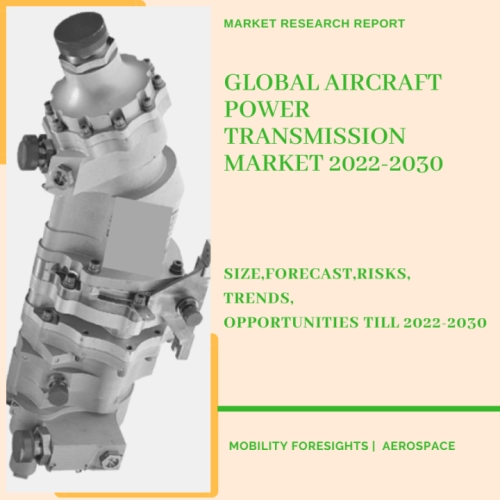
- Get in Touch with Us
Last Updated: Apr 25, 2025 | Study Period: 2022-2030
In the case that a second hydraulic system on an aircraft fails or is switched off, a power transfer unit (PTU) is a mechanism that switches hydraulic power from one system to another.
When, for instance, the right hydraulic system is under pressure but the left hydraulic system is not, the PTU is used.
The global aircraft power transmission market accounted for $XX Billion in 2021 and is anticipated to reach $XX Billion by 2030, registering a CAGR of XX% from 2022 to 2030.
The global market for aircraft mechanical power transmission systems is being driven by an increase in aircraft deliveries brought on by an increase in air travel. Additionally, factors including rising demand for Pure-Power Geared Turbofan (GTF) engines, a growing fleet of aircraft, technological breakthroughs in gearboxes, and the development of lightweight gearboxes are driving the market for aviation mechanical power transmission systems.
Another key aspect that is anticipated to drive the worldwide aircraft mechanical power transmission system market is the great organic expansion of both civil and military aviation, along with ongoing technological advancements that make equipment essential.
High initial and ongoing costs, however, can impede the market's expansion for mechanical power transmission systems for airplanes. Moreover, during the forecast period, the integration of artificial intelligence and automation is anticipated to open up new market opportunities for the aircraft mechanical power transmission system market.
The aerospace industry has experienced a strong demand for gearboxes in recent years due to the excellent organic growth of both civil and military aviation as well as ongoing technological advancements, which make equipment essential. One of the largest consumers of the mechanical power transmission system in which gearboxes play the most important role has been the aircraft sector.
According to GE, it has successfully completed the first test of a hybrid electric propulsion system with a megawatt (MW) class and multiple kilovolts (kV) in an environment that simulates a single-aisle commercial flight.
The high power, high voltage system test, which examined the electric motor/generators, power converters, power transmission, and power control systems, effectively illustrated the functionality of the parts in a situation that closely resembled flight. This supports the architecture of the GE-developed hybrid electric propulsion systems.
GE is honoured to have partnered with NASA for many years in the development of cutting-edge aviation technologies. By successfully completing the first test of a high power, high voltage hybrid electric system at altitude, they have recently accomplished a significant milestone.
The AGB NG, a new power transmission system from Safran Transmission Systems, will be unveiled (accessory gear box â next generation). The needs of the upcoming generation of aviation engines are being met by this innovative architecture.
The AGB NG, which was created as part of the extensive European research project Clean Sky 2, has a cutting-edge architecture that makes it easier for it to be integrated with the engine and nacelle.
The AGB NG is now situated in the engine's core area, next to the high-pressure compressor. By allowing a nacelle with a lower diameter, which in turn reduces aerodynamic drag, moving this location aids in reducing fuel consumption.
In order to help efforts to make air travel more fuel-efficient and lower CO2 emissions, Avio Aero, a division of GE Aerospace, has started a new technology demonstration programme. This programme will advance the development of hybrid electric propulsion technologies for commercial aviation.
In a recently concluded deal, the Clean Aviation Joint Undertaking of the European Commission awarded roughly â¬34 million over four years to a group led by Avio Aero for the AMBER demonstrator. It is intended to develop, integrate, and validate essential technologies required for a megawatt (MW)-class hydrogen fuel cell-powered hybrid-electric propulsion system.
The AMBER hybrid-electric initiative, which intends to illustrate the advantages of a cutting-edge aircraft propulsion system linking a turbine engine with a fuel cell-powered electric motor, has been launched, and the team is happy to do so. This demonstrates the desire to create, develop, and test ground-breaking technology to help shape the future of more environmentally friendly aviation in Europe.
Their AMBER proposal's acceptance and grant by Clean Aviation demonstrates its strategic and technological relevance in support of the European Union's goal of achieving net-zero CO2 emissions from flight. Technologies for hybrid electric propulsion can enhance engine performance while lowering fuel consumption and pollutants.
The hybrid electric technologies Avio Aero and its parent company GE Aerospace are developing are also compatible with cutting-edge engine layouts like open fans and alternative fuels like sustainable aviation fuel (SAF). To achieve these goals, the Clean Aviation cooperation with industry helps hasten innovation of critical technologies like electrification.
A total of 21 members from Europe make up the Avio Aero-led collaboration, including the universities and R&D facilities that make up Avio Aero's European technology development network.
The Czech Republic, Germany, Poland, Turkey, and other GE Aerospace locations in Europe will contribute to the study of the engine, propeller, and electric powertrain systems. One of their 20 audacious new projects currently under way, the AMBER project, will be crucial in assisting them in meeting this lofty goal.
Sl no | Topic |
1 | Market Segmentation |
2 | Scope of the report |
3 | Abbreviations |
4 | Research Methodology |
5 | Executive Summary |
6 | Introduction |
7 | Insights from Industry stakeholders |
8 | Cost breakdown of Product by sub-components and average profit margin |
9 | Disruptive innovation in the Industry |
10 | Technology trends in the Industry |
11 | Consumer trends in the industry |
12 | Recent Production Milestones |
13 | Component Manufacturing in US, EU and China |
14 | COVID-19 impact on overall market |
15 | COVID-19 impact on Production of components |
16 | COVID-19 impact on Point of sale |
17 | Market Segmentation, Dynamics and Forecast by Geography, 2022-2030 |
18 | Market Segmentation, Dynamics and Forecast by Product Type, 2022-2030 |
19 | Market Segmentation, Dynamics and Forecast by Application, 2022-2030 |
20 | Market Segmentation, Dynamics and Forecast by End use, 2022-2030 |
21 | Product installation rate by OEM, 2022 |
22 | Incline/Decline in Average B-2-B selling price in past 5 years |
23 | Competition from substitute products |
24 | Gross margin and average profitability of suppliers |
25 | New product development in past 12 months |
26 | M&A in past 12 months |
27 | Growth strategy of leading players |
28 | Market share of vendors, 2022 |
29 | Company Profiles |
30 | Unmet needs and opportunity for new suppliers |
31 | Conclusion |
32 | Appendix |