19 | Market Segmentation, Dynamics and Forecast by Application, 2023-2030 |
20 | Market Segmentation, Dynamics and Forecast by End use, 2023-2030 |
21 | Product installation rate by OEM, 2023 |
22 | Incline/Decline in Average B-2-B selling price in past 5 years |
23 | Competition from substitute products |
24 | Gross margin and average profitability of suppliers |
25 | New product development in past 12 months |
26 | M&A in past 12 months |
27 | Growth strategy of leading players |
28 | Market share of vendors, 2023 |
29 | Company Profiles |
30 | Unmet needs and opportunity for new suppliers |
31 | Conclusion |
32 | Appendix |