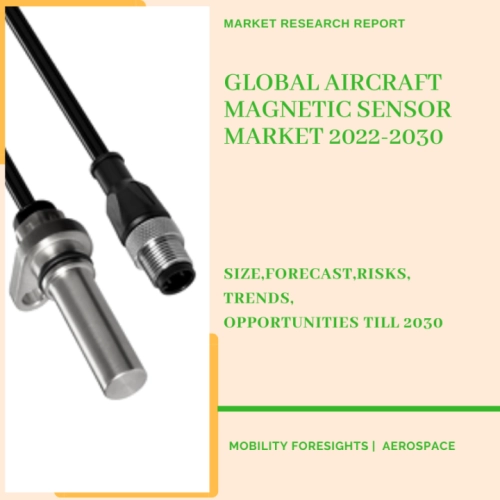
- Get in Touch with Us
Last Updated: Apr 25, 2025 | Study Period: 2022-2030
All forms of aircraft and spacecraft require the magnetometer, also referred to as a magnetic sensor, which is a sensor for gauging magnetic induction (magnetic field intensity).
It has also been extensively employed in a variety of other industries, including business, agriculture, and national security, as well as in fields like biology, medical, aerospace, and planetary science.
The position of the aircraft body, such as that of aeroplanes and satellites, can be determined by measuring the geomagnetic field vector information.
The Global aircraft magnetic sensor market accounted for $XX Billion in 2021 and is anticipated to reach $XX Billion by 2030, registering a CAGR of XX% from 2022 to 2030.
The newest 3-Axis Space Magnetometer made for tiny spacecraft by Honeywell has received full qualification. The new magnetometer satisfies the demands of the developing new space segment since it provides essential features and is designed to fit small spacecraft.
AV-Mag, a high precision 3-axis external magnetometer for AV-30 panel displays, was introduced by uAvionix. AV-Mag provides the long-term high-accuracy Directional Gyro (DG) solution that pilots have demanded by accurately measuring the earth's magnetic field and assisting the AV-30 directional heading measurement.
An electronic compass with three axes and tilt compensation is the SP-6 magnetometer. Information about the magnetic heading is output. When an SP-6 sensor is utilised independently, tilt compensation is carried out by determining the SP-6 sensor's attitude using on-board accelerometers that vector the direction of gravity.
Three magnetometers positioned perpendicular to one another are used to measure the magnetic field, producing three magnetic force vectors.
Aircraft Magnetic Structure Monitoring provided by wireless sensors.The sensors, which are built using magnetic components and amorphous ferromagnetic microwires that may respond to electromagnetic radiation, will provide useful data on the state of the component at any moment.
These will be mixed in with the dry carbon fiber so that they become an integral part of the composite and are tracked by a portable system to analyze the stresses and temperatures the part is exposed to as well as its condition.
It will be incorporated into composite materials and embedded in aeronautical parts to track the state of parts from production to recycling with the goal of extending their life, enhancing their quality, and lowering their cost.
One special characteristic that is not yet included in existing systems is the early integration of these sensors and their wireless capability. It will offer ways to produce parts of higher quality as well as more precise methods of predicting damage and flaws.
Engineers from the AMRC's composites division are assisting the partnership, which is being led by the Spanish research institute IDEKO, in creating a technology that will insert wireless sensors into materials at the outset of the production of aeronautical structures. They refer to this as manufacturing health monitoring (MHM) and structural health monitoring.
It will be a huge advancement to be able to insert highly-specific sensors into composite aerospace structures so early in the production process, and to monitor the complete life of a component.
The installation of these sensors at the very beginning of the life cycle will enable traceability of all succeeding stages of each component and monitor their state with a non-invasive system to optimize their performance.
This will alter the course of events. It will improve aircraft safety and component longevity, lower costs through predictive targeted maintenance, and provide the European and UK aircraft industries a competitive edge.
The INFINITE consortium is confident that this advanced monitoring will have a significant positive impact on the European aerospace industry's ability to reduce costs and improve component dependability, giving European equipment manufacturers (OEMs), component producers, and maintenance and repair companies a competitive edge.
Market Segmentation |
Scope of the report |
Abbreviations |
Research Methodology |
Executive Summary |
Introduction |
Insights from Industry stakeholders |
Cost breakdown of Product by sub-components and average profit margin |
Disruptive innovation in the Industry |
Technology trends in the Industry |
Consumer trends in the industry |
Recent Production Milestones |
Component Manufacturing in US, EU and China |
COVID-19 impact on overall market |
COVID-19 impact on Production of components |
COVID-19 impact on Point of sale |
Market Segmentation, Dynamics and Forecast by Geography, 2022-2030 |
Market Segmentation, Dynamics and Forecast by Product Type, 2022-2030 |
Market Segmentation, Dynamics and Forecast by Application, 2022-2030 |
Market Segmentation, Dynamics and Forecast by End use, 2022-2030 |
Product installation rate by OEM, 2022 |
Incline/Decline in Average B-2-B selling price in past 5 years |
Competition from substitute products |
Gross margin and average profitability of suppliers |
New product development in past 12 months |
M&A in past 12 months |
Growth strategy of leading players |
Market share of vendors, 2022 |
Company Profiles |
Unmet needs and opportunity for new suppliers |
Conclusion |
Appendix |