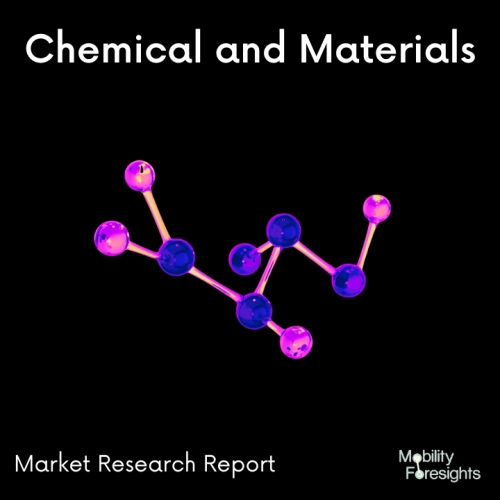
- Get in Touch with Us
Last Updated: Apr 25, 2025 | Study Period: 2024-2030
Aluminum Copper Silicon alloys are also heat-hardenable and high-strength, but they are also corrosive and less castable, albeit still sufficiently so. Most frequently, it is smelted from secondary aluminum.
Similar to how AlCu alloys harden, so do these materials. It contains between 1% and 4% copper and between 4% and 10% silicon. Magnesium supplements increase strength.
The Global Aluminum Copper Silicon Alloy Market accounted for $XX Billion in 2023 and is anticipated to reach $XX Billion by 2030, registering a CAGR of XX% from 2024 to 2030.
A promising metallic phase change material, the Aluminum Copper Silicon Alloy Al-25% Cu-6% Si (wt%) operates best between 508°C and 548°C. Experimental findings revealed the alloy's melting point, latent heat of fusion, and room temperature density.
The measured parameters throughout an operating range of 160°C to 660°C were used to determine an energy density of 0.7764 0.0178 kWh L. From heat capacity DSC tests, thermal diffusivity light flash observations, and density calculations, the alloy's temperature-dependent thermal conductivity was estimated.
After two weeks at 600°C, it was discovered that the eutectic was compatible with alumina and graphite but not with iron or stainless steel (304 grade). As building materials, graphite and alumina are advised.
In particular, the provision of heat in electric cars, latent thermal storage in metals can solve numerous problems relating to the temporal or spatial intermittency of heat resources. The most desirable alloys for thermal storage applications are those that are both energy dense and thermally conductive.
The ideal metallic phase change material melting in the range of 508°C to 548°C has been found to be the Aluminum Copper Silicon Alloy Al-25% Cu-6% Si (wt%).
The thermal and compatibility properties of this alloy are experimentally evaluated using differential scanning calorimetry, light flash analysis, and long-term reaction studies.
After two weeks at 550°C, graphite and alumina are seen as the alloy's appropriate housing materials. Using energy-dispersive X-ray spectroscopy, the depth of the reaction and the products at the interface between iron and stainless steel are determined.
Sl no | Topic |
1 | Market Segmentation |
2 | Scope of the report |
3 | Abbreviations |
4 | Research Methodology |
5 | Executive Summary |
6 | Introduction |
7 | Insights from Industry stakeholders |
8 | Cost breakdown of Product by sub-components and average profit margin |
9 | Disruptive innovation in the Industry |
10 | Technology trends in the Industry |
11 | Consumer trends in the industry |
12 | Recent Production Milestones |
13 | Component Manufacturing in US, EU and China |
14 | COVID-19 impact on overall market |
15 | COVID-19 impact on Production of components |
16 | COVID-19 impact on Point of sale |
17 | Market Segmentation, Dynamics and Forecast by Geography, 2024-2030 |
18 | Market Segmentation, Dynamics and Forecast by Product Type, 2024-2030 |
19 | Market Segmentation, Dynamics and Forecast by Application, 2024-2030 |
20 | Market Segmentation, Dynamics and Forecast by End use, 2024-2030 |
21 | Product installation rate by OEM, 2023 |
22 | Incline/Decline in Average B-2-B selling price in past 5 years |
23 | Competition from substitute products |
24 | Gross margin and average profitability of suppliers |
25 | New product development in past 12 months |
26 | M&A in past 12 months |
27 | Growth strategy of leading players |
28 | Market share of vendors, 2023 |
29 | Company Profiles |
30 | Unmet needs and opportunity for new suppliers |
31 | Conclusion |
32 | Appendix |