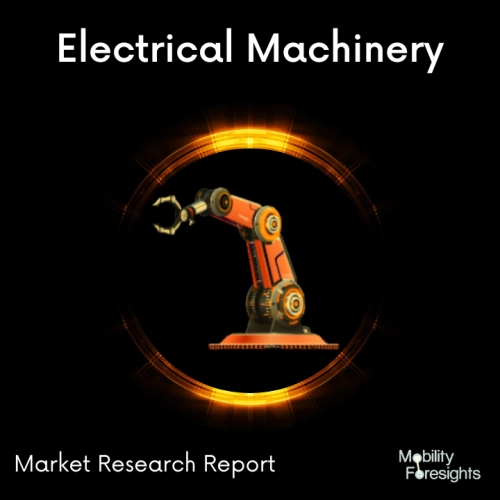
- Get in Touch with Us
Last Updated: Apr 25, 2025 | Study Period: 2024-2030
Atomic Layer Deposition (ALD), a cutting-edge deposition method, enables the highly controlled deposition of ultra-thin films that are only a few nanometers thick.
In addition to great thickness control and homogeneity, Atomic Layer Deposition also enables the coating of 3D structures with conformal materials for high aspect-ratio structures.
Due to its reliance on self-limiting surface reactions, Atomic Layer Deposition often offers extremely low pin-hole and particle levels, which might be advantageous for a variety of applications.
Numerous applications call for the high film quality, level of film and interface control that is offered. The use of plasma enables the control of film qualities, as well as a large variety of potential materials. Processing with little harm is made possible by the flexibility of certain surface pre-treatments.
The GlobalAtomic Layer Deposition Equipment Market accounted for $XX Billion in 2022 and is anticipated to reach $XX Billion by 2030, registering a CAGR of XX% from 2024 to 2030.
With its scalability and versatility to suit a wide range of applications and market areas, Beneq Transform creates a whole new class of ALD cluster tool solutions.
Beneq Transform is capable of being expanded later to accommodate increasing quantities or new ALD applications. It may be configured with numerous ALD process modules to satisfy specific wafer capacity requirements.
processing in batches or only one wafer. most diverse selection of high-performance oxides and nitrides. Make the most of your production options for flexible volume.
Beneq Transform offers unmatched flexibility in how processing sequences can be realised to meet the most demanding thin-film deposition requirements thanks to its flexible automation platform and unique capability to combine both thermal batch and plasma enhanced ALD process modules in one integrated system.
A large global chip manufacturer will get atomic layer deposition (ALD) equipment from the South Korean company Jusung Engineering Co. for use in system chips at a major Taiwanese foundry and a U.S. integrated device manufacturer.
The Guidance Series, a piece of ALD equipment created for the first time in the world, has successfully passed the test run by our international client.
After development, it typically takes two to three years for a chip equipment to be validated and put into mass production. Jusung Engineering has conducted testing with several clients as part of the cooperative development of an ALD apparatus with a major non-memory chip maker.
Jusung Engineering has previously concentrated on producing deposition equipment that coats wafers with the essential materials as part of the chip manufacturing process.
The ALD, as opposed to the current chemical vapour deposition, which creates layers in molecular units, enables the creation of a thin, layered chip film in atomic units for lamination. Along with extreme ultraviolet (EUV) processing equipment, the machinery is regarded as a necessary technology for the fabrication of small and high-performance chips, driven by Dutch and Japanese businesses.
As the sole supplier of ALD equipment to SK hynix Inc., Jusung Engineering in Korea is known for its technical expertise. However, because memory chip equipment makes up more than 90% of the overall chip industry, there have been growth constraints.
If Jusung Engineering starts selling ALD equipment to a manufacturer of non-memory chips, it should be able to diversify its business portfolio, which primarily consists of equipment for memory chips.
Contrary to the memory chip industry, which has a narrow range of applications, non-memory chips span a variety of industries, including logic, imaging, and sensors. It is estimated that the market will increase at a rate more than three times faster than that of memory chips.
Sl no | Topic |
1 | Market Segmentation |
2 | Scope of the report |
3 | Abbreviations |
4 | Research Methodology |
5 | Executive Summary |
6 | Introduction |
7 | Insights from Industry stakeholders |
8 | Cost breakdown of Product by sub-components and average profit margin |
9 | Disruptive innovation in the Industry |
10 | Technology trends in the Industry |
11 | Consumer trends in the industry |
12 | Recent Production Milestones |
13 | Component Manufacturing in US, EU and China |
14 | COVID-19 impact on overall market |
15 | COVID-19 impact on Production of components |
16 | COVID-19 impact on Point of sale |
17 | Market Segmentation, Dynamics and Forecast by Geography, 2024-2030 |
18 | Market Segmentation, Dynamics and Forecast by Product Type, 2024-2030 |
19 | Market Segmentation, Dynamics and Forecast by Application, 2024-2030 |
20 | Market Segmentation, Dynamics and Forecast by End use, 2024-2030 |
21 | Product installation rate by OEM, 2023 |
22 | Incline/Decline in Average B-2-B selling price in past 5 years |
23 | Competition from substitute products |
24 | Gross margin and average profitability of suppliers |
25 | New product development in past 12 months |
26 | M&A in past 12 months |
27 | Growth strategy of leading players |
28 | Market share of vendors, 2023 |
29 | Company Profiles |
30 | Unmet needs and opportunity for new suppliers |
31 | Conclusion |
32 | Appendix |