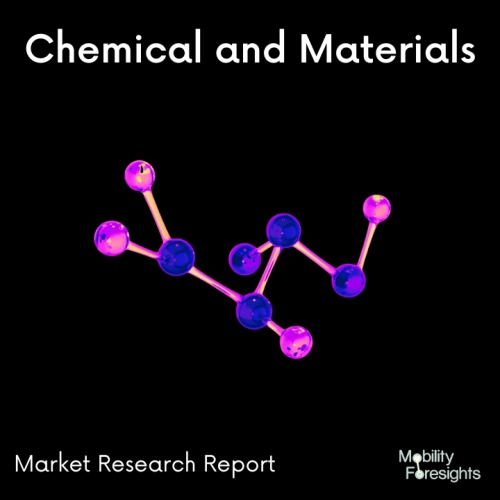
- Get in Touch with Us
Last Updated: Apr 25, 2025 | Study Period: 2024-2030
A type of packaging material that combines the characteristics of both aluminum and plastic is aluminum plastic film, often referred to as an aluminum-plastic composite film. Due to its adaptability, it is frequently utilized across a variety of industries. The film is made up of several layers, usually with layers of plastic like polyethylene or polypropylene sandwiching a thin sheet of aluminum foil.
While the aluminum layer offers good light, oxygen, and gas barriers, the plastic layers offer flexibility, heat-sealing capabilities, and defense against moisture and other environmental conditions. The film's use of aluminum and plastic has a number of benefits. It offers a strong barrier that shields the contents from contaminants like moisture, mist, and scents.
The film also has good heat-sealing capabilities, making it simple to seal in order to make packaging that is airtight and tamper-evident.Additionally, the aluminum layer offers a reflective surface that, by obstructing light and UV rays, can aid in keeping the freshness and increasing the shelf life of the packaged goods. Pharmaceuticals, cosmetics, electronics, and industrial products, as well as food and beverage packaging, all use aluminum plastic film.
Snacks, coffee, pet food, prescription tablets and capsules, and electrical components are all frequently packaged using this method. To meet individual packaging needs, the film is offered in various thicknesses, hues, and finishes. Aluminum plastic film is a common choice for packaging applications where preservation, durability, and product integrity are critical concerns because it combines protective, barrier, and sealing capabilities.
The Global Aluminum Plastic Film Market accounted for $XX Billion in 2023 and is anticipated to reach $XX Billion by 2030, registering a CAGR of XX% from 2024 to 2030.
There are now two primary methods of manufacturing aluminum plastic sheets for lithium batteries, one dry (represented by Showa in Japan) and the other thermal (represented by DNP in Japan).
Showa Japan and Sony Japan together created the dry process production method. Showa's dry method in Japan employs a follow-up agent since Sony's electrolyte is solid and does not require the functionality of aluminum plasticizer electrolytic fluid. The lithium battery aluminum plastic film's service life is somewhat impacted by the secondary agent's rather weak electrolytic performance.
Sl no | Topic |
1 | Market Segmentation |
2 | Scope of the report |
3 | Abbreviations |
4 | Research Methodology |
5 | Executive Summary |
6 | Introduction |
7 | Insights from Industry stakeholders |
8 | Cost breakdown of Product by sub-components and average profit margin |
9 | Disruptive innovation in the Industry |
10 | Technology trends in the Industry |
11 | Consumer trends in the industry |
12 | Recent Production Milestones |
13 | Component Manufacturing in US, EU and China |
14 | COVID-19 impact on overall market |
15 | COVID-19 impact on Production of components |
16 | COVID-19 impact on Point of sale |
17 | Market Segmentation, Dynamics and Forecast by Geography, 2024-2030 |
18 | Market Segmentation, Dynamics and Forecast by Product Type, 2024-2030 |
19 | Market Segmentation, Dynamics and Forecast by Application, 2024-2030 |
20 | Market Segmentation, Dynamics and Forecast by End use, 2024-2030 |
21 | Product installation rate by OEM, 2023 |
22 | Incline/Decline in Average B-2-B selling price in past 5 years |
23 | Competition from substitute products |
24 | Gross margin and average profitability of suppliers |
25 | New product development in past 12 months |
26 | M&A in past 12 months |
27 | Growth strategy of leading players |
28 | Market share of vendors, 2023 |
29 | Company Profiles |
30 | Unmet needs and opportunity for new suppliers |
31 | Conclusion |
32 | Appendix |