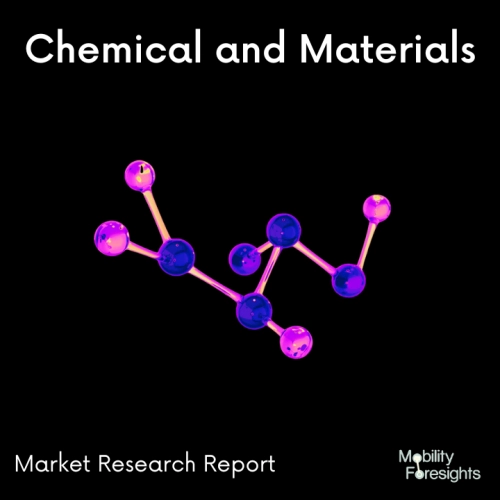
- Get in Touch with Us
Last Updated: Apr 25, 2025 | Study Period: 2024-2030
Acrylonitrile Butadiene Styrene, or ABS, is often used to make the plastics in the luggage compartments and interior of airplanes.
This plastic can be manipulated into a wide range of shapes thanks to its excellent suitability for vacuum forming. Prepregs, also known as glass fibers, can be made using the team's thermosetting resin system and a hot-melt process.
This material has excellent fire resistance and exceptional mechanical properties. Because of their extreme toughness, some plastics can withstand impact without breaking. Acrylic or polycarbonate plastics, for example, are now used to make a lot of aircraft canopies for both military and civilian aircraft.
These plastics are much lighter than glass and have a lot more impact strength than glass. Aluminum, magnesium, titanium, steel, and their alloys are the most frequently used metals in aircraft construction. A mixture of two or more metals is called an alloy.
The term "base metal" refers to the metal that makes up the majority of the alloy. Alloying elements are the other metals that are added to the base metal.
The section of an airplane where passengers travel is called an aircraft cabin. Because cruising altitudes are so high that it is impossible for passengers and crew to breathe, most modern commercial aircraft are pressurized.
The Global aircraft interior plastics market accounted for $XX Billion in 2022 and is anticipated to reach $XX Billion by 2030, registering a CAGR of XX% from 2024 to 2030.
Three new high-tech materials have been added to GE Plastics' expanding line of high-performance resins for aircraft interior plastics: Lexan1 FST9705, Noryl1 LS6010, and Ultem1 9085 resin from GE.
When taken as a whole, these distinctive materials provide customers with numerous advantages for a wide range of interior aircraft applications.
Ultem 9085 Resin Sets New Standards for Aerospace Industry Compliance, Outstanding Customer Benefits, and Top Performance.
GE Plastics today introduced a new flame-resistant Ultem 9085 resin for aircraft interiors to assist the aerospace industry in improving fuel efficiency, performance, and safety.
This new material, which outperforms GE's Ultem 9075 resin, the prior industry standard, in terms of flow and ductility, enables parts with thinner walls and excellent impact strength.
Further contrasting the two materials, the new Ultem 9085 resin supports the objective of reducing fuel consumption by reducing part weight by 5 to 15% through thinner walls.
In addition, Ultem 9085 resin offers enhanced stiffness and the highest modulus of any Ultem resin grade, ensuring excellent application durability.
The new GE product is the best choice for demanding applications like decompression grilles, window reveals, and personal service units due to its significantly improved properties.