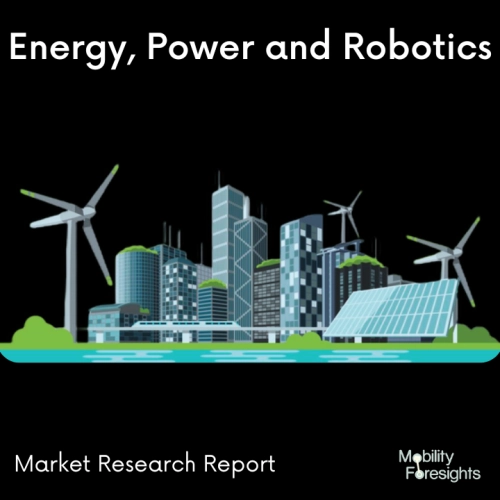
- Get in Touch with Us
Last Updated: Apr 25, 2025 | Study Period: 2023-2030
A battery separator that has an aramid layer or coating added to it is known as an aramid-coated separator. High-performance synthetic fiber known as Aramid is prized for its excellent toughness, heat resistance, and longevity. The qualities of the battery separator can be enhanced in a number of ways by covering the separator material with aramid.
The following are the main advantages and traits of aramid-coated separators for batteries:
Improved mechanical toughness: Aramid fibers have a remarkable tensile strength, such as those made from materials like Kevlar® or Nomex®. Aramid improves the mechanical characteristics of the separator when employed as a coating on battery separators, making it more resilient to tears, punctures, and deformation.This increased strength enhances the battery's overall safety and durability while assisting in the prevention of internal short circuits.
Thermal stability: Materials made of aramid have exceptional thermal resistance and can sustain high temperatures without suffering serious damage. Aramid improves the thermal stability of the battery when it is applied as a coating on the separator. Due to the decreased risk of thermal runaway and increased assurance that the battery can function dependably in challenging circumstances, this is particularly crucial in high-power or high-temperature battery applications.
Aramid fibers are capable of absorbing and holding onto electrolytes, which is essential for battery performance. Aramid can be added to the separator coating to increase the electrolyte retention capacity overall. This enhances the battery's performance and cycling stability by facilitating efficient ion transport and allowing for improved electrolyte distribution throughout the battery.
Dendrite formation obstruction: Aramid-coated separators can act as a barrier to prevent dendrite formation inside the battery. Dendrites, which are tiny metal filaments that can develop on the electrodes and lead to short circuits that compromise battery safety and performance, can form. The aramid layer aids in preventing dendrite formation, enhancing the cycle life and stability of the battery.
In sophisticated battery technologies like lithium-ion batteries, where performance, durability, and safety are essential factors, aramid-coated separators are frequently employed. Depending on the battery chemistry and application requirements, several aramid materials and coating techniques may be used.
Aramid coatings in battery separators provide enhanced mechanical strength, thermal stability, electrolyte absorption, and resistance to dendrite formation overall. These improvements make battery operation safer and more dependable, especially in demanding applications where durability and high performance are essential.
The Global Aramid Coated Separator Market accounted for $XX Billion in 2022 and is anticipated to reach $XX Billion by 2030, registering a CAGR of XX% from 2023 to 2030.
In a new collaboration, General Motors and Microvast will create battery separators for upcoming electric vehicles that will use the Ultium battery technology from GM. The Detroit, Michigan-based automotive giant recently announced a partnership with Texas-based battery maker Microvast to create battery separator technology for its expanding line of electric vehicles (EVs), which are powered by its Ultium system.
According to the press release, the separators will work with the majority of lithium-ion (Li-ion) cells, including those with anodes composed of graphite, silicon, and lithium, as well as lithium iron phosphate and high-voltage cathodes. The separators will be built to increase the thermal stability of batteries intended for electric vehicles, with the overall objective of enhancing battery life, charging, and safety.
Sl no | Topic |
1 | Market Segmentation |
2 | Scope of the report |
3 | Abbreviations |
4 | Research Methodology |
5 | Executive Summary |
6 | Introduction |
7 | Insights from Industry stakeholders |
8 | Cost breakdown of Product by sub-components and average profit margin |
9 | Disruptive innovation in the Industry |
10 | Technology trends in the Industry |
11 | Consumer trends in the industry |
12 | Recent Production Milestones |
13 | Component Manufacturing in US, EU and China |
14 | COVID-19 impact on overall market |
15 | COVID-19 impact on Production of components |
16 | COVID-19 impact on Point of sale |
17 | Market Segmentation, Dynamics and Forecast by Geography, 2023-2030 |
18 | Market Segmentation, Dynamics and Forecast by Product Type, 2023-2030 |
19 | Market Segmentation, Dynamics and Forecast by Application, 2023-2030 |
20 | Market Segmentation, Dynamics and Forecast by End use, 2023-2030 |
21 | Product installation rate by OEM, 2023 |
22 | Incline/Decline in Average B-2-B selling price in past 5 years |
23 | Competition from substitute products |
24 | Gross margin and average profitability of suppliers |
25 | New product development in past 12 months |
26 | M&A in past 12 months |
27 | Growth strategy of leading players |
28 | Market share of vendors, 2023 |
29 | Company Profiles |
30 | Unmet needs and opportunity for new suppliers |
31 | Conclusion |
32 | Appendix |