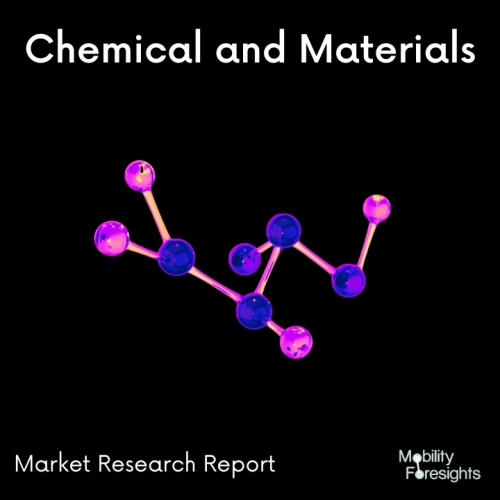
- Get in Touch with Us
Last Updated: Apr 25, 2025 | Study Period: 2024-2030
The base or foundation for many different sorts of products, including printed circuit boards (PCBs), thin-film solar cells, and LEDs, is made of aluminum substrates.
A wafer is a piece of semiconductor material that is shaped like a very thin disc and made of silicon, one of the most prevalent semiconductors in use today. Silicon-based photovoltaic cells and electronic integrated circuits (ICs) are both made from wafers. The wafer acts as the substrate in these designs.
Aluminum is a light, silvery-white metal. It is bendable and soft. Many items, such as cans, foil, culinary utensils, window frames, beer kegs, and airplane components, are made of aluminum. This is as a result of its unique characteristics.
The Global Aluminum Wafer market accounted for $XX Billion in 2023 and is anticipated to reach $XX Billion by 2030, registering a CAGR of XX% from 2024 to 2030.
Aluminum substrates are components that serve as the framework or platform for a variety of goods, including printed circuit boards (PCBs), thin-film solar cells, and LEDs. Good electrical and thermal conductivity, great strength, and low weight are just a few benefits of using aluminum as a substrate material.
Because they can help to increase the performance and dependability of electronic devices, aluminum substrates are frequently employed in the electronics sector. Due to their high strength and low weight, they are also utilized in the automotive and aerospace industries.
Many products, including solar cells, semiconductor chips, and other electrical devices, can be made from aluminum wafers. Aluminum wafers are extremely robust and unbreakable. They are the ideal choice for semiconductors because of their great density.
They also satisfy the needs of the semiconductor industry. They are simple to handle and can be packaged without compromising the end products' quality or shape.
Moreover, they are unbreakable. They are therefore appropriate for a wide range of applications. Aluminum wafers are the ideal option if they require a high-quality, long-lasting material. There are several uses for aluminum substrates in semiconductor applications.
They can be applied to lattice strain, power diodes, and thin-film substrates. There are many different sizes and forms in which aluminum wafers can be made. They are resistant to breaking no matter what shape they are. They also satisfy the criteria for producing semiconductors.
For instance, they can make high-speed computer circuits and thin-film transistors using an aluminum alloy plate. With these materials, they can also produce different kinds of materials. It will be challenging for them to select one that will meet their needs.
Sl no | Topic |
1 | Market Segmentation |
2 | Scope of the report |
3 | Abbreviations |
4 | Research Methodology |
5 | Executive Summary |
6 | Introduction |
7 | Insights from Industry stakeholders |
8 | Cost breakdown of Product by sub-components and average profit margin |
9 | Disruptive innovation in the Industry |
10 | Technology trends in the Industry |
11 | Consumer trends in the industry |
12 | Recent Production Milestones |
13 | Component Manufacturing in US, EU and China |
14 | COVID-19 impact on overall market |
15 | COVID-19 impact on Production of components |
16 | COVID-19 impact on Point of sale |
17 | Market Segmentation, Dynamics and Forecast by Geography, 2024-2030 |
18 | Market Segmentation, Dynamics and Forecast by Product Type, 2024-2030 |
19 | Market Segmentation, Dynamics and Forecast by Application, 2024-2030 |
20 | Market Segmentation, Dynamics and Forecast by End use, 2024-2030 |
21 | Product installation rate by OEM, 2023 |
22 | Incline/Decline in Average B-2-B selling price in past 5 years |
23 | Competition from substitute products |
24 | Gross margin and average profitability of suppliers |
25 | New product development in past 12 months |
26 | M&A in past 12 months |
27 | Growth strategy of leading players |
28 | Market share of vendors, 2023 |
29 | Company Profiles |
30 | Unmet needs and opportunity for new suppliers |
31 | Conclusion |
32 | Appendix |