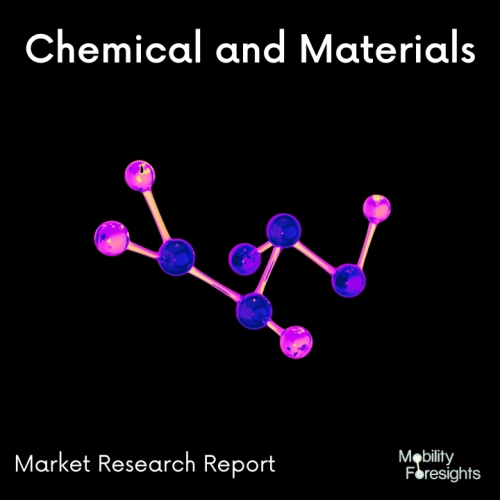
- Get in Touch with Us
Last Updated: Apr 25, 2025 | Study Period: 2024-2030
To lessen reflections and increase light transmission, antireflection (AR) film is a thin coating or film that is placed to the surface of optical elements such as lenses, windows, and displays.
Antireflection film's main goal is to reduce light loss from unintentional reflections, improving the effectiveness and clarity of optical systems.
A fraction of the light that travels from one medium to another (for instance, from air to glass or vice versa) is reflected at the interface of the two materials.
For optical devices, such as cameras, eyeglasses, microscopes, projectors, and other optical devices, this reflection can cause glare, ghost images, and diminished contrast.
The interference concept underlies the operation of antireflection films.
Metal oxides, such as magnesium fluoride and titanium dioxide, or dielectric materials, such as silicon dioxide, can be used to create antireflection films.
Utilizing methods like vacuum deposition or sputtering, these compounds are deposited on the optical surface.
In optical instruments like as binoculars, telescopes, microscopes, and eyeglasses, where minimizing reflections and optimizing light transmission are crucial for optimum performance, AR films are frequently used.
It's important to keep in mind that although AR films can greatly minimize reflections, they cannot entirely do away with them.
To further improve their performance, some high-quality optical components may also have numerous antireflection coating layers.
They are made to have a particular thickness and refractive index that cancel out reflections from the coated object's front and back surfaces.
The Global Antireflection Film market accounted for $XX Billion in 2023 and is anticipated to reach $XX Billion by 2030, registering a CAGR of XX% from 2024 to 2030.
ZYGO's top-notch coating design engineers and technicians collaborate closely with our metrology and optical manufacturing teams to give our clients the benefit of "one-stop shopping."
This shortens the entire timetable, lowers program risks, and streamlines your supply chain.
Choosing a single, vertically integrated manufacturer is essential if you want to ensure that your substrate will satisfy all specifications after a coating has been applied. improved and shielded metals.
The UV to MWIR spectral spectrum (248 nm to 5 m), Broadband (BBAR), single or dual band, plus custom designs, and AR coating over EMI gridding are among the characteristics of antireflective coatings.
Filters, beamsplitters, and high LIDT, including femtosecond laser applications.
After coating, ZYGO's state-of-the-art metrology equipment validate all specifications.
Sl no | Topic |
1 | Market Segmentation |
2 | Scope of the report |
3 | Abbreviations |
4 | Research Methodology |
5 | Executive Summary |
6 | Introduction |
7 | Insights from Industry stakeholders |
8 | Cost breakdown of Product by sub-components and average profit margin |
9 | Disruptive innovation in the Industry |
10 | Technology trends in the Industry |
11 | Consumer trends in the industry |
12 | Recent Production Milestones |
13 | Component Manufacturing in US, EU and China |
14 | COVID-19 impact on overall market |
15 | COVID-19 impact on Production of components |
16 | COVID-19 impact on Point of sale |
17 | Market Segmentation, Dynamics and Forecast by Geography, 2024-2030 |
18 | Market Segmentation, Dynamics and Forecast by Product Type, 2024-2030 |
19 | Market Segmentation, Dynamics and Forecast by Application, 2024-2030 |
20 | Market Segmentation, Dynamics and Forecast by End use, 2024-2030 |
21 | Product installation rate by OEM, 2023 |
22 | Incline/Decline in Average B-2-B selling price in past 5 years |
23 | Competition from substitute products |
24 | Gross margin and average profitability of suppliers |
25 | New product development in past 12 months |
26 | M&A in past 12 months |
27 | Growth strategy of leading players |
28 | Market share of vendors, 2023 |
29 | Company Profiles |
30 | Unmet needs and opportunity for new suppliers |
31 | Conclusion |
32 | Appendix |