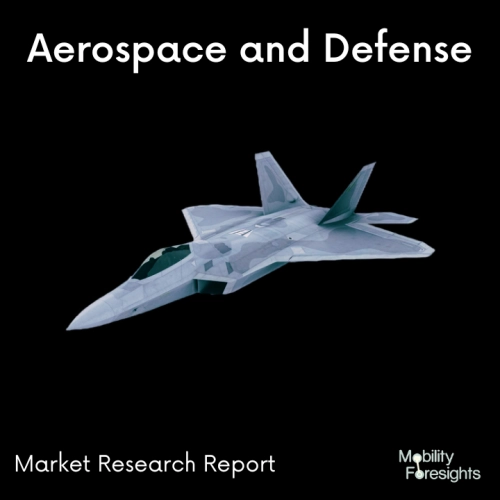
- Get in Touch with Us
Last Updated: Apr 25, 2025 | Study Period: 2023-2030
Plastic molding sheet is an essential material used to produce strong lightweight parts for interior and exterior aircraft applications.
It is made up of strong, lightweight sheets of plastic and is typically manufactured from a variety of thermoplastic polymers including Acrylonitrile Butadiene Styrene (ABS), Polycarbonate, and Polyethylene Terephthalate (PET).
With its high mechanical properties, plastic molding sheets enable aircraft parts to be lightweight yet still strong enough to meet the required safety standards.
Due to its manufacturability, plastic molding sheet has been used extensively in the production of aircraft interior and exterior components, such as seats and panels. It is also used to create windows, wings, and wingspans.
The plastic molding sheet offers designers a higher level of flexibility, allowing for the creation of detailed designs and intricate forms.
The process of forming a plastic sheet involves heated molds, a sheet of plastic material, and pressure. The mold is heated to a temperature that softens the plastic sheet and then pressure is applied.
The heated mold and plastic form a final product and the heat and pressure are released and the plastic cools. After cooling, the formed plastic sheet can be trimmed, cured and painted for an array of aircraft components.
Plastic molding sheet is now a widely used material for completed aircraft parts. Its ability to produce lightweight yet strong components makes it a desirable choice for aircraft designers and manufacturers.
Combined with its manufacturability, plastic molding sheet is an effective, cost efficient material for aircraft parts.
The Global aircraft plastic molding sheet market accounted for $XX Billion in 2022 and is anticipated to reach $XX Billion by 2030, registering a CAGR of XX% from 2023 to 2030.
Through the process of injection moulding, Superior Plastics develops plastic components utilised in the aircraft industry. Superior Plastics has both, having constructed injection moulds for more than 30 years.Using a specially made mould to produce a plastic product is called injection moulding. Moldable plastic that can be moulded into any shape is created by the mould. During this procedure, molten polymer grains are typically pumped into the mould.
It is possible to shape the molten plastic into almost any shape. The chemical can be applied in almost any field thanks to its adaptability. These multipurpose goods can only be produced by first customising and creating the moulds from which they are built.
A crucial step in producing components for aircraft engineering is injection moulding. Turbine housings, turbine blades, and pin mapsâwhich are used to mould carbon or glass fibres into sheet applicationsâare examples of aerospace parts made using injection moulding. To make sure the components fulfil performance requirements, designers and engineers collaborate closely.
The highest level of precision is required when creating moulded parts for the aerospace sector. Only flawless specs and precise measurements can be used to create the pieces. The products' ability to withstand the harsh conditions needed in aerospace applications is a result of this attention to detail.
Apart from constructing moulds and producing parts via aerospace plastic injection moulding methods, Superior Plastics also offers labelling and drop shipping services. These extra possibilities can be quite beneficial for aerospace sector companies that already have a clientele.
Not only can Superior Plastics produce a product, but it can also ship it under the corporate name. Superior may manufacture big numbers on behalf of a client if the client lacks the means to do so on its own, once more including the client's business name. By saving the client money, these actions increase revenue and free time.
Sl no | Topic |
1 | Market Segmentation |
2 | Scope of the report |
3 | Abbreviations |
4 | Research Methodology |
5 | Executive Summary |
6 | Introduction |
7 | Insights from Industry stakeholders |
8 | Cost breakdown of Product by sub-components and average profit margin |
9 | Disruptive innovation in the Industry |
10 | Technology trends in the Industry |
11 | Consumer trends in the industry |
12 | Recent Production Milestones |
13 | Component Manufacturing in US, EU and China |
14 | COVID-19 impact on overall market |
15 | COVID-19 impact on Production of components |
16 | COVID-19 impact on Point of sale |
17 | Market Segmentation, Dynamics and Forecast by Geography, 2023-2030 |
18 | Market Segmentation, Dynamics and Forecast by Product Type, 2023-2030 |
19 | Market Segmentation, Dynamics and Forecast by Application, 2023-2030 |
20 | Market Segmentation, Dynamics and Forecast by End use, 2023-2030 |
21 | Product installation rate by OEM, 2023 |
22 | Incline/Decline in Average B-2-B selling price in past 5 years |
23 | Competition from substitute products |
24 | Gross margin and average profitability of suppliers |
25 | New product development in past 12 months |
26 | M&A in past 12 months |
27 | Growth strategy of leading players |
28 | Market share of vendors, 2023 |
29 | Company Profiles |
30 | Unmet needs and opportunity for new suppliers |
31 | Conclusion |
32 | Appendix |