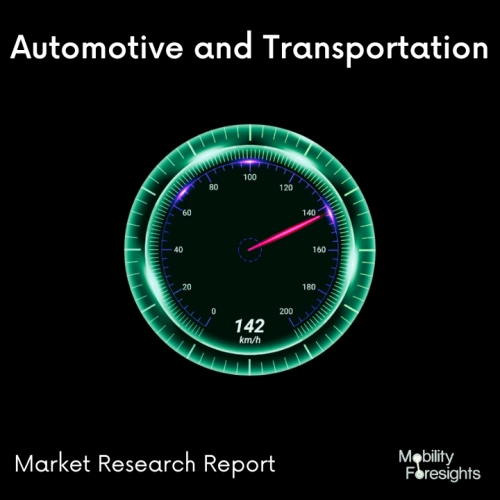
- Get in Touch with Us
Last Updated: Apr 25, 2025 | Study Period: 2024-2030
The unique properties of aluminium alloys provide the opportunity to develop lightweight, cost-effective constructions with high rigidity and outstanding capacity for absorbing impact energy.
Aluminium is therefore the material of choice to assure the safety of the car and its occupants while also meeting associated needs like protecting pedestrians and having minimal maintenance costs, etc. Applications range from crash boxes, bumper beams, and aluminium side impact beams to full structural modules.
Aluminium structures that are crashworthy are the product of a comprehensive systems approach that takes into consideration the advantages brought about by specially designed alloy characteristics, design principles, and suitable fabrication techniques.
The extrusion technology is a key component of cost-effective manufacturing methods for aluminium components. Extruded aluminium profiles can be securely connected using a variety of techniques, and they can be integrated with other aluminium product shapes, steel, or other materials to create full structural modules.
Aluminium crash management solutions are extremely adaptable and allow for quick and simple alterations to accommodate for individual crash situations, lowering both development times and costs. This is due to the low cost of the extrusion tools and the short lead times for tool fabrication.
TheGlobal aluminium Crash Management System marketaccounted for $XX Billion in 2023 and is anticipated to reach $XX Billion by 2030, registering a CAGR of XX% from 2024 to 2030.
Constellium N. announced the release of new Crash Management Systems (CMS) technology made of high-strength aluminium that is intended for the front and back of a vehicle for improved structural protection in the event of a collision.
The features of the 6xxx family of aluminium alloys, including formability, corrosion resistance, energy absorption, and recyclability, are combined with high-strength mechanical performance in Constellium's new-generation CMS.
The design freedom (i.e., the ability to produce multi-chamber profiles with different wall thicknesses) and cost-effectiveness of the aluminium extrusion technique are the primary factors driving this desire.
Sl no | Topic |
1 | Market Segmentation |
2 | Scope of the report |
3 | Abbreviations |
4 | Research Methodology |
5 | Executive Summary |
6 | Introduction |
7 | Insights from Industry stakeholders |
8 | Cost breakdown of Product by sub-components and average profit margin |
9 | Disruptive innovation in the Industry |
10 | Technology trends in the Industry |
11 | Consumer trends in the industry |
12 | Recent Production Milestones |
13 | Component Manufacturing in US, EU and China |
14 | COVID-19 impact on overall market |
15 | COVID-19 impact on Production of components |
16 | COVID-19 impact on Point of sale |
17 | Market Segmentation, Dynamics and Forecast by Geography, 2024-2030 |
18 | Market Segmentation, Dynamics and Forecast by Product Type, 2024-2030 |
19 | Market Segmentation, Dynamics and Forecast by Application, 2024-2030 |
20 | Market Segmentation, Dynamics and Forecast by End use, 2024-2030 |
21 | Product installation rate by OEM, 2023 |
22 | Incline/Decline in Average B-2-B selling price in past 5 years |
23 | Competition from substitute products |
24 | Gross margin and average profitability of suppliers |
25 | New product development in past 12 months |
26 | M&A in past 12 months |
27 | Growth strategy of leading players |
28 | Market share of vendors, 2023 |
29 | Company Profiles |
30 | Unmet needs and opportunity for new suppliers |
31 | Conclusion |
32 | Appendix |