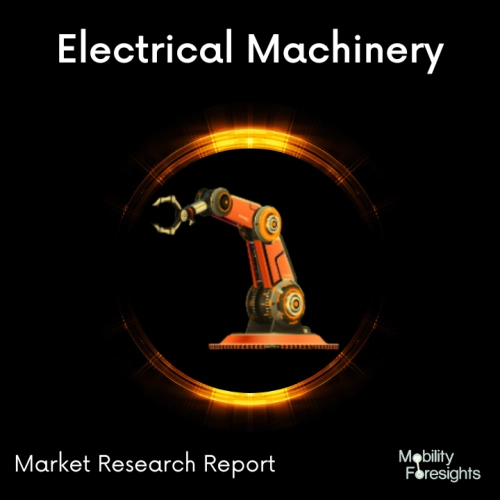
- Get in Touch with Us
Last Updated: Apr 25, 2025 | Study Period: 2024-2030
The most common way to weld aluminum is this one. Tungsten Inert Gas Welding is another name for it. You won't have to deal with feedability issues because this method doesn't require mechanical wire feeding.
ER4043 and ER5356 are the most frequently utilized MIG aluminum welding wires. MIG welding wire ER4043 is used to weld aluminum alloys 2014, 3003, 3004, 4043, 5052, 6061, 6062, and 6063.
The welds have a high ductility and excellent cracking resistance.
While MIG and TIG are the most common methods for welding aluminum, there are a number of other welding techniques that can be utilized, including Laser shaft and electron bar welding: For aluminum, beam welding is a common method.
Gas tungsten arc welding (GTAW), also known as tungsten inert gas (TIG) welding, is one of the most common methods of welding aluminum.
Because it does not require mechanical wire feeding, which can cause feedability issues, GTAW is an excellent process for aluminum. Aluminum is a gentler metal than copper, furthermore being inclined to harm during establishment, it likewise grows more when warmed.
The wire's expansion and contraction can cause the wire to creep out from under the screw that holds it in place, resulting in loose wires and overheating.
TheGlobal Aluminium Welding Wires Marketaccounted for $XX Billion in 2023 and is anticipated to reach $XX Billion by 2030, registering a CAGR of XX% from 2024 to 2030.
A type of welding wire used to weld aluminum are aluminum welding wires. There are numerous varieties of aluminum welding wires on the market, each with distinct advantages and disadvantages.
MIG welding is the most common application for aluminum welding wires. MIG is a type of welding that uses an electrode made of a consumable wire to create an arc between the workpiece and the electrode. MIG stands for Metal Inert Gas.
A torch is the conduit through which the electrode receives its supply of shielding gas. Argon is the most frequently used shielding gas in MIG welding.
Argon is an excellent gas for MIG welding because it is inert and does not react with the aluminum or weld pool. Helium, carbon dioxide, and combinations of these gases are additional shielding gases that can be utilized in MIG welding.
Because it produces very clean welds with little smoke and spatter, MIG welding is ideal for welding aluminum. Additionally, it is relatively simple to learn and use, making it a popular option for people who are just starting out in welding.
TIG represents Tungsten Latent Gas, and is one more kind of welding that can be utilized to weld aluminum. A non-consumable tungsten electrode is used in TIG welding to form an arc between the workpiece and the electrode.
The new Millermatic 350P car body aluminium repair system, which was introduced by Miller Electric Mfg. Co., is a comprehensive welding package made to facilitate repairs to aluminium auto body panels and beds, like those on the Ford F-150 truck, while also delivering high-quality welds.
The use of aluminium in the automobile industry is on the rise, and this turnkey solution addresses the issue.It has been specially created to overcome the problems associated with welding thin gauge aluminium, such as warping, distortion, and burn-through.
It enhances the dependable functionality of the well-known Miller® Millermatic 350P MIG power source and may also be used to pulse weld with silicon bronze, steel, and stainless steel wires.
Miller has contributed to the simplification of the aluminium welding process, particularly for welding operators who may not be as experienced with this material or the difficulties it can present.
This has been done by giving all the components required for creating aluminium vehicle bodies in a single optimised package.
The Millermatic 350P auto body aluminium repair system is equipped with the elements required to carry out weld repairs on the Ford F-150 aluminium-body truck in accordance with the requirements established by Ford and the Assurance Performance Network.
According to these standards, aluminium welding with.047-inch (1.2mm) 5554 series aluminium alloy wire requires a 220V power source with Pulsed MIG capability.
The Millermatic system has improved low-end Pulse MIG programmes specifically designed for aluminium welding, and it offers 300-amp output at a 60 percent duty cycle.
When welding on aluminium auto body panels, the low-end wire feed speed capabilities have been decreased from 105 inches per minute (IPM) to 75 IPM, requiring less heat input to prevent burn-through and warping.
The new Millermatic 350P car body aluminium repair system includes an aluminium Pulse Hot Start that automatically gives extra power to minimise "cold starts' ' typical of welding this material.
This power source is identical to the conventional Millermatic 350P MIG power source. Because of the system's line voltage correction, output remains consistent even when input power fluctuates.
When cooling the power source, a Fan-On-DemandTM cooling system only activates when necessary, consuming less power and lowering the likelihood that pollutants may be sucked into the machine.
With a 12-foot cable, plastic liner, and 30-degree head tube for the best possible transmission of aluminium wire, the BernardTM Q200 aluminium MIG gun is specially designed. Millermatic 350P, a single-phase or three-phase power source with voltage ranges of 200, 230, and 460.
Sl no | Topic |
1 | Market Segmentation |
2 | Scope of the report |
3 | Abbreviations |
4 | Research Methodology |
5 | Executive Summary |
6 | Introduction |
7 | Insights from Industry stakeholders |
8 | Cost breakdown of Product by sub-components and average profit margin |
9 | Disruptive innovation in the Industry |
10 | Technology trends in the Industry |
11 | Consumer trends in the industry |
12 | Recent Production Milestones |
13 | Component Manufacturing in US, EU and China |
14 | COVID-19 impact on overall market |
15 | COVID-19 impact on Production of components |
16 | COVID-19 impact on Point of sale |
17 | Market Segmentation, Dynamics and Forecast by Geography, 2024-2030 |
18 | Market Segmentation, Dynamics and Forecast by Product Type, 2024-2030 |
19 | Market Segmentation, Dynamics and Forecast by Application, 2024-2030 |
20 | Market Segmentation, Dynamics and Forecast by End use, 2024-2030 |
21 | Product installation rate by OEM, 2023 |
22 | Incline/Decline in Average B-2-B selling price in past 5 years |
23 | Competition from substitute products |
24 | Gross margin and average profitability of suppliers |
25 | New product development in past 12 months |
26 | M&A in past 12 months |
27 | Growth strategy of leading players |
28 | Market share of vendors, 2023 |
29 | Company Profiles |
30 | Unmet needs and opportunity for new suppliers |
31 | Conclusion |
32 | Appendix |