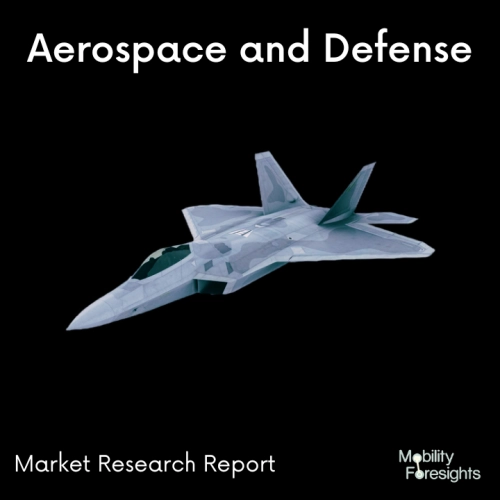
- Get in Touch with Us
Last Updated: Apr 25, 2025 | Study Period: 2023-2030
An aircraft oil cooler prevents the temperature of the aircraft oil from rising while the engine is running. If the temperature begins to rise, the oil is routed through a heat exchanger, which uses either air or fuel to cool the oil.
A radiator-like part called an oil cooler is used to keep your oil at a cool temperature. It is made up of tubes and fins that permit efficient airflow. They are typically positioned where they can get the most airflow, like in front of or behind the radiator or fans.
Any aircraft needs a jet engine oil system since it is in charge of maintaining a steady supply of oil to the aircraft's engine. To store, cool, transport, and distribute the oil required to lubricate and cool every gear, spline, bearing, and carbon seal, the recirculatory system is required.
The Global Aircraft Oil Cooler market accounted for $XX Billion in 2022 and is anticipated to reach $XX Billion by 2030, registering a CAGR of XX% from 2023 to 2030.
Development of the worldâs first air-cooling system for aircraft onboard 100kW-class power electronics - The âliquid-lessâ, clean cooling technology enlarges applicability of the power electronics.
Electric Architecture for Aircraft and Propulsion, often known as MEAAP, is a technological advancement that attempts to optimise the overall energy management of aircraft systems in order to reduce CO2 emissions from aviation.
The air-cooling system for the onboard power electronics is one of the core MEAAP ideas. Even in locations where coolant, water, and oil cannot be used, the liquid-less cooling technique provides the versatility of the power electronics application.
IHI designed the air-cooling system and successfully completed evaluation testing for the aircraft's 100kW-class high power electronics.
The New Energy and Industrial Technology Development Organization funded this development as one of its research and development projects for advanced aircraft systems towards practical application.
Although the electrification of the aircraft system reduces fuel consumption, the power electronics' heat generation poses a substantial thermal management challenge because a significant quantity of heat must be dispersed within the aircraft system.
High power electronics typically use liquid cooling systems, which have installation and placement restrictions. These systems include coolant pumps, tanks, heat exchangers, ducts, and tubes.
Moreover, the normal coolant liquid needs to be treated carefully during maintenance. The adjustable arrangement of the power electronics is made possible by the air-cooling technology, which is both environmentally and humanely friendly.
Sl no | Topic |
1 | Market Segmentation |
2 | Scope of the report |
3 | Abbreviations |
4 | Research Methodology |
5 | Executive Summary |
6 | Introduction |
7 | Insights from Industry stakeholders |
8 | Cost breakdown of Product by sub-components and average profit margin |
9 | Disruptive innovation in the Industry |
10 | Technology trends in the Industry |
11 | Consumer trends in the industry |
12 | Recent Production Milestones |
13 | Component Manufacturing in US, EU and China |
14 | COVID-19 impact on overall market |
15 | COVID-19 impact on Production of components |
16 | COVID-19 impact on Point of sale |
17 | Market Segmentation, Dynamics and Forecast by Geography, 2023-2030 |
18 | Market Segmentation, Dynamics and Forecast by Product Type, 2023-2030 |
19 | Market Segmentation, Dynamics and Forecast by Application, 2023-2030 |
20 | Market Segmentation, Dynamics and Forecast by End use, 2023-2030 |
21 | Product installation rate by OEM, 2023 |
22 | Incline/Decline in Average B-2-B selling price in past 5 years |
23 | Competition from substitute products |
24 | Gross margin and average profitability of suppliers |
25 | New product development in past 12 months |
26 | M&A in past 12 months |
27 | Growth strategy of leading players |
28 | Market share of vendors, 2023 |
29 | Company Profiles |
30 | Unmet needs and opportunity for new suppliers |
31 | Conclusion |
32 | Appendix |